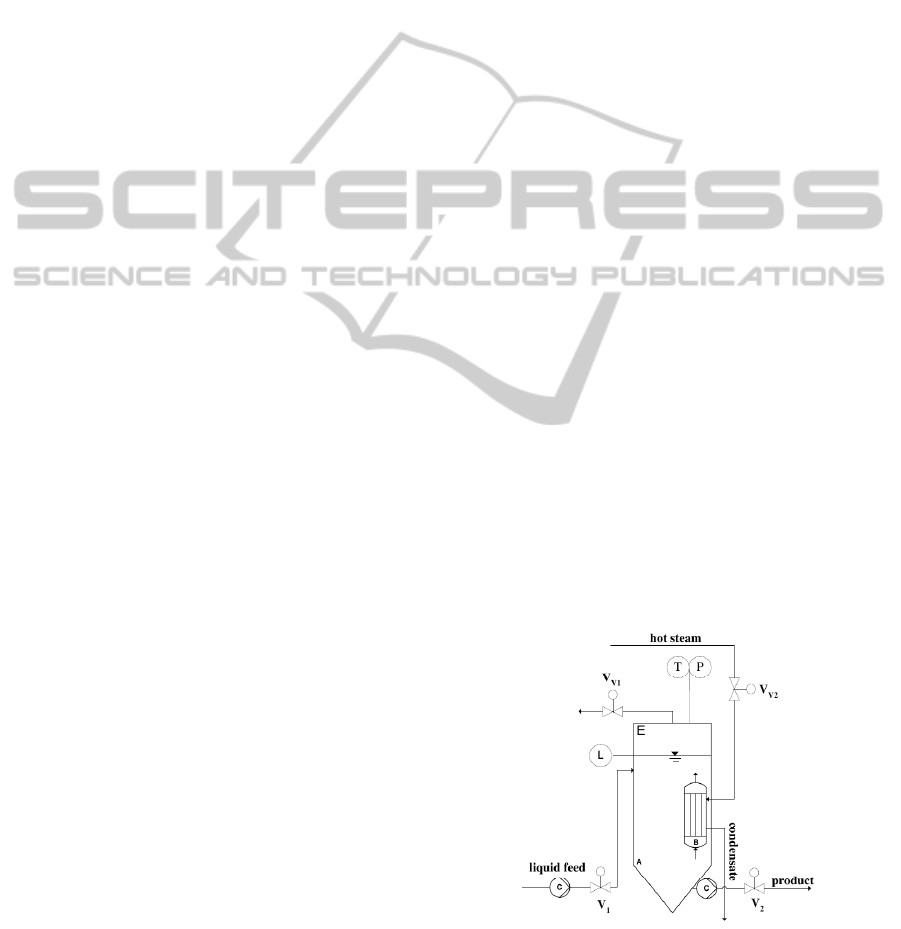
method to two fundamental tasks of process engineer-
ing, namely parameter estimation and the calculation
of sensitivities. Section 6 summarizes the results and
concludes the paper.
2 OPTIMIZATION OF HYBRID
SYSTEMS
Mathematically, discrete transitions in hybrid sys-
tems are often formulated in terms of complementar-
ity conditions. In actual numerical simulation, dis-
crete transitions are almost always handled through
embedded logical statements. At the zero-crossing
points of some switching function, the initial condi-
tions are updated and the appropriate set of equations
is solved restarting at this point in time (Barton and
Lee, 2002). Systems with so-called Filippov solu-
tions that remain for a while at the zero-crossing re-
quire additional analysis. Since they do not pose a
particular problem for our approach, we will not dis-
cuss them further here. A profound analysis and nu-
merical simulation results of hybrid systems can be
found in (Mehrmann and Wunderlich, 2009; Goebel
et al., 2009). For optimization tasks, the hybrid sim-
ulation can be embedded into a heuristic search al-
gorithm. For instance, particle swarm optimization
has been applied by (Pappala and Erlich, 2008) to
the unit commitment problem. These methods suf-
fer from high computational cost when many func-
tion evaluations are needed (i.e. in a high dimen-
sional search space). Alternatively one can consider
the problem as a constrained optimization problem
subject to the dynamic model equations. This leads
to a dynamic nonlinear program (NLP). In the so-
called direct method, the DAE system is discretized
resulting in a large-scale NLP with equality (and pos-
sibly inequality) constraints, which can be solved by
means of a NLP solver with a gradient-based search.
However this NLP-based optimization of hybrid sys-
tems is an extremely challenging task due to the non-
smoothness of the objective function or constraints
which result from instantaneous mode transitions. As
a consequence, NLP regularity cannot be presumed
and NLP solvers may fail. Essentially three different
approaches can be used to overcome this difficulty.
Mixed-integer methods have been applied success-
fully to optimal control problems by (Sonntag et al.,
2006) and (Barton et al., 2006), where a graph search
algorithm explores the state space of the discrete vari-
ables. An embedded NLP is used to find the local
optima in the continuous state space. The complex-
ity study in (Till et al., 2004) indicates that for sys-
tems with many decision variables solving the prob-
lem becomes computationally expensive. The sec-
ond approach applied, e.g., by (Prada et al., 2007)
and (Voelker et al., 2007) comprises sequential op-
timization methods. Here, the optimization layer ex-
clusively contains continuous variables. The hybrid
system is put into the simulation layer and solved
by any simulator which is capable to treat discon-
tinuities. Again, the necessity of many simulation
runs increases the computational cost. Reformulation
strategies, which represent the third class of methods,
introduce additional variables and parameters to re-
move the non-smoothness related to the complemen-
tarity conditions from the problem while retaining the
desired features. Reformulation strategies have been
studied by (Baumrucker et al., 2008; Sager, 2009;
Ralph and Wright, 2004). Most reformulation strate-
gies fall into one of the following two classes: (i)
Relaxation methods transform the complementarities
into a set of relaxed equality or inequality constraints,
e.g., by the smoothing discussed in this contribution.
A sequence of relaxed problems is solved in order to
approach the solution of the original problem. (ii) Pe-
nalization methods introduce a penalization term into
the objective function which measures the violation
of the complementarity condition.
3 MODEL OF THE EVAPORATOR
The evaporation of volatile components to concen-
trate non-volatile components within a mixture is a
common technology in process engineering. Usually
multi-stage systems built up from several identical
single evaporators are used. Such a single evaporator
model is considered in this paper following (Sonntag
et al., 2006). The system consists of an evaporation
Figure 1: Evaporator model (Sonntag et al., 2006).
tank and a heat exchanger (see Figure 1). The tank is
fed through the valveV
1
with a mixture of three liquid
SIMULTECH 2011 - 1st International Conference on Simulation and Modeling Methodologies, Technologies and
Applications
32