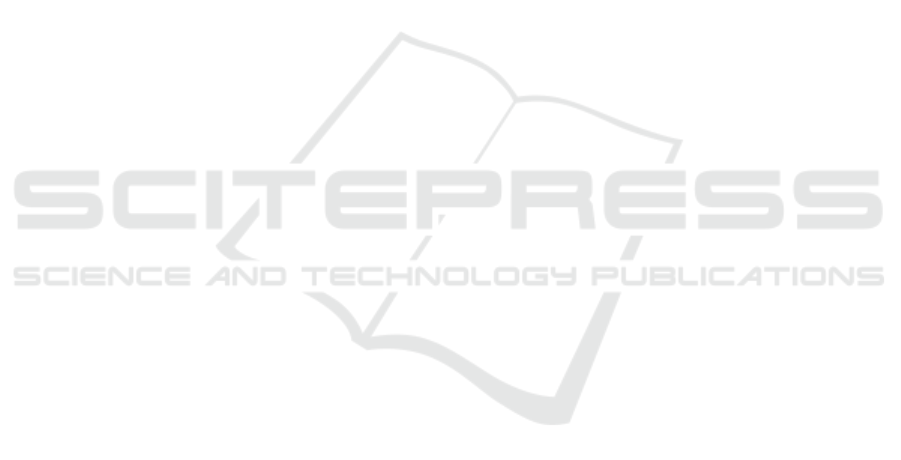
Brazilian electoral system has constant challenges re-
lated to the transparency, reliability and security of the
process as a whole. Therefore, there are several ways
to audit and test the polls.
As mentioned before, tests and inspections are
carried out at least every 3 months in the Brazilian
electronic voting machines, in order to ensure their in-
tegrity. One of the main tests carried out in this regard
is the Electronic Ballot Box Integrity Test, which is a
parallel vote to the official one, which aims to demon-
strate the proper functioning of the equipment and the
security of the Electronic Ballot Box. This process
starts the day before the elections; in which 641 elec-
tronic voting machines, randomly selected from ap-
proximately 500,000 voting machines, are removed
from their polling stations and replaced by new ones.
The selected voting machines are then taken to the
place where the Integrity Test will take place. In or-
der to carry out this voting equivalent to the official
vote, the process begins on the eve of the elections,
when a public ceremony takes place for the draw-
ing of the voting machines that will participate in the
tests. Then, the randomly selected electronic voting
machines are transported from their original sections
to the place where the integrity test is carried out, and
the entire audit process is monitored by cameras. In
parallel with the draw, to simulate voters, voting bal-
lots are filled out by students from the public educa-
tion network, representatives of political parties and
coalitions, which are deposited in sealed canvas urns.
On election day, the integrity test starts at the same
time as the official voting and the first procedure is
to print the zero, which is an extract that proves the
absence of votes counted in the electronic voting ma-
chine. Then, all votes from the ballots that were filled
in earlier are entered, one by one, in a parallel sys-
tem. At the end of the day, a Ballot Box Report (BU)
is printed and the auxiliary system also issues a bul-
letin. This way, both countings are compared in order
to verify if the electronic voting machine worked nor-
mally, verifying that the votes received are in accor-
dance with the votes counted.
Currently, the Integrity Test process has the par-
ticipation of 6 (six) to 8 (eight) people per Electronic
Ballot Box to be audited. To increase productivity
and reduce the chance of human error involved in
the testing process, a solution for test automation was
devised: this alternative solution uses a robotic arm
guided by computer vision and 1 (one) human being.
However, even with the automation of the process,
it was still necessary to map the robot’s position man-
ually, so the main focus of this work is to present a
process for the automatic mapping of the keys of the
electronic voting machine as a whole. We use a robot
with Cartesian motion support, enabling the mapping
of robot coordinates to the RGB-D camera coupled on
it using computer vision techniques and deep learn-
ing, so that the machine understands what it is seeing.
The results obtained by this work were considered
satisfactory, where our macro project, which is the
”automation of the audit of the functioning of elec-
tronic voting machines in Brazilian elections” won a
technological innovation award in the Brazilian judi-
ciary and was presented to the minister of the federal
supreme court( STF), who at the time was the presi-
dent of the Superior Electoral Court (TSE). In addi-
tion, as a technical result, it was possible to detect,
track and map all the keys on the Brazilian electronic
voting machine.
The present work is structured as follows. Sec-
tion 2 presents the background, which shows what
was used to create our solution. Section 3 describes
the methodology used to create our solution. Section
4 describes the tests and results, while section 5 con-
cludes the work and points future work directions.
2 RELATED WORKS
Garcia et al. (Garcia et al., 2013) used a mapping
approach very similar to the one of this work. They
also used four target points to guide the robotic arm
in tasks of interacting or manipulating objects within
the created workspace. The depth information in the
image improves the accuracy of the trajectory calcu-
lation.
Singh, Rakesh et al. (Singh and Kotecha, 2021)
do a work focused on the optimization of the SLAM
algorithm, the authors propose to use the deep learn-
ing technique to improve the SLAM algorithm so that
it is able to differentiate between static and dynamic
objects.
Viturino et al.(Viturino et al., 2021) used an in-
stance segmentation method (Mask R-CNN), a point
cloud collision verification system and a path plan-
ning technique with orientation control based on the
Adaptive Artificial Potential Field algorithm to detect
and grasp objects using a robotic arm with 6DoF.
3 BACKGROUND
In this section, we will present the main concepts
that were underneath the proposed solution. We start
by providing some background related to object de-
tection and specifically YOLO’s neural network, and
end the section talking about the benefits of using an
VISAPP 2023 - 18th International Conference on Computer Vision Theory and Applications
688