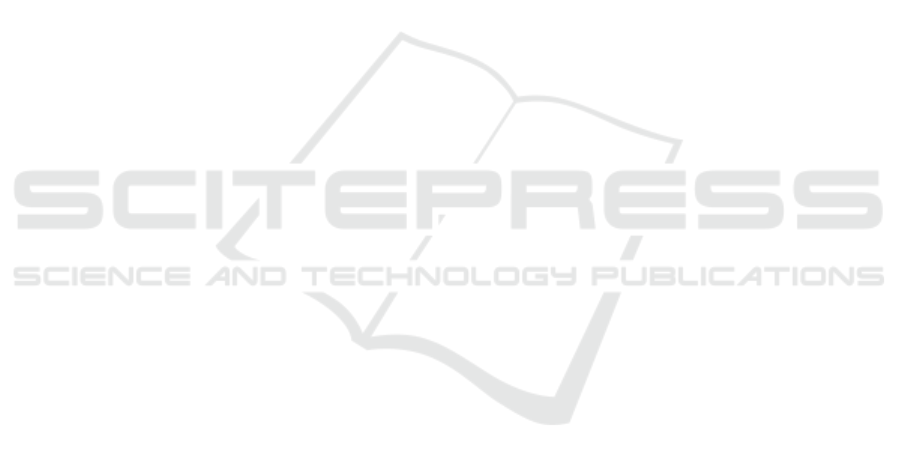
lightning of the experiment) when used with a noisy
or low-resolution camera. (4) The evolution of the
system should be also studied over a longer time-scale
since some experiments (like in Figure 12) suggest the
presence of cyclic behavior. (5) Future work should
also focus on the quantitative analysis of the process
in the context of the proposed model.
ACKNOWLEDGEMENTS
The research leading to these results has re-
ceived funding from the Czech Science Foundation
(GA
ˇ
CR) under grant agreement no. 19-26143X.
The work of Miroslav Kulich has been supported
by the European Regional Development Fund un-
der the project Robotics for Industry 4.0 (reg. no.
CZ.02.1.01/0.0/0.0/15 003/0000470).
REFERENCES
Boncheva, M., Bruzewicz, D., and Whitesides, G. (2003).
Millimeter-scale self-assembly and its applications.
Pure Appl. Chem, 75:621–630.
Boncheva, M. and Whitesides, G. (2005). Making things by
self-assembly. MRS Bulletin, 30:736–742.
Cademartiri, L. and Bishop, K. J. M. (2015). Programmable
self-assembly. Nature materials, 14 1:2–9.
Chen, J. and Seeman, N. C. (1991). Synthesis from DNA
of a molecule with the connectivity of a cube. Nature,
350:631–633.
Cheung, K. C., Demaine, E. D., Bachrach, J. R., and Grif-
fith, S. (2011). Programmable assembly with univer-
sally foldable strings (moteins). IEEE Transactions on
Robotics, 27(4):718–729.
Daiko Tsutsumi and Satoshi Murata (2007). Multistate part
for mesoscale self-assembly. In SICE Annual Confer-
ence 2007, pages 890–895.
Douglas, S. M., Dietz, H., Liedl, T., Hogberg, B., Graf, F.,
and Shih, W. M. (2009). Self-assembly of DNA into
nanoscale three-dimensional shapes. In Nature.
Egri, S. and Bihari, G. (2018). Self-assembly of magnetic
spheres: a new experimental method and related the-
ory. Journal of Physics Communications, 2.
Haghighat, B., Droz, E., and Martinoli, A. (2015). Lily: A
miniature floating robotic platform for programmable
stochastic self-assembly. In 2015 IEEE International
Conference on Robotics and Automation (ICRA),
pages 1941–1948.
Hosokawa, K., Shimoyama, I., and Miura, H. (1996).
Two-dimensional micro-self-assembly using the sur-
face tension of water. Sensors and Actuators A: Phys-
ical, 57(2):117 – 125. Ninth International Workshop
on Micro Electro Mechanical System.
Jiang, S., Hong, F., Hu, H., Yan, H., and Liu, Y. (2017).
Understanding the elementary steps in DNA tile-based
self-assembly. ACS Nano, 11(9):9370–9381. PMID:
28813590.
Krogius, M., Haggenmiller, A., and Olson, E. (2019). Flex-
ible layouts for fiducial tags. In 2019 IEEE/RSJ In-
ternational Conference on Intelligent Robots and Sys-
tems (IROS), pages 1898–1903.
L
¨
othman, P. A. (2018). Macroscopic magnetic self-
assembly. PhD thesis, University of Twente, Nether-
lands.
Masumori, A. and Tanaka, H. (2013). Morphological com-
putation on two dimensional self-assembly system.
In ACM SIGGRAPH 2013 Posters, SIGGRAPH ’13,
New York, NY, USA. Association for Computing Ma-
chinery.
McGorty, R., Fung, J., Kaz, D., and Manoharan, V. N.
(2010). Colloidal self-assembly at an interface. Mate-
rials Today, 13(6):34 – 42.
Ne
ˇ
zerka, V., Somr, M., Janda, T., Vorel, J., Do
ˇ
sk
´
a
ˇ
r, M.,
Anto
ˇ
s, J., Zeman, J., and Nov
´
ak, J. (2018). A jigsaw
puzzle metamaterial concept. Composite Structures,
202:1275–1279.
Patitz, M. J. (2014). An introduction to tile-based self-
assembly and a survey of recent results. Natural Com-
puting, 13(2):195–224.
Rothemund, P. W. K. (2000). Using lateral capillary forces
to compute by self-assembly. Proceedings of the Na-
tional Academy of Sciences, 97(3):984–989.
Rothemund, P. W. K. (2006). Folding DNA to create
nanoscale shapes and patterns. Nature, 440:297–302.
Rothemund, P. W. K., Papadakis, N., and Winfree, E.
(2004). Algorithmic self-assembly of DNA Sierpin-
ski triangles. PLoS Biology, 2:1021 – 1024.
van Dommelen, R., Fanzio, P., and Sasso, L. (2018). Sur-
face self-assembly of colloidal crystals for micro- and
nano-patterning. Advances in Colloid and Interface
Science, 251:97 – 114.
Wei, S., Qin, M., and Zhang, J. (2016). Mechanism
and application of capillary-force self-assembly mi-
cro/nanofabrication. In 2016 IEEE International Con-
ference on Manipulation, Manufacturing and Mea-
surement on the Nanoscale (3M-NANO), pages 256–
260.
Whitesides, G. M. and Grzybowski, B. A. (2002). Self-
assembly at all scales. Science, 295:2418–2421. 793.
Winfree, E. (1998). Algorithmic self-assembly of DNA. PhD
thesis, Caltech.
Winfree, E. (2006). Algorithmic self-assembly of DNA. In
2006 International Conference on Microtechnologies
in Medicine and Biology, page 4.
Centimeter-scaled Self-Assembly: A Preliminary Study
445