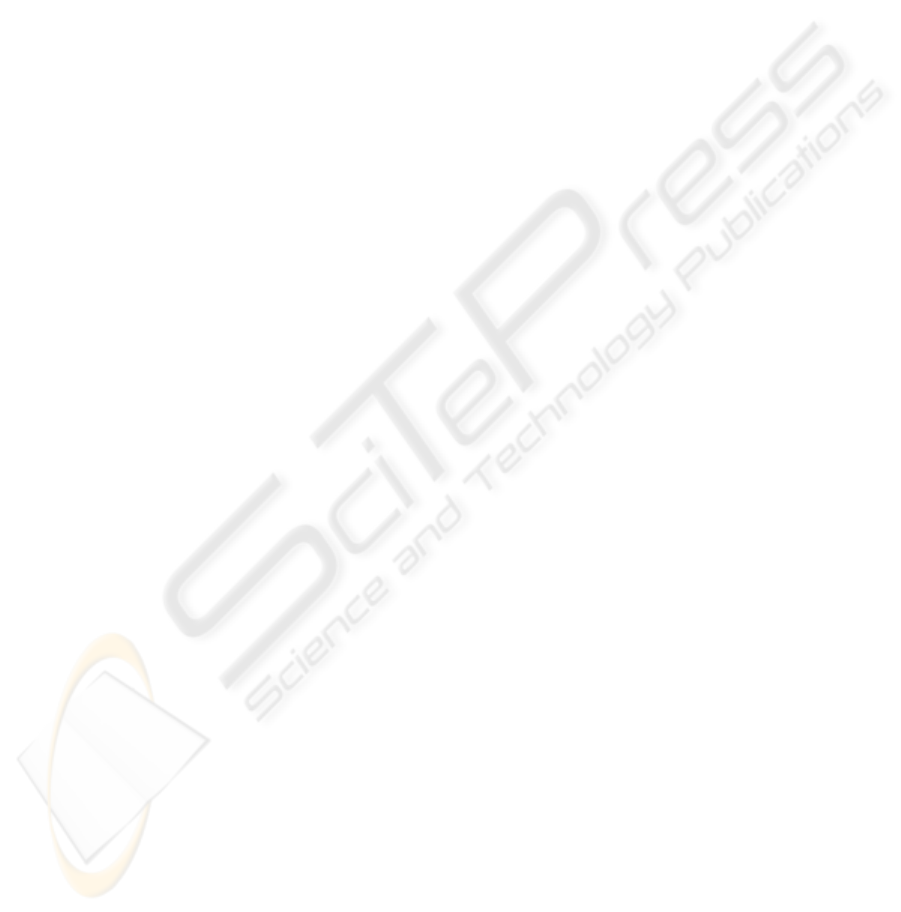
USING 3D FEATURES TO EVALUATE CORK QUALITY
Beatriz Paniagua-Paniagua
1
, Miguel A. Vega-Rodríguez
1
, Hiroshi Nagahashi
2
Juan A. Gómez-Pulido
1
and Juan M. Sánchez-Pérez
1
1- Dept. Technologies of Computers and Communications. Extremadura University
Escuela Politécnica. Campus Universitario, s/n. 10071. Cáceres. Spain
2- Imaging Science and Engineering Laboratory. Tokyo Institute of Technology
R2-51, 4259 Nagatsuta-cho, Midori-ku, Yokohama 226-8503, Japan
Keywords: Image processing, cork quality classification, 3D feature extraction.
Abstract: In this paper we study different 3D features in cork material. We do this in order to solve a classification
problem existing in the cork industry: the cork stopper/disk quality classification. Cork Quality Standard
sets seven different cork quality classes for cork stopper classification. These classes are based on a
complex combination of cork stopper defects. In previous studies we only analysed those features that could
be detected/acquired with a 2D camera. In this study we work in a 3D environment, in order to extract those
features that we could not be extracted in a 2D approach. As a conclusion we can say that the most
important 3D cork quality detection feature takes into account dark and deep cork areas (usually, these areas
indicate deep and important defects). Furthermore, the 3D features have widely improved the results
obtained by similar features with a 2D approach, due to the 3D approach includes more information. This
fact allows us to extract more complex features, as well as improve the classification results.
1 INTRODUCTION
Oak is a tree that mostly grows in the western shores
of the Mediterranean Sea. Because of this fact, the
cork industry has a big economic importance and
great research interest in the native zones of this
material.
The most important industrial application of cork
is the production of disks and stoppers for sealing
wines, ciders, and champagnes. In the cork industry,
stoppers and disks are classified in different quality
classes based on a complex combination of its
defects. Due to this high heterogeneity degree,
traditionally, the classification process has been
carried out by human experts manually.
At the moment, there are several models of
electronic machines for the cork stoppers
classification in the market. The performance of
these machines is acceptable for high quality
stoppers/disks, but for medium or low quality, the
number of samples classified erroneously is large. In
conclusion, the stoppers/disks should be re-
evaluated by human experts later. This increases the
process price and the production time because a
human expert needs a minimum training period of 6
months to attain minimum classification accuracy,
although the learning process can last years.
Furthermore, a human classifier can introduce some
mistakes on the classification due to his/her
subjectivity degree. In conclusion, more research
efforts are necessary in the automatic cork
classification field.
We have to add to these reasons the fact that
Spain produces 31% (ASECOR, 2006) of the
worldwide cork. All these motivations have lead us
to the development of this research, whose final
main objective is the construction of a computer
vision system for cork classification based on
advanced methods of image processing and feature
extraction in order to avoid the human evaluation in
the quality discrimination process.
In this work we try to prove the accuracy of new
3D features in cork quality classification. In
previous works (Paniagua-Paniagua et al, 2006a;
Paniagua-Paniagua et al, 2006b), a wide study about
feature extraction was made. Now, we try to analyse
the automatic feature extraction of cork quality,
within a 3D approach. We have focused this study
on feature extraction, and several new cork quality
3D features have been obtained. We will test the
79
Paniagua-Paniagua B., A. Vega-Rodríguez M., Nagahashi H., A. Gómez-Pulido J. and M. Sánchez-Pérez J. (2007).
USING 3D FEATURES TO EVALUATE CORK QUALITY.
In Proceedings of the Second International Conference on Signal Processing and Multimedia Applications, pages 79-84
DOI: 10.5220/0002136700790084
Copyright
c
SciTePress