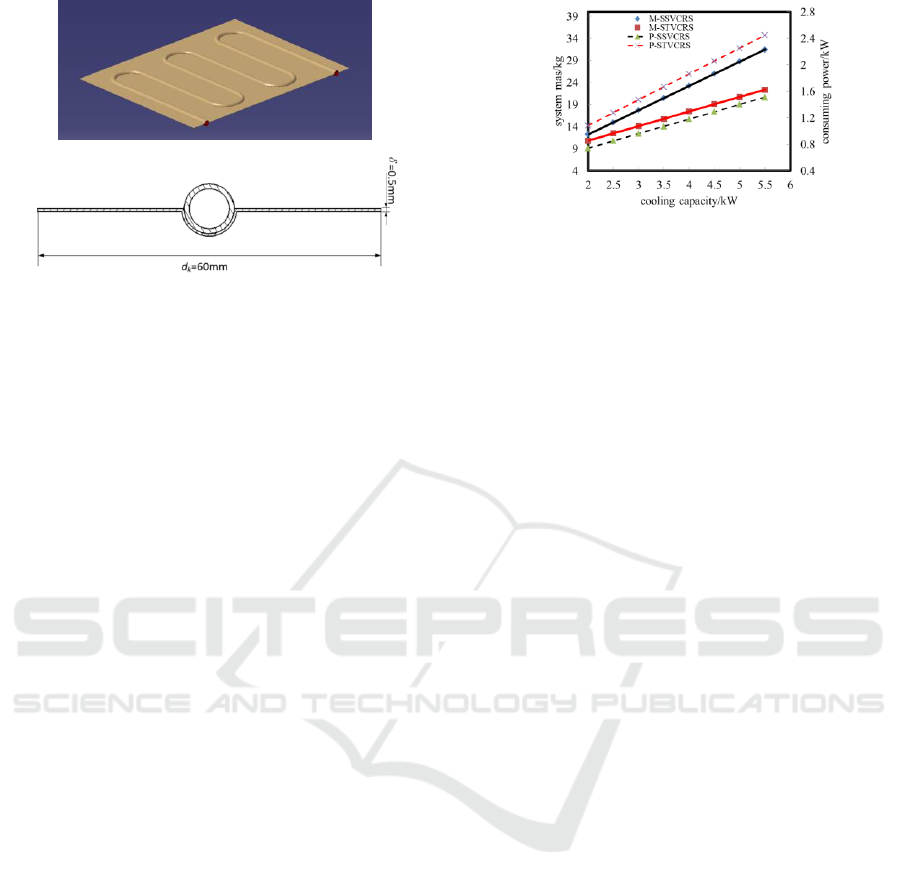
Figure 5: Schematic of radiation condensers.
The estimated correlations of the condenser mass
with the cooling capacity of a SSVCRS and
TSVCRS are shown below respectively:
(4) Expansion valve
The thermal expansion valve is selected by the
Danfoss TCEL3.5 type thermal expansion valve
(suitable for the range of refrigeration is not more
than 12kW), its weight is about
(5) Refrigerant charge
The Enviros Consulting Ltd. "Refrigerant Charge
Calculator" software is used to make a simple
estimate of the weight and charging amount of the
heat exchanger. There is no high or low pressure
storage tank in the estimation. At the same time, the
lubricating oil is not considered because of the oil-
free centrifugal refrigerating compressor used in this
work.
(6) Load cooling circuit
According to the market research, the ratio of the
cold plate mass to the heat dissipation area is
approximately equal to 8kg/m
2
. The length of the
connecting pipe can be estimated approximately
according to the length of the fuselage, and the pipe
can choose the specifications of the aluminium tube
of
with a mass density of 0.06kg/m.
The mass estimation method of the pump is
according to Eq.4. In addition, the power
consumption of the pump is less than 0.3kW within
the operating range.
Therefore, the relationship between the cooling
capacities with consuming power/mass of the two
systems is given respectively in Figure 6. From the
aspect of mass assessment, TSVCRS has substantial
advantage but high power consumption is not
favoured.
Figure 6: System mass varies with cooling capacity
6 CONCLUSION
This paper proposed two cooling systems of
equipment bay for the long endurance solar-powered
UAV, and conclusion based on systematic analysis
can be summarized as follows:
(1) For the heat sink of the long endurance solar-
powered UAVs in the near space, the conservative
design and system reliability requires only
considering heat transfer based on radiation without
convective component.
(2) As far as system energy consumption
concerns, it is suggested to adopt single stage vapor
cycle system. While, from the perspective of mass
concern, it is suggested to adopt two-stage vapor
cycle system; however, the system is more complex.
(3) Limited by the high altitude thermal
environment for condenser radiation, the condenser
contributes to overall system weight in a larger
portion. By increasing the condensing temperature,
the heat transfer capability and the mass of the
radiation condenser can be reduced. The condenser
design and weight can be optimized in future’s work.
ACKNOWLEDGEMENTS
The research presented in this paper was supported
financially by the National Basic Research Program
of China (the 973 Program) through Grant No.
2012CB720100.
REFERENCES
Gao GL, Song BF, Li ZK and Ding X, 2010. Key
technologies of solar powered unmanned air vehicle.
Flight Dynamics. 28 (1), p1-4. (in Chinese)
ICECTT 2018 - 3rd International Conference on Electromechanical Control Technology and Transportation
90