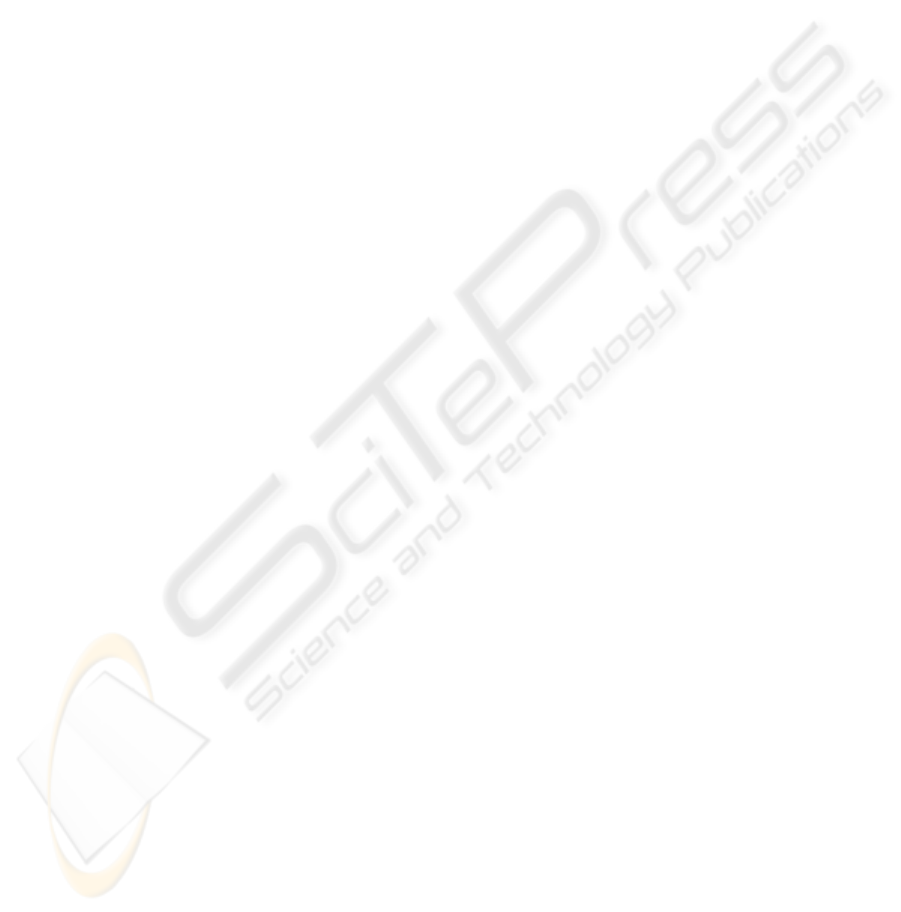
2 SELECTION
AND DESCRIPTION OF
THE PROCESS MODELING
TECHNIQUE
Utilization of business process modelling
methodologies varies depending on a particular
purpose or activity. Business process models can be
used as aids in re-engineering processes, for testing
the processes or for developing simulation systems
to automate the processes and so on. As widely
exploited traditional process modelling tools can be
recognized Flow charts, Data flow diagrams,
Control flow diagrams, Functional flow block
diagram, Gantt and PERT charts without the
exception of others. Some of them provide only
limited possibilities without power to properly
describe complicated models of cooperating
processes. Among very common modelling methods
belong also IDEF models. There are several types of
IDEF models. The most familiar are IDEF0
diagrams that model the tasks performed by an
organization at a high level of abstraction. Process
details are captured in IDEF3 diagrams. The major
IDEF methods in use are described for instance by
Mayer, Painter, deWitte (1992). Since modelling by
IDEF0 diagrams is very usable tool also for applying
and adopting of the process approach philosophy in
organization it inspired to use this method as a base
for modelling of real manufacturing system.
Process mapping by this technique begins with
the description the system as a whole at the highest
level and then decomposing this model level by
level to describe each of the sub-systems within the
system hierarchy. The IDEF0 notation was
standardized in 1993 by the National Institute of
Standards and Technology of the USA (FIPS, 1983).
Use of this standard permits the construction of
models comprising system functions (activities,
actions, processes, and operations), functional
relationships, and data (information or objects) that
support systems integration. The another reason for
a selection of the IDEF0 model is that it is composed
of a hierarchical series of diagrams that gradually
display increasing levels of detail describing
functions and their interfaces within the context of a
system (see fig 1a). Moreover, simple text and
glossary diagrams, which provide additional
information in support of graphic diagrams, help to
bridge semantic gaps between model designers and
model users.
The above mentioned process modelling tools
presents naturally only a fraction of the
methodologies used over the last decades. Hommes
(2005) has identified twenty different techniques and
over 350 different process modelling tools. A new
group of methodologies is under development to
meet the needs of modern e-businesses technology.
3 MODIFIED VERSION OF IDEF0
3.1 Some Identical Signs of Original
and Modified IDEF0 Version
Both modified and original versions:
- compose of a hierarchical tree of diagrams that
gradually display increasing levels of detail
describing functions and their relations within the
context of a system. They use three types of
structured representations: graphic, text, and
glossary. The graphic diagrams define functions and
functional relationships via box and arrow syntax.
Text and glossary components provide additional
information in support of graphic diagrams,
- provide a systems engineering approach to
performing systems analysis and design at all levels,
for systems composed of people, machines,
materials, computers and information of all varieties
and producing reference documentation concurrent
with development to serve as a basis for integrating
new systems or improving existing systems,
- are offering reference architecture for enterprise
analysis, information engineering and resource
management,
- use common syntax, where arrows represent data
or objects related to functions. Rules define how the
components are used, and the diagrams provide a
format for depicting models both verbally and
graphically. A box provides a description of what
happens in a designated function. Arrows that bend
shall be curved using only 90 degree arcs.
3.2 Some Staple Differences between
Original and Modified IDEF0
Versions
The box name in the modified version is noun that
labels the object (process or entity) and moreover is
denoted by alphabetic character with index
describing the level of process decomposition.
Objects are classified to six basic classes. Five of
them are hierarchically arranged from top to bottom
as follows (Modrák, 2005):
- Unified Enterprise Process (UEP),
- Integrated Process (IP),
CASE ON MODELING OF MANUFACTURING SYSTEMS BY MODIFIED IDEF0 TECHNIQUE
307