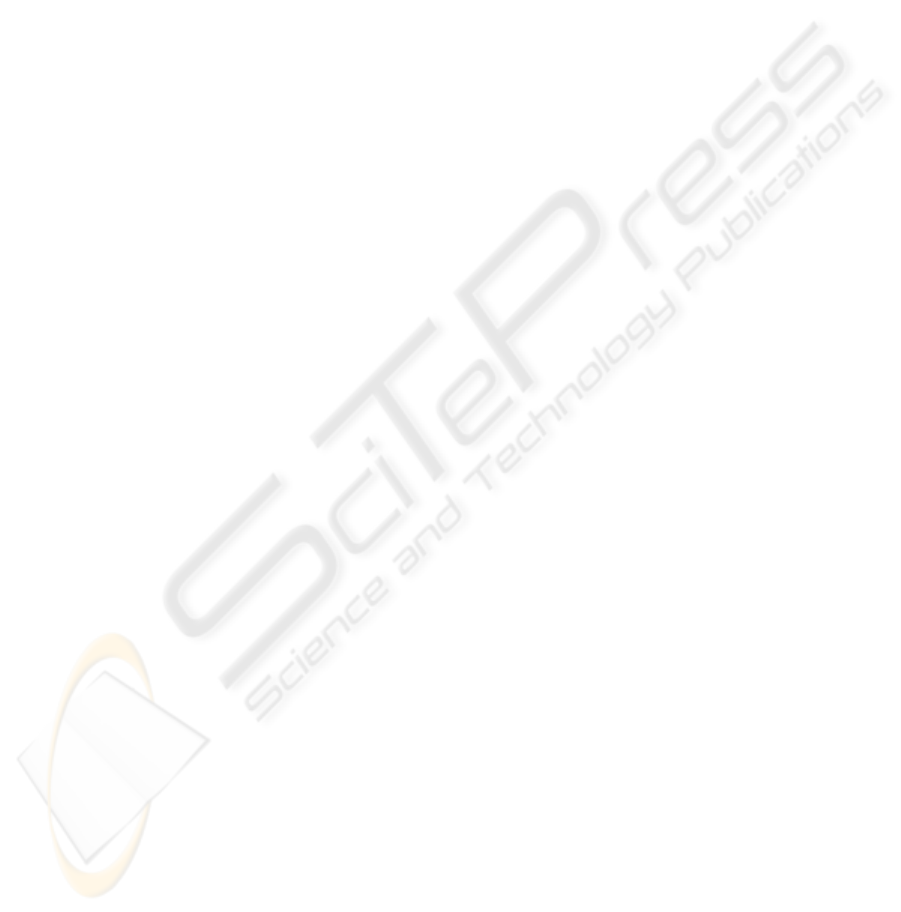
REFERENCES
Albino, V., Garavelli, A. C., and Okogbaa, O.G. (1998).
“Vulnerability of production systems with multi-
supplier network: a case study.” International Journal
of Production Research, 36(11), pp.3055-3066.
Almgren, H., (1999). “Towards a framework for analyzing
efficiency during start-up: An empirical investigation
of a Swedish auto Manufacturer.” International
Journal of Production Economics, 60-61, pp.79-86.
Al-Najjar, B., (1996). “Total quality maintenance An
approach for continuous reduction in cost of quality
products.” Journal of Quality in Maintenance
Engineering, 2(3), pp. 4-23.
Bamber, C. J., Sharp, J. M., and Hides, M.T., (1999).
“Factors affecting successful implementation of total
productive maintenance.” Journal of Quality in
Maintenance Engineering, 5(3), pp.162-181.
Beach, R., Muhlemann, A. P., and Price, D.H.R., (2000).
“Manufacturing operations and strategic flexibility:
survey and cases.” International Journal of
Operations & Production Management, 20(1), pp.7-
30.
Bever, K., (2000), “Understanding Plant Asset
Management Systems”, Maintenance Technology,
July/August, pp. 20-25
Blanchard, B. S., (1997). “An enhanced approach for
implementing total productive maintenance in the
manufacturing environment.” Journal of Quality in
Maintenance Engineering, 3(2), pp.69-80.
