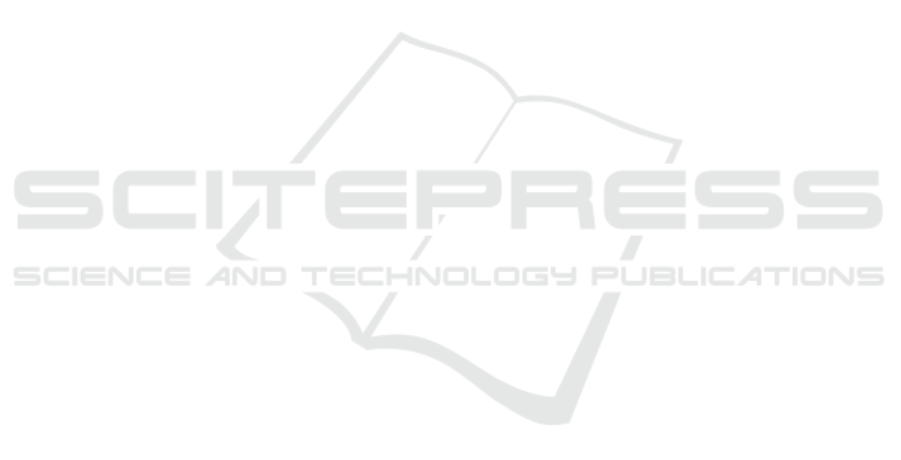
model by using a SimMechanics and VRML environ-
ment (Bouzgou et al., 2014) (Bouzgou et al., 2015).
REFERENCES
Aydemir, M., Arıkan, K. B., and
˙
Irfano
˘
glu, B. (2015). Dis-
turbance rejection control of a quadrotor equipped
with a 2 dof manipulator. In Machine Vision and
Mechatronics in Practice, pages 91–103. Springer.
Bouzgou, K. and Ahmed-Foitih, Z. (2014). Geometric mod-
eling and singularity of 6 dof fanuc 200ic robot. In
Innovative Computing Technology (INTECH), 2014
Fourth International Conference on, pages 208–214.
IEEE.
Bouzgou, K. and Ahmed-Foitih, Z. (2015). Workspace
analysis and geometric modeling of 6 dof fanuc 200ic
robot. Procedia-Social and Behavioral Sciences,
182:703–709.
Bouzgou, K., Ahmed-Foitih, Z., and Oran-Algeria, U. M.
(2014). Singularity analysis and illustration of inverse
kinematic solutions of 6 dof fanuc 200ic robot in vir-
tual environment. Journal of Intelligent Computing,
5(3):91–105.
Bouzgou, K., Amar, R. H. E., and Ahmed-Foitih, Z. (2015).
Virtual reality simulation and singularity analysis of
3-rrr translational parallel robot. In Innovative Com-
puting Technology (INTECH), 2015 Fifth Interna-
tional Conference on, pages 61–66. IEEE.
Bouzgou, K., Benchikh, L., Nouveliere, L., Bestaoui, Y.,
and Ahmed-Foitih, Z. (2019a). A new classification
and aerial manipulation q-prr design.
Bouzgou, K., Benchikh, L., Nouveliere, L., Bestaoui, Y.,
and Ahmed-Foitih, Z. (2019b). A novel aerial manip-
ulation design, modelling and control for geometric
com compensation.
Cho, S. and Shim, D. H. (2017). Development of a vision-
enabled aerial manipulator using a parallel robot.
Transaction of the Japan Society for Aeronautical and
Space Sciences, 15(APISAT-2016):a27–a36.
Danko, T. W., Chaney, K. P., and Oh, P. Y. (2015). A parallel
manipulator for mobile manipulating uavs. In Tech-
nologies for Practical Robot Applications (TePRA),
2015 IEEE International Conference on, pages 1–6.
IEEE.
Danko, T. W. and Oh, P. Y. (2014). Design and control of
a hyper-redundant manipulator for mobile manipulat-
ing unmanned aerial vehicles. Journal of Intelligent &
Robotic Systems, 73(1-4):709.
