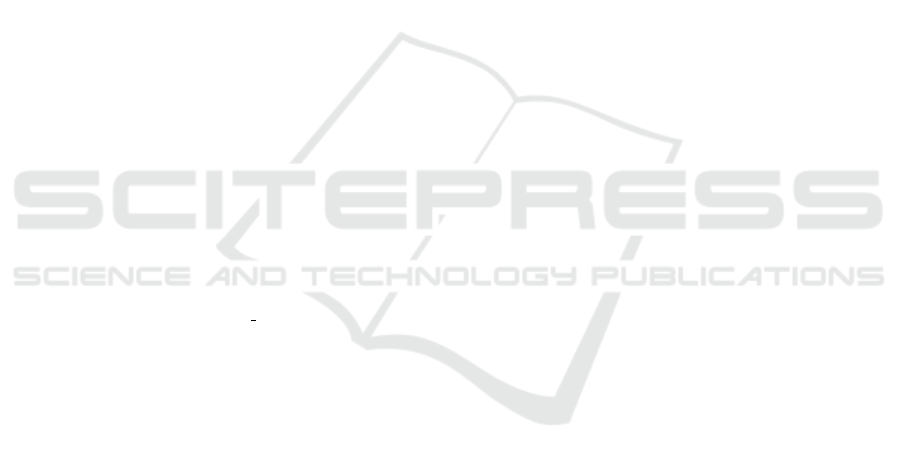
trial robots enabling them to cope with low-moderate
levels of disorders commonly found in maintenance
sectors. More importantly these techniques are lim-
ited to maintenance environments but certainly can be
adapted to manufacturing industry as well.
REFERENCES
Armada, M. A., Tavakoli, M., Zakerzadeh, M., Vossoughi,
G., and Bagheri, S. (2005). A hybrid pole climbing
and manipulating robot with minimum dofs for con-
struction and service applications. Industrial Robot:
An International Journal, 32(2):171–178.
BARA (2012). Robot facts 2012. Technical report, British
automation and Robotic Association.
Chan, B., Guan, H., Jo, J., and Blumenstein, M. (2015). To-
wards uav-based bridge inspection systems: A review
and an application perspective. Structural Monitoring
and Maintenance, 2(3):283–300.
Farnsworth, M. and Tomiyama, T. (2014). Capturing, clas-
sification and concept generation for automated main-
tenance tasks. CIRP Annals-Manufacturing Technol-
ogy, 63(1):149–152.
Fraser, K. (2014). Facilities management: the strategic se-
lection of a maintenance system. Journal of Facilities
Management, 12(1):18–37.
Gupta, A. and Arora, S. (2009). Industrial automation and
robotics. Laxmi Publications.
HSE (1999). Hazards during maintenance. http://
www.hse.gov.uk/safemaintenance/. (Accessed on
05/28/2017).
IFR (2015). World robotics 2014. https://ifr.org/img/
uploads/Executive-Summary
WR-Industrial-Robots-
0161.pdf. (Accessed on 05/28/2017).
Kochan, A. (2001). Tele-operated maintenance of live
power lines. Industrial Robot: An International Jour-
nal, 28(4):316–319.
Lasky, T. A. and Ravani, B. (2000). Sensor-based path plan-
ning and motion control for a robotic system for road-
way crack sealing. IEEE Transactions on Control Sys-
tems Technology, 8(4):609–622.
Lee, W., Hirai, M., and Hirose, S. (2013). Gunryu iii: recon-
figurable magnetic wall-climbing robot for decom-
missioning of nuclear reactor. Advanced Robotics,
27(14):1099–1111.
M
´
arquez, A. C. (2007). The maintenance management
framework: models and methods for complex systems
maintenance. Springer Science & Business Media.
Maruyama, Y. (2000). Robotic applications for hot-line
maintenance. Industrial Robot: An International
Journal, 27(5):357–365.
McNulty, R. (2011). Report of the rail value for money
study. Technical report, Department for Transport and
the Office of Rail Regulation.
Moura, J. and Erden, M. S. (2017). Formulation of a control
and path planning approach for a cab front cleaning
robot. Procedia CIRP, 59:67–71.
Nagatani, K., Kiribayashi, S., Okada, Y., Otake, K.,
Yoshida, K., Tadokoro, S., Nishimura, T., Yoshida,
T., Koyanagi, E., Fukushima, M., et al. (2013).
Emergency response to the nuclear accident at the
fukushima daiichi nuclear power plants using mobile
rescue robots. Journal of Field Robotics, 30(1):44–63.
Onori, M. and Kochan, A. (2005). Robot cleans glass roof
of louvre pyramid. Industrial Robot: An International
Journal, 32(5):380–382.
ORR (2014). Rail value for money study — office of
rail and road. http://www.orr.gov.uk/rail/publications/
reports/rail-value-for-money-study. (Accessed on
05/28/2017).
Parker, L. E. and Draper, J. V. (1998). Robotics applica-
tions in maintenance and repair. Handbook of indus-
trial robotics, pages 1023–1036.
Pegman, G., Luk, B., Liu, K., Collie, A., Cooke, D., and
Chen, S. (2006). Tele-operated climbing and mobile
service robots for remote inspection and maintenance
in nuclear industry. Industrial Robot: An Interna-
tional Journal, 33(3):194–204.
RAS (2014). Robotics and autonomous systems - ras 2020.
Technical report, The Knowledge Transfer Network.
RRUKA (2015). Robotics and autonomous systems
for rolling stock maintenance dissemination event
— rail research uk association (rruka). http://
www.rruka.org.uk/events/robotics-2/. (Accessed on
05/28/2017).
Tokhi, O., Zhang, H., Zhang, J., Wang, W., Liu, R., and
Zong, G. (2007). A series of pneumatic glass-wall
cleaning robots for high-rise buildings. Industrial
Robot: An International Journal, 34(2):150–160.
Tomiyama, T., Garc
´
ıa, L. R., Kr
ˇ
slin, A., and Taykaldira-
nian, G. (2017). Systems and conceptual design of a
train cab front cleaning robot. Procedia CIRP, 59:61–
66.
TSGL (2012). Rail technical strategy 2012. https://
www.rssb.co.uk/library/future%20railway/innovation-
in- rail- rail- technical- strategy-2012.pdf. (Accessed
on 05/28/2017).
UKTI (2014). The uk rail industry: A showcase of excel-
lence. Technical report, UK Trade & Investment.
Villedieu, E. and Francois, D. (1995). Vehicle for the auto-
matic laying of a track by a vehicle travelling on said
track and track designed for installation by such a ve-
hicle. US Patent 5,385,102.
A Study on Automating Rolling-stock Maintenance in the Rail Industry using Robotics
283