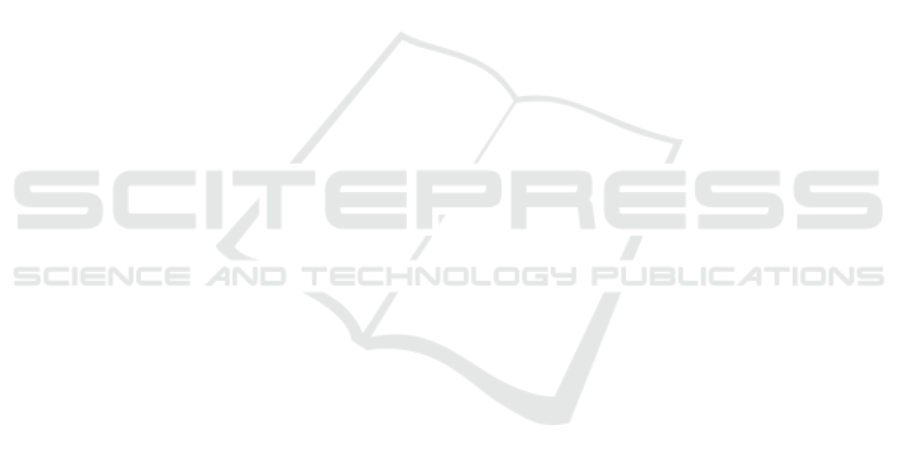
The main difference comes when the systems
come under stress: On-line systems could take ad-
vantages from updates if they are prepared and sent in
time by trackside (or the TMS behind). Off-line sys-
tems have only pre-loaded data. It is therefore mean-
ingful to load them with full maps and equip the track
so that they could quickly recognize where the route
leads (to which speed profile and potential stops).
On-line ATO can result in more efficient ride of
the trains (as they have more up-to-date and more pre-
cise data) – but only where the data are available and
in time. Off-line ATO is cheaper and can be used even
when the surrounding traffic data is not available.
8 EXPERIENCE FROM AVV
8.1 A few Gossips from AVV History
Automated Train Operation/Control (In Czech: Auto-
matick
´
e veden
´
ı vlaku (AVV); (Myslivec et al., 1998;
Lieskovsky and Myslivec, 2011)) is a system in-
stalled on hundreds of vehicles and used in practice
for many years (in commercial operation since 1991,
tests since half of 1960’s). Its basics have been de-
veloped decades ago. It has been therefore limited to
preloaded data available on board (at those times no
GSM-R or related technology has been available).
The dependency on preloaded on-board data led to
the graph-like track description. The graph contains
all tracks equipped with AVV-compatible balises. The
system can be therefore used everywhere where there
are necessary data available and where it is possible
to position precisely the train. The system is there-
fore robust to any change of the train path within this
graph. It the train is sent to some part of the track
where no information is available, it switches to con-
trol by the driver. The system always takes into ac-
count all (known) possible paths.
8.2 Cooperation of AVV with ATP
The AVV system reads the signals from national Class
B ATP system (compare (Lieskovsk
´
y et al., 2006))
and is capable to utilise data from onboard ETCS
if available (see (Lieskovsky and Myslivec, 2011)).
Even if no ATP is available, AVV can work alone and
can prevent some critical situations (can slow down
or stop the train if necessary).
8.3 AVV Approach to Data
The system is able to work without connectivity to
TMS On the other hand, it is limited to the areas for
whose it is equipped with corresponding maps. The
system is designed so that if a driver has some useful
information (s)he can enter the data relatively easily.
9 COMMON REQUIREMENTS
It is likely, and the available documents prove, that all
ATO systems need some basic information. It covers
information about speed limit start and end positions,
their validity for beginning or end of the train; plat-
forms and their positions; stopping points (their po-
sitions and required train alignment there); and train
timetable. There should be also information identify-
ing stations (to provide information about them to the
passengers), optionality of the stop (to induce its po-
tential request). Additionally, there should be avail-
able also some safety requirements (not to stop on
some places where it is not possible to rescue people
from the train).
If possible, it can be advantageous if there is in-
formation about current conditions around the train
like signals or information about other trains (e.g. if
there is a slow train ahead of given train, it could be
reasonable to slow down a bit); sometimes it could be
advantageous to speed up to allow smooth train cross-
ing on a more appropriate place.
The data could be stored efficiently. The detailed
track description covering haul between Praha and
Kol
´
ın (62 km distance, multiple stations, about 320
km of single track, single direction line) have been
stored in a 3KB piece of EPROM.
10 DIVERGING REQUIREMENTS
Various ATO systems could require different addi-
tional information. It can cover position and radius
of curves, some could require also their direction (in
other cases only modified train resistance could be
enough). Similarly, some systems can take advantage
from information about tunnels and bridges and their
parameters.
As it seems to be advantageous to have this in-
formation as in these places, the train running resis-
tance really is higher than the one in straight track in
open country, the fact is that the running resistance
provided by vehicle manufacturer is usually higher
than reality (not to be a problem to verify it during
the tests) and after adding this additional component,
the expected running resistance goes more away from
reality... Finally, there exists a component that is not
possible to take into computations: wind. Its asset
VEHITS 2020 - 6th International Conference on Vehicle Technology and Intelligent Transport Systems
264