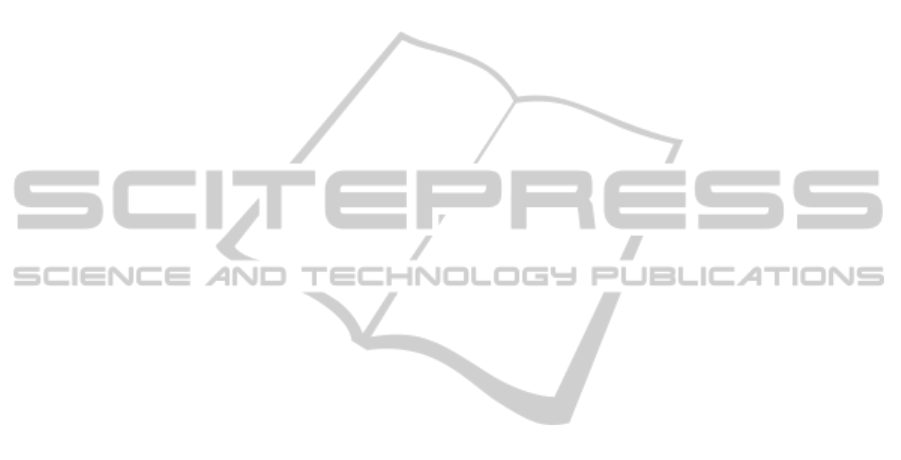
ding to Ashby and Johnson (2005), arranged in four
different selection methods called Selection by
Analysis, Selection by Synthesis, Selection by
Similarity and Selection by Inspiration. All methods
require input data in the form of design requirements
specific for each method.
Selection by Analysis is the most systematic and
robust as input requirements are objectives,
functions, and constraints, and furthermore, they are
precisely defined and unambiguous. Its deficiency
derives from this particular distinctiveness, which
causes the method to fail in the case of imprecise
inputs or imperfectly formulated rules. Previous
experience and analogy are key factors in the
Selection by Synthesis method, where design
requirements appear in the form of intentions,
features, and perceptions. This method is used, when
knowledge of the solved cases can be exploited and
transferred to other product with some features in
common. Selection by Similarity is the selection
method, where input is already known or potential
material solution and its purpose is to find
substitutive material for an existing product, often
initiated by design requirement changes due to e.g.
environment legislation. The less uniformed method
is Selection by Inspiration, where input is pure
curiosity and the designer’s task is to examine and
analyse other solutions for a specific feature, in a
systematic way. This method is used when no
scientific method is helpful. All material selection
methods and their variations are implemented in
numerous variations as engineering praxis.
2.2 Polymer Material Selection
in Praxis
Usually the methodology of material selection
involves making a list of properties that you must
have for future application and the list of properties
that are desired for this particular application. These
must and want properties are then matched with the
properties of available polymer materials on the
market. In engineering praxis, four basic groups of
material properties are reviewed:
Physical (specific heat, coefficient of thermal
expansion, thermal conductivity, heat distortion
temperature, glass transition temperature)
Chemical (composition, additives, fillers,
crystallinity, environmental degradation, spatial
configuration, molecular weight, flammability)
Mechanical (tensile and compressive properties,
heat distortion, pressure-velocity limit, toughness,
stress rupture resistance, creep resistance)
Dimensional considering manufacturing condi-
tions (manufacturing tolerances, stability, available
sizes, moldability, surface texture)
In order to illustrate the importance of polymer
materials’ idiosyncrasies (Budinski and Budinski,
2010), each group of followed properties should be
described.
2.2.1 Physical Properties
Physical properties are material characteristics that
pertain to the interaction of these materials with
various forms of energy and human senses.
Generally they could be measured without
destroying the material. Density is a physical
property determined with weighting or measuring
the volume of the product. Physical properties like
feel and colour are even easier to determine while
they affect the customer as he or she only looks at it.
Nevertheless, they are not marginal material
properties and their importance rises in today’s
consumer oriented society. The designer has to
acknowledge that plastic feels different from metal
and yellow is happier colour in comparison to
brown.
2.2.2 Chemical Properties
Chemical properties are related to the structure of
polymer material, its formation from the elements of
which the material is made, its reactivity with
chemicals and environments. These properties
cannot be visually inspected and are measurable in
chemical laboratory.
2.2.3 Mechanical Properties
Mechanical properties are the features of material,
which are put on view when it is exposed to a force.
They are related to the elastic or plastic behaviour of
the polymer and they often require destruction for
measurement. Term mechanical is used because they
are usually used to indicate the suitability of the
material for use in mechanical applications – parts
that carry a load, absorb shock, resist wear, etc.
2.2.4 Dimensional Properties
Dimensional properties include as well
manufacturing considerations like manufacturing
tolerances and moldability. This category concerns
also the surface texture and its roughness, which is
measurable and essential for many applications.
Available size, shape, finish and tolerances of the
product are also important polymer material
selection factors.
ICAART 2011 - 3rd International Conference on Agents and Artificial Intelligence
708