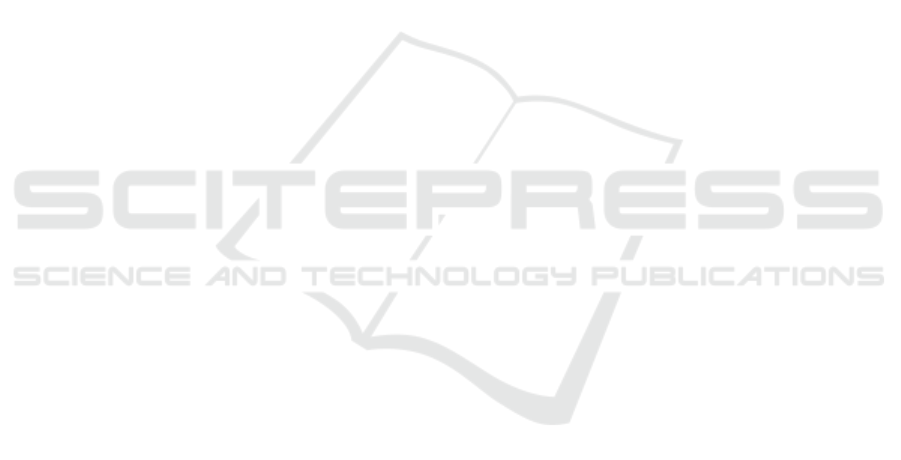
Bentaleb, T., Nguyen, V. T., Sentouh, C., Conreur, G.,
Poulain, T., and Pudlo, P. (2019). A real-time multi-
objective predictive control strategy for wheelchair er-
gometer platform. In 2019 IEEE International Con-
ference on Systems, Man and Cybernetics (SMC).
Berret, B., Darlot, C., Jean, F., Pozzo, T., Papaxanthis, C.,
and Gauthie, J. P. (2008). The inactivation principle:
Mathematical solutions minimizing the absolute work
and biological implications for the planning of arm
movements. Public Library of Science, 4(10).
Betts, J. T. (2010). Practical methods for optimal control
and estimation using nonlinear programming, vol-
ume 19. SIAM.
Cooper, R. A., , Corfman, T. A., Fitzgerald, S. G., Boninger,
M. L., Spaeth, D. M., Ammer, W., and Arva, J.
(2002). Performance assessment of a pushrim-
activated power-assisted wheelchair control system.
IEEE transactions on control systems technology,
10(1):121–126.
Cooper, R. A. (1990a). A force/energy optimization model
for wheelchair athletics. IEEE Transactions on Sys-
tems, Man, and Cybernetics, 20(2):444–449.
Cooper, R. A. (1990b). A systems approach to the modeling
of racing wheelchair propulsion. Journal of Rehabili-
tation Research and Development, 27(2):151–162.
Cuerva, V. I., Ackermann, M., and Leonardi, F. (2016). A
comparison of different assistance strategies in power
assisted wheelchairs using an optimal control formu-
lation. In Proceedings of the Sixth IASTED Interna-
tional Conference Modeling, Simulation and Identifi-
cation (MSI 2016).
Hintzy, F., Tordi, N., and Perrey, S. (2002). Muscular effi-
ciency during arm cranking and wheelchair exercise: a
comparison. International journal of sports medicine,
23(06):408–414.
Horiuchi, M., Muraki, S., Horiuchi, Y., Inada, N., and Abe,
D. (2014). Energy cost of pushing a wheelchair on
various gradients in young men. International Journal
of Industrial Ergonomics, 44(3):442–447.
Karmarkar, A., Cooper, R. A., Liu, H. Y., Connor, S.,
and Puhlman, J. (2008). Evaluation of pushrim-
activated power-assisted wheelchairs using ansi/resna
standards. Archives of physical medicine and rehabil-
itation, 89(6):1191–1198.
Luhtanen, P., Rahkila, P., Rusko, H., and Viitasalo, J. T.
(1987). Mechanical work and efficiency in ergometer
bicycling at aerobic and anaerobic thresholds. Acta
physiologica scandinavica, 131(3):331–337.
Oukacha, O. and Boizot, N. (2020). Consumption minimi-
sation for an academic vehicle. Accepted for publica-
tion in the Optimal control applications and methods
(October 2016 - march 2020), <hal-01384651>.
Pezzuti, E., Pvalentini, P., and Vita, L. (2006). Design and
optimization of a wheelchair for basketball using cad.
In XVIII Congresso INGEGRAF.
Pontryagin, L. S., Boltyanskii, V. G., Gamkrelidze, R. V.,
and Mishchenko, E. F. (1962). The Mathematical The-
ory of Optimal Processes. John Wiley and Sons, New
York-London-Sydney.
Rozendaal, L. A., Veeger, H. E. J., and van der Woude,
L. H. V. (2003). The push force pattern in manual
wheelchair propulsion as a balance between cost and
effect. Journal of Biomechanics, 36(2):239–247.
Williams, K. R. (1985). The relationship between mechani-
cal and physiological energy estimates. Medicine and
Science in Sports and Exercise, 17(3):317–325.
Yang, Y. S., Koontz, A., Triolo, R. J., Cooper, R. A., and
Boninger, M. L. (2009). Biomechanical analysis of
functional electrical stimulation on trunk musculature
during wheelchair propulsion. Neurorehabilitation
and Neural Repair, 23(7):717–725.
ICINCO 2020 - 17th International Conference on Informatics in Control, Automation and Robotics
166