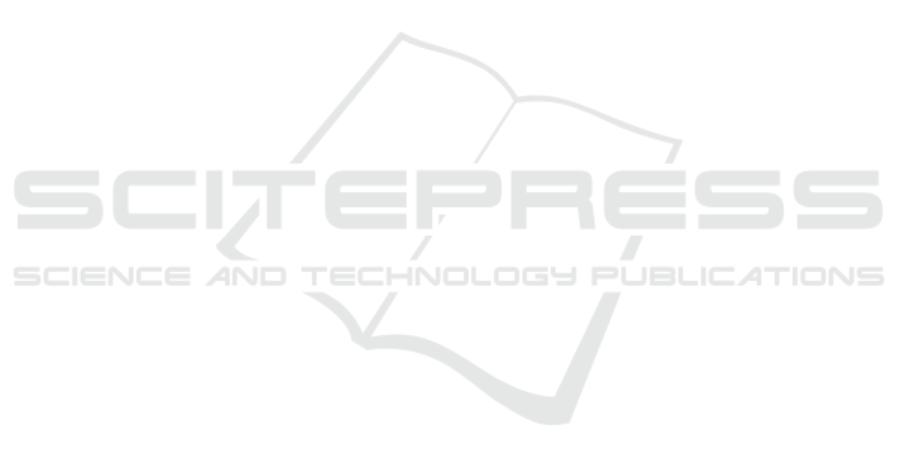
lash coupling. The IMU measurement can be initiated
manually independent of the hardware that controls
the motor, because time synchronisation is possible
based on the recorded signals.
ACKNOWLEDGEMENTS
This work was sponsored by the AiF (Arbeits-
gemeinschaft industrieller Forschungsvereinigungen
Otto von Guericke e.V.) and managed by the FVA
(Forschungsvereinigung Antriebstechnik e.V.) both in
Germany.
REFERENCES
Amazon Web Services, Inc. (2020). FreeRTOS
TM
- real-time operating system for microcontrollers.
https://www.freertos.org/index.html, accesssed: Feb.
2020.
Calvini, M., Carpita, M., Formentini, A., and Marchesoni,
M. (2015). Pso-based self-commissioning of electrical
motor drives. IEEE Transactions on Industrial Elec-
tronics, 62(2):768–776.
Dagalakis, N. G. and Myers, D. R. (1985). Adjustment
of robot joint gear backlash using the robot joint test
excitation technique. The international journal of
robotics research, 4(2):65–79.
Friedland, B. (1997). Feedback control of systems with par-
asitic effects. In Proceedings of the 1997 American
Control Conference (Cat. No. 97CH36041), volume 2,
pages 937–941. IEEE.
Gebler, D. and Holtz, J. (1998). Identification and compen-
sation of gear backlash without output position sensor
in high-precision servo systems. In IECON’98. Pro-
ceedings of the 24th Annual Conference of the IEEE
Industrial Electronics Society (Cat. No. 98CH36200),
volume 2, pages 662–666. IEEE.
Han, Y., Liu, C., and Wu, J. (2016). Backlash identifica-
tion for PMSM servo system based on relay feedback.
Nonlinear Dynamics, 84(4):2363–2375.
Itoh, M. (2008). Torsional vibration suppression of a twin-
drive geared system using model-based control. In
2008 10th IEEE International Workshop on Advanced
Motion Control, pages 176–181. IEEE.
Lagerberg, A. (2001). A literature survey on control of au-
tomotive powertrains with backlash. Technical Re-
port R013/2001, Control and Automation Laboratory,
Chalmers University of Technology, G
¨
oteborg, Swe-
den.
Lagerberg, A. and Egardt, B. (2005). Model predictive con-
trol of automotive powertrains with backlash. IFAC
Proceedings Volumes, 38(1):1–6.
Lenze (2020). Product-related documentation. https://
www.lenze.com/en-de/services/knowledge-base/
product-related-documentation/, accesssed: Feb.
2020.
Marton, L. and Lantos, B. (2009). Friction and backlash
measurement and identification method for robotic
arms. In 2009 International Conference on Advanced
Robotics, pages 1–6. IEEE.
Merzouki, R., Davila, J. A., Cadiou, J. C., and Fridman, L.
(2006). Backlash phenomenon observation and identi-
fication. In 2006 American Control Conference, pages
3322–3327. IEEE.
Nordin, M. and Gutman, P.-O. (2000). Nonlinear speed con-
trol of elastic systems with backlash. In Proceedings
of the 39th IEEE Conference on Decision and Control
(Cat. No. 00CH37187), volume 4, pages 4060–4065.
IEEE.
Nordin, M. and Gutman, P.-O. (2002). Controlling mechan-
ical systems with backlash – a survey. Automatica,
38(10):1633–1649.
Popp, E., Tantau, M., Wielitzka, M., Ortmaier, T., and
Giebert, D. (2019). Frequency domain identification
and identifiability analysis of a nonlinear vehicle driv-
etrain model. In 2019 18th European Control Confer-
ence (ECC), pages 237–242. IEEE.
Ravanbod-Shirazi, L. and Besanc¸on-Voda, A. (2002).
Backlash identification: a two step approach. IFAC
Proceedings Volumes, 35(1):85–90.
Reddy, P., Darokar, K., Robinette, D., Shahbakhti, M.,
Blough, J., Ravichandran, M., Farmer, M., and Doer-
ing, J. (2019). Control-oriented modeling of a vehicle
drivetrain for shuffle and clunk mitigation. Technical
report, SAE Technical Paper.
Rostalski, P., Besselmann, T., Bari
´
c, M., Belzen, F. V.,
and Morari, M. (2007). A hybrid approach to mod-
elling, control and state estimation of mechanical sys-
tems with backlash. International Journal of Control,
80(11):1729–1740.
S
¨
arkk
¨
a, S. (2013). Bayesian filtering and smoothing, vol-
ume 3. Cambridge University Press.
Schoeling, I. and Orlik, B. (2000). Control of a nonlinear
two-mass system with uncertain parameters and un-
known states. In IEEE Industry Applications Confer-
ence (Cat. No. 00CH37129), volume 2, pages 1096–
1103. IEEE.
Shim, H., Kochem, M., and Tomizuka, M. (1998). Use of
accelerometer for precision motion control of linear
motor driven positioning system. In IECON’98. Pro-
ceedings of the 24th Annual Conference of the IEEE
Industrial Electronics Society (Cat. No. 98CH36200),
volume 4, pages 2409–2414. IEEE.
Specht, R. (1986). Ermittlung von Getriebelose und
Getriebereibung bei Robotergelenken mit Gleich-
stromantrieben. VDI-Berichte, (598):71–83.
Tao, G. and Kokotovic, P. V. (1996). Adaptive control of
systems with actuator and sensor nonlinearities. John
Wiley & Sons, Inc.
Villwock, S. (2007). Identifikationsmethoden f
¨
ur
die automatisierte Inbetriebnahme und Zu-
stands
¨
uberwachung elektrischer Antriebe. PhD
thesis, Universit
¨
at Siegen.
Villwock, S. and Pacas, M. (2009). Time-domain iden-
tification method for detecting mechanical backlash
Backlash Identification in Industrial Positioning Systems Aided by a Mobile Accelerometer Board with Wi-Fi
583