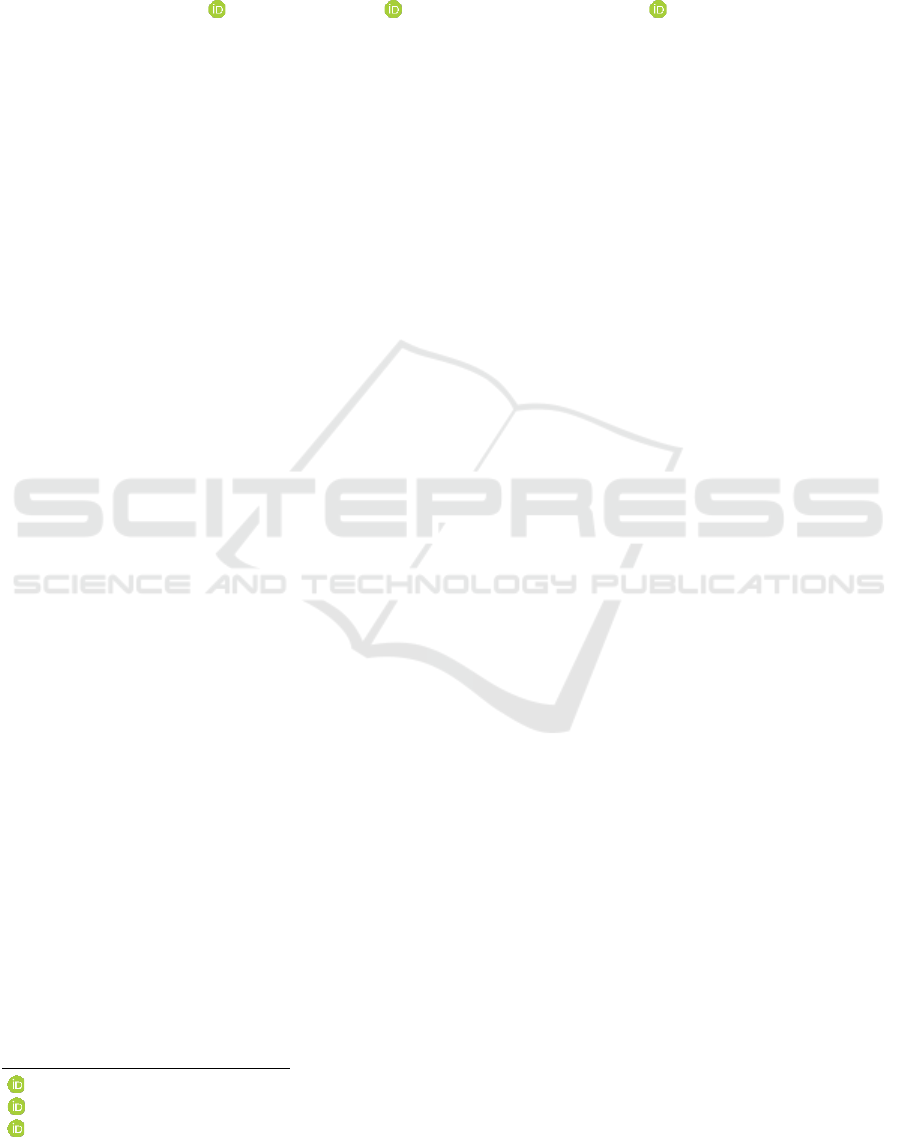
Progressive Hybrid Stamping Tool Development on Automotive
Components Stay Headlight Material SPC270C
Aida Mahmudah
a
, Metha Islameka
b
, Rofan Yulian Romansyah
c
and Sigit Permana
Design Engineering Department, Politeknik Manufaktur Bandung, Jl. Kanayakan No. 21, Bandung, Indonesia
Keywords: Progressive Hybrid Tool, Stay Headlight, SPC270C.
Abstract: Stay headlight component is a product that requires several stages in its manufacture. The production process
used one compound tool and one group tool mounted on two different press machines. Progressive hybrid
tools can be used to reduce the number of operators, press machines, and speed up processing times. A
progressive hybrid tool is a stamping tool used to produce components from sheet metal materials. In
progressive hybrid tools, the combined process consisting of cutting and forming processes occurs
continuously. In this study, the initial development of a progressive hybrid tool was carried out to produce a
stay headlight component that functions as a vehicle headlight holder. The material used is SPC270C, with a
thickness of 1.6 mm. The design method used is VDI 2222 (Verein Deutsche Ingenieure 2222), which consists
of 4 main stages: planning, conceptualising, designing, and finishing. This early-stage development results in
a progressive hybrid tool design consisting of 11 process stations with a material efficiency of 57.6%. The
tool's dimensions are 845 mm long, 640 mm wide, and 370 mm high. The total force required on this tool is
64.86 tons.
1 INTRODUCTION
The automotive industry is one of the main sectors
contributing to the national economy. The automotive
industry is currently experiencing an increase. This is
in line with the development of technology and
components in vehicles. The development of
manufacturing processes to improve the efficiency of
the production process has become a necessity for the
industry as an active player in manufacturing
activities. The stamping process is one manufacturing
process to produce components from sheet metal
materials, for example, automotive components,
medical equipment, household equipment, and so on
(Thomas et al., 2000; Su et al., 2022). Automotive
components are the most needed stamping products
with a wide variety of materials, shapes, and
dimensions. So that the development of process
quality and production acceleration is necessary in
line with the increasing demand for components
(Silva et al., 2021). The development of precision tool
technology is an alternative solution that can be done
to increase production efficiency without reducing
a
https://orcid.org/0000-0002-7124-0824
b
https://orcid.org/0000-0003-4578-8850
c
https://orcid.org/0000-0001-9216-785X
the quality of the resulting product (Shakkarwal et al.,
2021).
The stay headlight component is one of the
components on the front of the vehicle that functions
as a vehicle headlight holder. This component is made
of SPC270C material with a thickness of 1.6 mm.
This product goes through several process stages:
cutting, forming and bending. The process is carried
out using two stamping tools, the compound tool
(cutting process) and the group tool (forming and
bending process). Both tools are installed on two
different press machines with two operators.
Furthermore, based on the analysis of the stay
headlight product, the result is that the product can be
formed with a continuous process stage using one
tool, namely the progressive hybrid tool. Progressive
hybrid tools are often recommended for mass
production of stamped parts requiring complex press
operations (Karimov, 2021). By using one tool, the
number of press machines and operators needed is
reduced. This, of course, can also reduce energy
consumption and production process costs (Gen and
Yunong, 2020). Therefore, an initial step is necessary
Mahmudah, A., Islameka, M., Romansyah, R. and Permana, S.
Progressive Hybr id Stamping Tool Development on Automotive Components Stay Headlight Material SPC270C.
DOI: 10.5220/0011806400003575
In Proceedings of the 5th International Conference on Applied Science and Technology on Engineering Science (iCAST-ES 2022), pages 375-380
ISBN: 978-989-758-619-4; ISSN: 2975-8246
Copyright © 2023 by SCITEPRESS – Science and Technology Publications, Lda. Under CC license (CC BY-NC-ND 4.0)
375