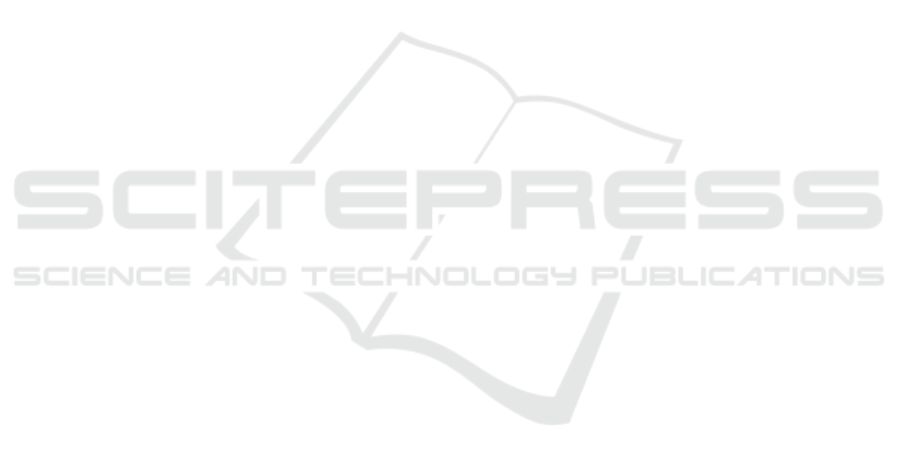
REFERENCES
Bagheri, M., Ajoudani, A., Lee, J., Caldwell, D. G.,
and Tsagarakis, N. G. (2015). Kinematic Analysis
and Design Considerations for Optimal Base Frame
Arrangement of Humanoid Shoulders. In IEEE Int.
Conf. Robot. Autom., pages 2710–2715, Seattle.
Belter, D., Skrzypczy
´
nski, P., Walas, K., and Wlodkowic,
D. (2015). Affordable Multi-legged Robots for
Research and STEM Education: A Case Study of
Design and Technological Aspects. In Prog. Autom.
Robot. Meas. Tech., pages 23–34. Springer.
Caldwell, D. G., Tsagarakis, N., and Semini, C.
(2014). Mechanism and Structures: Humanoids
and Quadrupeds. In Bioinspired Approaches for
Human-Centric Technologies, pages 133–153.
Chen, J. J., Peattie, A. M., Autumn, K., and Full, R. J.
(2006). Differential leg function in a sprawled-posture
quadrupedal trotter. J. Exp. Biol., 209(2):249–259.
Chen, X., Sun, Y., Huang, Q., Jia, W., and Pu, H.
(2008). Development of Multi-Legged Walking
Robot Using Reconfigurable Modular Design and
Biomimetic Control Architecture. J. Syst. Des. Dyn.,
2(1):401–412.
Chiacchio, P., BouffardVercelli, Y., and Pierrot, F. (1997).
Force polytope and force ellipsoid for redundant
manipulators. J. Robot. Syst., 14(8):613–620.
Corke, P. (2011). Robotics, Vision and Control:
Fundamental Algorithms in MATLAB. Springer
Science & Business Media.
Gasparetto, A., Vidoni, R., and Seidl, T. (2008).
Kinematic study of the spider system in a biomimetic
perspective. In IEEE/RSJ Int. Conf. Intell. Robot.
Syst., pages 3077–3082. IEEE.
Ho, T., Choi, S., and Lee, S. (2007). Development
of a biomimetic quadruped robot. J. Bionic Eng.,
4(4):193–199.
Hutter, M., Gehring, C., Bloesch, M., Hoepflinger, M. A.,
Remy, C. D., and Siegwart, R. (2012). StarlETH: A
compliant quadrupedal robot for fast, efficient, and
versatile locomotion. In 15th Int. Conf. Climbing
Walk. Robot. 2012, number EPFL-CONF-181042.
Kang, T., Kim, H., Son, T., and Choi, H. (2003).
Design of quadruped walking and climbing robot. In
IEEE/RSJ Int. Conf. Intell. Robot. Syst., volume 1,
pages 619–624. IEEE.
Kar, D. C. (2003). Design of statically stable walking robot:
a review. J. Robot. Syst., 20(11):671–686.
