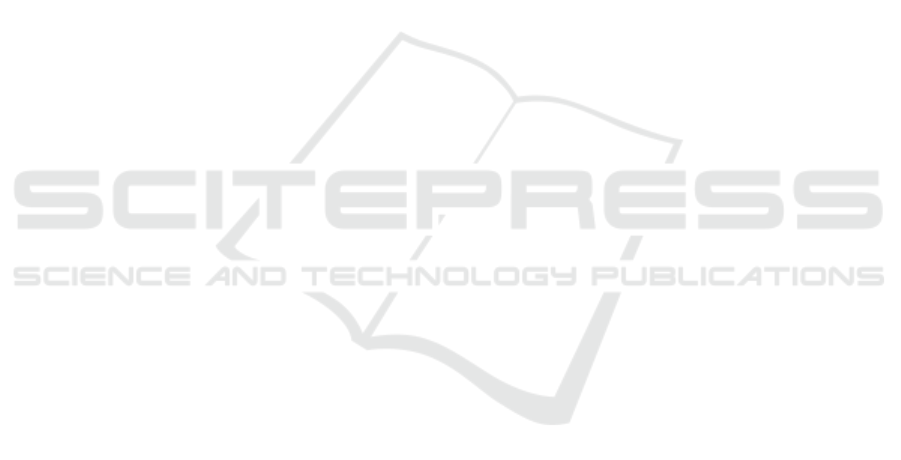
NUMERICAL PARAMETRIC STUDY OF COMPLEX LIQUID
FLOW IN THREE-DIMENSIONAL IMPELLER
AND IMPELLER-VOLUTE OF A CENTRIFUGAL PUMP
Massinissa Djerroud, Guyh Dituba Ngoma and Walid Ghie
University of Quebec in Abitibi-Témiscamingue, Department of Applied Sciences
445, Boulevard de l’Université, Rouyn-Noranda, Quebec, J9X 5E4, Canada
Keywords: Centrifugal Pump, Impeller, Volute, Navier-Stokes, Computational Fluid Dynamics, Modeling and
Simulation.
Abstract: In this study, the effects that the blade width, the blade number, and the impeller diameter have on the
steady state liquid flow in three-dimensional impeller, and combined impeller and volute were investigated.
The continuity and Navier-Stokes equations with the k-ε turbulence model and the standard wall functions
were used by mean of ANSYS-CFX code taking into account of the suction pressure variation as a function
of the valve volume flow rate. The achieved results reveal that the selected key design parameters have an
impact on the head, the brake horsepower and the overall efficiency of the centrifugal pump. To valid the
developed approach, the results of numerical simulation were compared with the experimental results
considering a special case of combined impeller and diffuser.
1 INTRODUCTION
Nowadays, centrifugal pumps are widely used in
industrial and mining enterprises. One of the most
important components of a centrifugal pump is the
impeller (Peng, W. W., 2008). The performance
characteristics related to the pump rely a great deal
on the impeller. To achieve better performance for a
centrifugal pump, design parameters such as the
number of blades, blade angles, the blade width, the
blade height, the impeller diameter and the volute
radius must be accurately determined, due to the
complex liquid flow through a centrifugal pump.
This liquid flow is three-dimensional and turbulent.
It is therefore important to be aware of the liquid
flow’s behavior when traveling through an impeller.
This can be done by accounting for the volute in the
planning, design, and optimization phases at
conditions of design and off-design. Many studies
have been carried out on the liquid flow through a
centrifugal pump (Zhou, W. et al., 2003;
Derakhshan, S., et al., 2008; Spence, R., et al., 2008;
Amaral-Teixeira, J., et al., 2008; Cheah, K.W.,
2007; Lee, T. S., et al., 2007; Wen-Guang, L., et al,
2002; LIU, H., et al., 2010; González, J., et al.,
2007; Asuaje, M., et al., 2005; Kaupert, K, et al.,
1999), where the effects of the number of impeller
blades on the pump’s performance were examined
experimentally by Wen-Guang, L., et al, 2002 and
Liu, H., et al., 2010. González, J., et al., 2007 had
numerically investigated the dynamic effects due to
the impeller-volute interaction within a centrifugal
pump, whereas the effects of the volute on velocity
and pressure fields were examined by Asuaje, M., et
al., 2005 and Kaupert, K, et al., 1999. The analysis
of previous works clearly demonstrated that research
results obtained are specific to the centrifugal pump
design parameter values and thus cannot be
generalized. In this work therefore a numerical study
was performed using a finite volume method
according to the CFX code (Ansys inc., 2008) to
gain further insight into the characteristics of the
three-dimensional turbulent liquid flow through an
impeller and a combined impeller and volute
accounting for suction pressure variation as a
function of the valve volume flow rate, while also
considering various flow conditions and pump
design parameters: blade width, blade number and
impeller outer diameters.
2 GOVERNING EQUATIONS
The models selected for the liquid flow in an
93
Djerroud M., Dituba Ngoma G. and Ghie W..
NUMERICAL PARAMETRIC STUDY OF COMPLEX LIQUID FLOW IN THREE-DIMENSIONAL IMPELLER AND IMPELLER-VOLUTE OF A
CENTRIFUGAL PUMP.
DOI: 10.5220/0003566800930102
In Proceedings of 1st International Conference on Simulation and Modeling Methodologies, Technologies and Applications (SIMULTECH-2011), pages
93-102
ISBN: 978-989-8425-78-2
Copyright
c
2011 SCITEPRESS (Science and Technology Publications, Lda.)