Duffuaa, S., Ben-Daya, M., Al-Sultan, K., and Andijani,
A., (2001), “A Generic Conceptual Simulation Model
for Maintenance Systems”, Journal of Quality in
Maintenance Engineering, 7(3), pp. 207-19.
Duffuaa, S.O., Cambel, J.D., and Raouf, A., (1999),
“Planning and Control of Maintenance Systems:
Modelling and Analysis”, John Wiley & Sons, New
York.
Grobholz, H. R., (1988), “Managementaufgabe
Instandhaltung”, 2 Auflage
Honkanen, T., (2004), “Modelling Industrial Maintenance
Systems and the Effects of Automatic Condition
Monitoring”, Phd Thesis, Helsinki University of
Technology, Information and Computer Systems in
Automation
Horner, R., El-Haram, M., and Munns, A., (1997),
“Building maintenance strategy: a new management
approach”, Journal of Quality in Maintenance
Engineering, 3(4), pp. 273-280.
IIM, ( 2002), “International Infrastructure Manual”,
National Asset Management Steering Group, Australia
New Zealand Edition, Thames, ISBN 0-473-09137-2
Intentia, (2004), “Enterprise Asset Management
Benchmark Survey: How do you measure your
maintenance performance?”, The Maintenance
Journal. February, pp.52 -70.
Jonsson, P., (1999), “The Impact of Maintenance on the
Production Process - Achieving High Performance”,
Doctoral thesis, Division of Production Management,
Lund University. Lund, Sweden.
Koc, M., Lee, J., (2003), “A System Framework for Next-
Generation E- Maintenance Systems”, IMS: Centre for
Intelligent Maintenance Systems, Milwaukee, accessed
online at http://www.uwm.edu/CEAS/ims/pdffiles/E-
Maintenance.PDF, on June 27, 2004.
Lawrence, J. L., (1999), “Use mathematical modeling to
give your TPM implementation effort an extra boost.”
Journal of Quality in Maintenance Engineering, 5(1),
pp. 62-69.
Lee, J., (2003), “E-Intelligence Strategies for Product
Manufacturing Innovation”, IMS: Centre for
Intelligent Maintenance Systems, Milwaukee, accessed
online at
http://www.uwm.edu/CEAS/ims/pdffiles/EIntelligence
Strategies.PDF,on June 27, 2004.
Matson, J., and McFarlane, D., (1998), “Tools for
Assessing the Responsiveness of Existing Production
Operations”, IEE Workshop on Responsiveness in
Manufacturing, London, UK, February.
Moubray, J., (1991), “Reliability-centred Maintenance”,
Oxford, Butterworth-Heinemann Ltd.
Moubray, J., (2003), “21st Century Maintenance
Organization Part I: The Asset Management Model”,
Maintenance Technology, accessed online at
http://www.mt-
online.com/articles/0203_asset_mgmtt.cfm, on July
12, 2004.
Nakajima, S., (Eds). (1989), “TPM Development
Program: Implementing Total Productive
Maintenance”, Cambridge, Productivity Press, Inc.
Sandberg, U., (1994), “The Coupling Between Process
and Product Quality – The interplay Between
Maintenance and Quality in Manufacturing”,
Euromaintenance ´94, Amsterdam.
Taskinen, T., and Smeds R., (1999), “Measuring change
project management in manufacturing.” International
Journal of Operations & Production Management,
19(11), pp. 168-1187.
Warnecke, H. J., and Hueser, M., (1994), “Technologies
of Advanced Manufacturing”, Organization and
Management of Advanced Manufacturing, W.
Karwowski and G. Salvendy (Eds), New York, John
Wiley & Sons INC:.
Woodhouse, J., (2001), “Asset Management”, The
Woodhouse Partnership Ltd, online accessed on May
10, 2004 at http://www.plant-
maintenance.com/articles/AMbasicintro.pdf
Yamashina, H., and Otani, S., (2001), “Optimal Preventive
Maintenance Planning For Multiple Elevators”,
Journal of Quality in Maintenance Engineering, 7(2),
pp. 128-50.
ICEIS 2005 - INFORMATION SYSTEMS ANALYSIS AND SPECIFICATION
322