Kashiri, N., Tsagarakis, N. G., Van Damme, M.,
Vanderborght, B., and Caldwell, D. G. (2014).
Enhanced Physical Interaction Performance for
Compliant Joint Manipulators using Proxy-based
Sliding Mode Control. In Int. Conf. Informatics
Control. Autom. Robot., pages 175–183, Vienna.
Kato, K. and Hirose, S. (2001). Development of
the quadruped walking robot, TITAN-IXmechanical
design concept and application for the humanitarian
de-mining robot. Adv. Robot., 15(2):191–204.
Laffranchi, M., Chen, L., Kashiri, N., Lee, J., Tsagarakis,
N. G., and Caldwell, D. G. (2014). Development and
control of a series elastic actuator equipped with a
semi active friction damper for human friendly robots.
Rob. Auton. Syst., 62(12):1827–1836.
Negrello, F., Garabini, M., Catalano, M. G., Kryczka, P.,
Choi, W., Caldwell, D. G., Bicchi, A., and Tsagarakis,
N. G. (2016). WALK-MAN Humanoid Lower
body Design Optimization for Enhanced Physical
Performance. In IEEE Int. Conf. Robot. Autom.,
Stockholm.
Pratt, J. E. and Tedrake, R. (2006). Velocity-based stability
margins for fast bipedal walking. In Fast Motions
Biomech. Robot., pages 299–324. Springer.
Raibert, M., Blankespoor, K., Nelson, G., Playter, R.,
and Team, T. B. (2008). Bigdog, the rough-terrain
quadruped robot. In Proc. 17th World Congr.,
volume 17, pages 10822–10825.
Roennau, A., Heppner, G., Pfozter, L., and Dillman, R.
(2013). Lauron V: Optimized leg configuration for the
design of a bio-inspired walking robot. In Proc. 16th
Int. Conf. Climbing Walk. Robot. Support Technol.
Mob. Mach., volume 1417.
Semini, C., Tsagarakis, N. G., Guglielmino, E., Focchi, M.,
Cannella, F., and Caldwell, D. G. (2011). Design
of HyQa hydraulically and electrically actuated
quadruped robot. Proc. Inst. Mech. Eng. Part I J. Syst.
Control Eng., page 0959651811402275.
Seok, S., Wang, A., Chuah, M. Y., Otten, D., Lang, J.,
and Kim, S. (2013). Design principles for highly
efficient quadrupeds and implementation on the MIT
Cheetah robot. In IEEE Int. Conf. Robot. Autom.,
pages 3307–3312. IEEE.
Shkolnik, A., Levashov, M., Manchester, I. R., and
Tedrake, R. (2010). Bounding on rough terrain
with the LittleDog robot. Int. J. Rob. Res., page
0278364910388315.
Siciliano, B., Sciavicco, L., Villani, L., and Oriolo, G.
(2009). Robotics: Modelling, Planning and Control.
Springer Science & Business Media.
Spr
¨
owitz, A., Tuleu, A., Vespignani, M., Ajallooeian, M.,
Badri, E., and Ijspeert, A. J. (2013). Towards dynamic
trot gait locomotion: Design, control, and experiments
with Cheetah-cub, a compliant quadruped robot. Int.
J. Rob. Res., 32(8):932–950.
Spyrakos-Papastavridis, E., Kashiri, N., Lee, J., Tsagarakis,
N. G., and Caldwell, D. G. (2015). Online impedance
parameter tuning for compliant biped balancing. In
IEEE-RAS International Conference on Humanoid
Robots, pages 210–216.
Xie, H., Zhang, Z., Shang, J., and Luo, Z. (2014).
Mechanical Design of A Modular Quadruped
Robot-XDog. In Int. Conf. Mechatronics, Electron.
Ind. Control Eng., pages 1074–1078.
Yoshikawa, T. (1985). Dynamic manipulability of robot
manipulators. In IEEE Int. Conf. Robot. Autom.,
volume 2, pages 1033–1038. IEEE.
Zielinska, T. (2013). Design Issues and Robots Autonomy.
In New Trends Mech. Mach. Sci., pages 691–699.
Zielinska, T. and Heng, J. (2003). Mechanical design
of multifunctional quadruped. Mech. Mach. Theory,
38(5):463–478.
ICINCO 2016 - 13th International Conference on Informatics in Control, Automation and Robotics
212