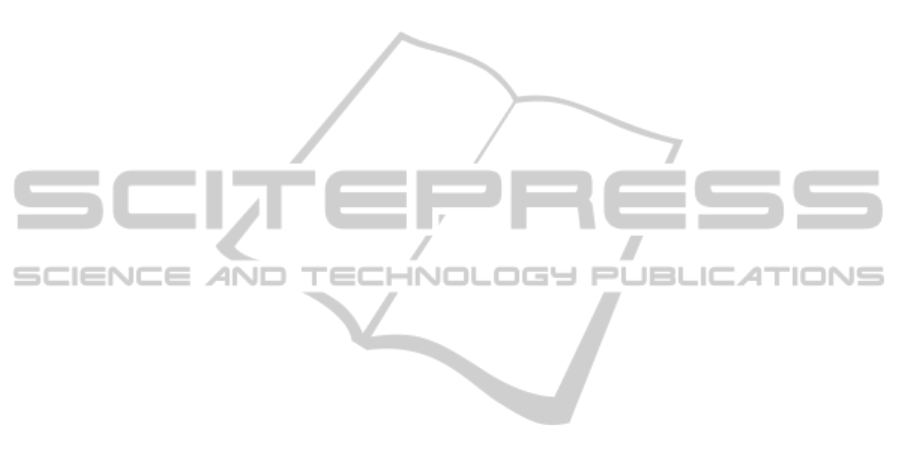
the kinematic invariants, including the CPC and
CenPC for the relatively movable link, for which we
already know the kinematic joint connecting it to the
input link as well as the Boll point. If we synthesize
a five-link mechanism, then the choice of the closed
kinematic pair can be subjected to the convenient
ratio of the two input velocities for the realization of
the transfer function of the third series.
Theoretically, the solutions are numerous, i.e.
numerous four-link CKC can be synthesized
(Genova 2010). Also, some special cases are studied
where the first transfer function is a constant, i.e. its
derivatives are zero, as well as solutions are
examined for a rectilinear section of maximum
length around the Boll point.
Further problems of the synthesis of hybrid
macro-micro mechatronic systems (MS):
- Synthesis of MS with three DoF and given
orientation of the trajectory of output link.
- Synthesis of MS with given points of
Burmester.
- Synthesis of MS combined with micro motions
by means of the methods of kinematic geometry of
infinitesimally close positions.
3 CONCLUSIONS
A design approach for the synthesis of five-link
mechanisms with two DoF with infinitesimally close
positions has been developed. With slight changes
this approach can also be implemented for the
synthesis of mechanisms with open kinematic
chains. The obtained results clearly demonstrate that
with the methods of kinematic geometry rectilinear
micro motions can be achieved with very high
precision and they can be successfully combined
with the motion of macro mechatronic systems
(MS). Such macro-micro MS are useful in the
performance of operations such as precise delivery
of probes in microelectronics and optics, pipetting,
cell injection and other microbiological operations.
Of course, the rectilinear trajectory may be obtained
by controlling the actuators, but inertial forces may
appear which will decrease the precision of the
trajectory.
With the two DoF mechanisms two principally
different problems can be formulated of the
synthesis with ICP: a direct problem and an inverse
problem. The direct problem is solved for a given
mechanism configuration and a given transfer ratio
of the velocities at the two inputs in order to find the
point of Boll. Furthermore, the results of these
examples show that optimal solutions can be sought
depending on the technological operation.
ACKNOWLEDGEMENTS
This work was funded by Bulgarian National
Science Fund through the project SpeSi-MINT Nr.
DO 0171/2008.
Dr. Kotev also acknowledges the support of the
ESF grant through the project BG051PO001-
3.3.0/40.
REFERENCES
Bacher, J., 2003. Conception de robots de tres haute
precision a articulations flexibles: integration
dynamicque-commande, these 2907, presenteee a ala
faculte sciences et techniques de l’ingenieur, institut
de production er robotique, section de
microtechnique, ecole polytechnique federale de
Lausanne, 1–150.
Codourey, A., W. Zesch, R. Buechi, R. Siegwart, 1994.
High Precision Robots for Automated Handling of
Micro Objects, Seminar on Handling and Assembly of
Microparts, Vienna, pp. 1–8, November 14th.
Chung, E. Pennestri, On a technique for higher order
synthesis of four-bar function generators, MMT, 1989.
Genova, P., R. Kitancheva, 1995. Curvature of Boll and
Boll’s point from a higher order, ММТ, №11.
Genova, K. Kostadinov, Vl. Kotev, 2009. Kinematic
invariants with infinitesimally close positions of
mechanisms with two degrees of freedom. Theoretical
and Applied mechanics, 2-5 Sept. 2009, Borovets,
Bulgaria.
Genova P., Kotev V., 2010. Structural Analysis of a Five-
Link Redundant Macro–Micro Mechatronic System,
ICBBM 2010, Liepaya, Latvia, May 24-28, 2010,
vol.7, 47-50.
Goldfarb, M. et al., 2002. An Introduction to Micro-and
Nanotechnology. Mechatronic Handbook.
Kobayashi, E., Masamune, K., 1999. A New Safe
Laparoscopic Manipulator System with a Five-Bar
Linkage Mechanism and an Optical Zoom, Computer
Aided Surgery, 4, pp.182-192.
Kotev V., Genova P., 2010. Computer Analysis for
Selection of Strategy of Control of Redundant Macro-
Micro Manipulation System. ICBBM 2010, Liepaya,
Latvia, May 24-28, 2010, vol.7, 51-54.
Tiankov, T. P. Genova, Vl. Kotev, K. Kostadinov, 2009.
Strategy for control of a hybrid macro – micro robot
with a 5 – link closed structure – an inverse problem
of kinematics. Proceedings of the international
conference on manufacturing systems – ICMaS, 2009,
Bucharest, Romania, 113 – 117.
ICINCO 2011 - 8th International Conference on Informatics in Control, Automation and Robotics
276