Escareno, J., Flores, G., Rakotondrabe, M., Romero, H.,
Lozano, R., and Rubio, E. (2014). Task-based con-
trol of a multirotor miniature aerial vehicle having an
onboard manipulator. In Unmanned Aircraft Systems
(ICUAS), 2014 International Conference on, pages
857–863. IEEE.
Fumagalli, M., Naldi, R., Macchelli, A., Forte, F., Keemink,
A. Q., Stramigioli, S., Carloni, R., and Marconi,
L. (2014). Developing an aerial manipulator proto-
type: Physical interaction with the environment. IEEE
robotics & automation magazine, 21(3):41–50.
Huber, F., Kondak, K., Krieger, K., Sommer, D.,
Schwarzbach, M., Laiacker, M., Kossyk, I., Parusel,
S., Haddadin, S., and Albu-Sch
¨
affer, A. (2013). First
analysis and experiments in aerial manipulation us-
ing fully actuated redundant robot arm. In Intelligent
Robots and Systems (IROS), 2013 IEEE/RSJ Interna-
tional Conference on, pages 3452–3457. IEEE.
Jimenez-Cano, A., Heredia, G., and Ollero, A. (2017).
Aerial manipulator with a compliant arm for bridge
inspection. In Unmanned Aircraft Systems (ICUAS),
2017 International Conference on, pages 1217–1222.
IEEE.
Kamel, B., Yasmina, B., Laredj, B., Benaoumeur, I., and
Zoubir, A.-F. (2017). Dynamic modeling, simulation
and pid controller of unmanned aerial vehicle uav. In
Innovative Computing Technology(INTECH) Seventh
International Conference on, pages 64–69. IEEE.
Kim, S., Choi, S., and Kim, H. J. (2013). Aerial manipu-
lation using a quadrotor with a two dof robotic arm.
In Intelligent Robots and Systems (IROS)/RSJ Inter-
national Conference on, pages 4990–4995. IEEE.
Kondak, K., Krieger, K., Albu-Schaeffer, A., Schwarzbach,
M., Laiacker, M., Maza, I., Rodriguez-Castano, A.,
and Ollero, A. (2013). Closed-loop behavior of an
autonomous helicopter equipped with a robotic arm
for aerial manipulation tasks. International Journal of
Advanced Robotic Systems, 10(2):145.
Korpela, C., Orsag, M., Pekala, M., and Oh, P. (2013). Dy-
namic stability of a mobile manipulating unmanned
aerial vehicle. In germany 2013, I., editor, Robotics
and Automation International Conference on, pages
4922–4927. IEEE.
Lee, H., Kim, H., and Kim, H. J. (2015). Path planning and
control of multiple aerial manipulators for a cooper-
ative transportation. In 2015 IEEE/RSJ International
Conference on Intelligent Robots and Systems (IROS),
pages 2386–2391. IEEE.
Lippiello, V. and Ruggiero, F. (2012). Cartesian impedance
control of a uav with a robotic arm. IFAC Proceedings
Volumes, 45(22):704–709.
Mello, L. S., Aldorno, B., and Raffo, G. V. (2015). Whole-
body modeling and control of an unmanned aerial ma-
nipulator. In the XII Brazilian Symposium of Intelli-
gent Automation (XII SBAI). Natal.
Ruggiero, F., Trujillo, M. A., and all (2015). A multi-
layer control for multirotor uavs equipped with a servo
robot arm. In Robotics and Automation (ICRA),IEEE
International Conference on, pages 4014–4020.
Srikanth, M. B., Soto, A., Annaswamy, A., Lavretsky, E.,
and Slotine, J.-J. (2011). Controlled manipulation
with multiple quadrotors. In AIAA Conf. on Guidance,
Navigation and Control.
Yeol, J. W., Toohey, D., and Hwang, Y.-W. (2017). Design
and analysis of a multiple tentacle system for mobile
manipulation in micro aerial vehicles. Procedia Com-
puter Science, 105:7–13.
PD Sliding Mode Controller based Decoupled Aerial Manipulation
489