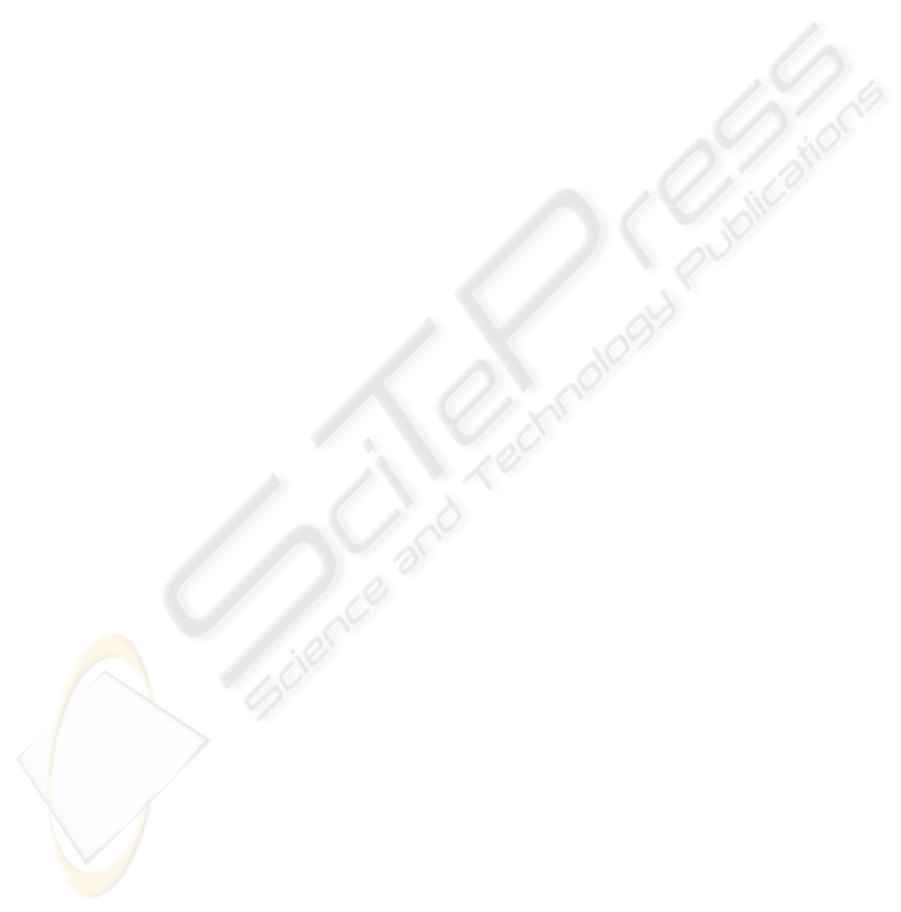
individual software or “no software” solutions.
Although there are many old systems in use the
companies are highly satisfied and prefer solutions
decoupled from the ERP-system. In particular the
segments quality assurance and staff work time
logging are concerned.
Based on the findings of this study, one may
generally conclude that for the majority of the
medium-sized companies in the production industry
the term MES is largely unknown. Even if some
enterprises are familiar with the definition of MES
they are not able to distinguish the functional
environments of a manufacturing execution system.
The most criticised items headed by this group are
the complexity of the MES-market, as well as the
unfeasible commitments from software vendors.
Also remarkable for the authors was that no
enterprise polled in the face-to-face interviews had
implemented a new software-system within the last
three years. The statement of uncertainty relating to
new software was considerable. Companies doubt
that implementation of new MES will bring more
benefits. The case that positive references are
missing has to be mentioned additionally at this
point.
Production enterprises, having long lasting
experience with ERP-system are more willing to
evaluate functions in the area of MES. Their know-
how in implementing and maintaining this standard-
software system is instrumental in realising new IT
systems.
In general there is an unexplainable gap between
the demands and the willingness to invest in the
shop floor. In other words enterprises agreed to the
advantages of an automated workflow but almost
none of the polled companies has an automated
workflow established or is willing to provide the
required resources.
Users that exhaust the functional limits of ERP-
system in the production area are increasingly
claiming for more flexibility and more transparency,
attributes very often expected from MES software.
In the first instance the fixed framework and the not
available real-time data are criticised, a standardised
bi-directional interface between ERP and control
layer does not exist. A high potential is attributed to
this unsolved section.
Looking into the future there is an irrepealable
tendency to integrated systems. The majority of the
medium-sized businesses prefer one fully integrated
IT system as personal resources are regularly
undersized. This fact offers a chance for ERP-
systems. There is still an enormous potential for the
development of ERP-systems in particular
concerning interfaces. These systems have to
provide more and better connectivity in order to
allow easy integration of satellite systems. All in all,
companies are quite happy with their ERP-systems.
In the sector of MES the request for one fully
integrated IT system is more likely to meet the idea
of an integration framework. Moreover enterprises
are reluctant to substitute successful partial software
solutions by a totally integrated MES. Together with
the problem of low IT resources the step of
exchanging the whole software landscape in the
shop floor seems to be too risky for medium sized
companies. But the integration of capsuled MES
functions into a framework with the opportunity of
step by step extension is a worthwhile alternative.
Another benefit of an integration framework is that
MES functionalities like maintenance can easily use
existing functionality of the ERP system.
Information about the production process or
machine parameters are usually collected by several
systems in the shop floor and the ERP. The job of
the integrating framework is to allocate and analyse
the information in order to provide it to a planning
tool.
5 FUTURE RESEARCH
In a test facility different MES scenarios will be
simulated. In one scenario it is planned to cover the
functionalities of an MES by using an off-the-shelf
MES product. In another scenario we are going to
use an IT framework such as xMII for the
integration of dedicated software tools like
scheduler, shop floor data acquisition or tool
management.
REFERENCES
Instrument Society of America, 2000. ANSI/ISA–
95.00.01–2000, Enterprise-Control System
Integration, Part 1: Models and Terminology, North
Carolina.
MESA International, 1997. MESA White Paper #06: MES
Explained: A High Level Vision, Pittsburgh.
Schuh, G., 2006. Produktionsplanung und –steuerung,
Grundlagen, Gestaltung und Konzepte, Springer,
Berlin Heidelberg, 3rd Edition.
Trovarit AG, 2004. MES-Echtzeit in der Fertigung?!,
Aachen.
VDI Berichte 5600, 2006. Manufacturing Execution
Systems - Fertigungsmanagementsysteme, Blatt 1,
Beuth Verlag, Berlin, First draft.
IT APPLICATIONS IN PRODUCTION PLANNING AND CONTROL - A Survey of Medium Sized Business in
German-speaking Europe
291