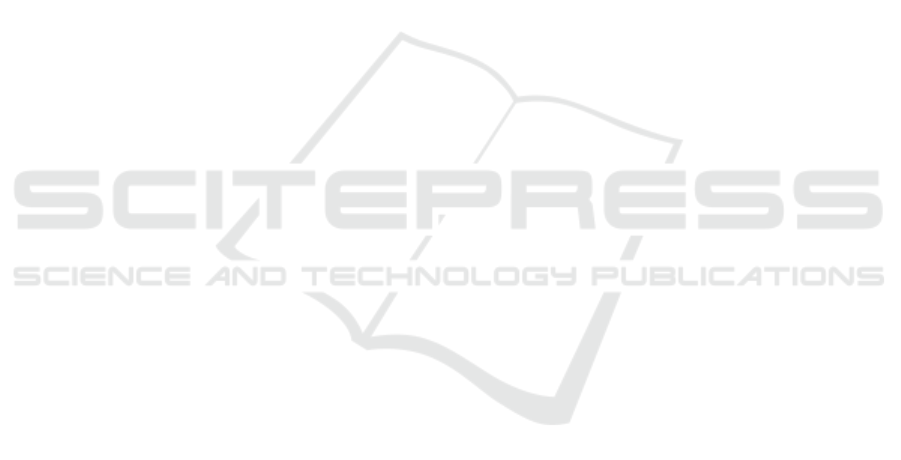
a guaranteed optimal solution could be found),
• the computation time (in seconds).
We first note that the computational effort needed
to solve the problem with a mathematical program-
ming solver is drastically reduced when using the
PLSP-based model instead of the GLSP-based model.
Thus, for the small instances, the proposed PLSP-
based model can be solved to optimality within less
than 2s, while the GLSP-based model cannot con-
verge to the optimal solution after 20 minutes of
computation: see Table 2. Moreover, for the set
of medium and large instances, no feasible solution
can be found by the solver in 20min when using
the GLSP-based model. In contrast, the PLSP-based
model is able to provide feasible solutions of accept-
able quality. The integrality gaps seem to be simi-
lar for both formulations (see in particular Table 2).
Thus, the observed improvement in the computational
efficiency may be mainly explained by the significant
decrease in the size of the MILP formulation obtained
when using the PLSP-based model.
In terms of solution quality, the GLSP-based for-
mulation is more flexible regarding the production
plan than the PLSP-based formulation. Namely, the
GLSP-based model allows the production of more
than 2 different types of items in a given energy-
oriented microperiod, which is forbidden in the
PLSP-based model. Thus, theoretically, the GLSP-
based model may provide less expensive production
and energy supply plans. However, in practice, as
can be seen in the results reported in Table 2, the
value of the optimal solution found by the PLSP-
based model is equal or very close to the one found
by the GLSP-based model. Thus, the GLSP-based
model is able to provide a lower cost production plan
than the PLSP-based model in only four instances
out of the 30 corresponding instances. Moreover, the
maximum observed relative cost difference over these
four instances is only 0.05%. This indicates that in
most cases, the optimal solution obtained by the PLSP
model is of the same cost as the one obtained by the
GLSP model.
5 CONCLUSION AND
PERSPECTIVES
This paper investigated an integrated lot-sizing and
energy supply planning problem in a single-machine
multi-product setting. A new MILP model based on
an extension of the PLSP was proposed to handle
this problem. Our numerical results showed that the
proposed model outperforms a previously published
GLSP-based model with respect to the computation
times. However, the availability of the renewable
energy resources heavily depends on weather condi-
tions, so that the corresponding power generation can-
not be predicted precisely. Therefore, future work
should focus on explicitly taking into account these
uncertainties in the problem modeling.
REFERENCES
Belvaux, G. and Wolsey, L. A. (2001). Modelling practical
lot-sizing problems as mixed-integer programs. Man-
agement Science, 47(7):993–1007.
Biel, K., Zhao, F., Sutherland, J. W., and Glock, C. H.
(2018). Flow shop scheduling with grid-integrated on-
site wind power using stochastic MILP. International
Journal of Production Research, 56(5):2076–2098.
Copil, K., W
¨
orbelauer, M., Meyr, H., and Tempelmeier, H.
(2017). Simultaneous lotsizing and scheduling prob-
lems: a classification and review of models. OR Spec-
trum, 39(1):1–64.
Drexl, A. and Haase, K. (1995). Proportional lotsizing and
scheduling. International Journal of Production Eco-
nomics, 40(1):73–87.
Fleischmann, B. and Meyr, H. (1997). The general lotsizing
and scheduling problem. OR Spectrum, 19(1):11–21.
Gao, K., Huang, Y., Sadollah, A., and Wang, L. (2020).
A review of energy-efficient scheduling in intelligent
production systems. Complex & Intelligent Systems,
6(2):237–249.
Golp
ˆ
ıra, H., Khan, S. A. R., and Zhang, Y. (2018). Ro-
bust smart energy efficient production planning for a
general job-shop manufacturing system under com-
bined demand and supply uncertainty in the presence
of grid-connected microgrid. Journal of Cleaner Pro-
duction, 202:649–665.
Johannes, C., Wichmann, M. G., and Spengler, T. S.
(2019). Energy-oriented production planning with
time-dependent energy prices. Procedia CIRP,
80:245–250.
Rodoplu, M., Arbaoui, T., and Yalaoui, A. (2019). Single
item lot sizing problem under renewable energy un-
certainty. IFAC-PapersOnLine, 52(13):18–23.
Terbrack, H., Claus, T., and Herrmann, F. (2021). Energy-
oriented production planning in industry: a systematic
literature review and classification scheme. Sustain-
ability, 13(23):13317.
Wang, S., Mason, S. J., and Gangammanavar, H. (2020).
Stochastic optimization for flow-shop scheduling with
on-site renewable energy generation using a case in
the United States. Computers & Industrial Engineer-
ing, 149:106812.
Wichmann, M. G., Johannes, C., and Spengler, T. S. (2019).
Energy-oriented lot-sizing and scheduling considering
energy storages. International Journal of Production
Economics, 216:204–214.
Zhang, H., Cai, J., Fang, K., Zhao, F., and Sutherland, J. W.
(2017). Operational optimization of a grid-connected
factory with onsite photovoltaic and battery storage
systems. Applied Energy, 205:1538–1547.
ICORES 2023 - 12th International Conference on Operations Research and Enterprise Systems
126