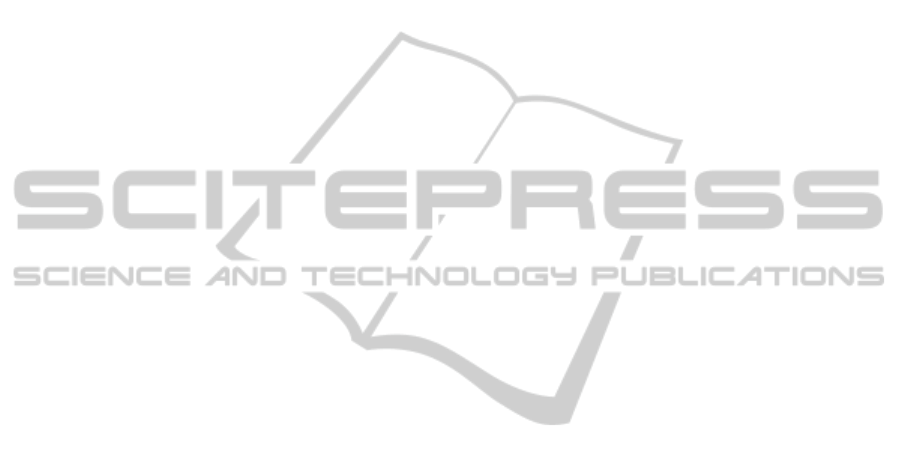
REFERENCES
Erdem E. Y., Chen Y. M., Mohebbi M., Darling R. B.,
Böhringer K. F., Suh J. W., Kovacs G. T., 2010 A
Thermally Actuated Omnidirectional Walking
Microrobot. Journal of Microelectromechanical
Systems; 19 (3), p.433-442.
Ebefors T., Mattson J. U., Kälvesten E., Stemme G., 1999
A walking silicon miro-robot // The 10th Int.
Conference on Solid-State Sensors and Actuators
(Transducers’99) – Sendai, Japan., p. 1202-1205.
Patent of USA US2012/0168233. Robotic devices and
methods / J.V. Clark (US); Purdue research foundation
(US) – Publ. 05.07.2012 – 8p.
Patent of USA US2010/0145511. Microcrawler and
conveyor robots, controllers, systems, and methods /
D.O. Popa (US), R. Murthy (US), A.N. Das (US);
Fulbright&Jaworski L.L.P. (US). Publ. 10.06.2010,
p.17.
The MEMS Handbook, 2002 Edited by Mohamed God-el-
Hak. Mechanical engineering handbook series, CRC
Press, USA, p. 26-63, 26-27.
Harc J. Madou. , 2002 Fundamentals of Microfabrication.
The Science of Miniaturization. Second Edition. CRC
Press, USA, 723 pp.
Patent of Russia RU2518258. Microsystem device for
temperature control of surface of spacecraft / A.A.
Zhukov (RU), I. P. Smirnov (RU), A. S. Selivanov
(RU), D. V. Kozlov (RU), I. V. Churilo (RU). Publ.
10.06.2014, Bull. № 16, 16 p.
Wallace B. P., Hampton P. J., Bradley C. H., Conan R.,
2006 Evaluation of a MEMS Deformable Mirror for
an Adaptive Optics Test Bench // Opt. Express.. №
14(22). P. 10132-10138.
Patent of Russia RU2456720. Microsystem apparatus
controlling surface for mounting small antenna /A. A.
Zhukov (RU), I. P. Smirnov (RU), A. S. Korpukhin
(RU), D.V. Kozlov (RU). Publ. 20.07.2012, Bull. №
20, 15 p.
Norton A., Evans J., Gave D. et al., 2009 Preliminary
Characterization of Boston Micromachines’ 4096-
actuator Deformable Mirror // MEMS Adaptive Optics
III. Proc. SPIE. V. 7209. P. 720901-720901-7.
Ebefors T., Mattson J. U., Kalvesten E., Stemme G. , 1999
A Walking Silicon Micro-robot // The 10th Int. Conf.
on Solid-State Sensors and Actuators (Transducers’
99). Sendai, Japan. P. 1202-1205.
Ebefors T., 2000 Polyimide V-groove Joints for Three-
dimensional Silicon Transducers // Thesis for the
Degree of Doctor of Philosophy at the Royal Institute
of Technology. Stockholm, Sweden. 143 p.
Patent of Russia RU2448896. Thermal micromechanical
actuator and method of making said actuator / A. A.
Zhukov (RU), I. P. Smirnov (RU), A. S. Korpukhin
(RU), D.V. Kozlov (RU), P.G. Babaevsky (RU). Publ.
27.04.2012, Bull. № 12, 20 p.
Bolotnik N. N., Gradetsky V. G., Kozlov D. V., Smirnov
I. P., Chashchukhin V. G., 2015 Physical
characteristics of the sensing elements of feedback
sensors combined with thermomechanical actuators
for plant micromotion control systems. Journal of
Computer and Systems Science International, Vol. 54,
No 1, pp. 140-150.
Gradetsky V. G., Knyazkov M. M., Fomin L. F.,
Chashchukhin V.G., 2010 Miniature robot mechanics.
Nauka, Moscow (in Russian).
Kozlov D. V., Smirnov I. P., Korpukhin A. S., Zhukov A.
A., Babaevsky P. G., Suchorukov A. G. , 2010
Estimation of influence of multicycle bending on
thermal deformation characteristics of elastic-hinged
beams of thermal microactuators. Nano- and
Microsystem Technology, No 12, p. 22-25.
Korpukhin A. S., Babaevsky P. G., Zhukov A. A., Kozlov
D.V., Smirnov I.P., 2011 Influence of forming
conditions and layer width on thermodeformation
characteristics of polyimide-silicon elastic-hinged
beams of thermal actuators. Nano- and Microsystem
Technology, No 2. pp. 34-40.
Xu T. B., Cheng Z. Y., Zhang O. M., 2002 High-
perfomance micromachined unimorph actuators based
on electrostrictive poly(vinylidenc fluoride-
trifluoroethylenc) copolymer. Applied physics letters,
v. 80, #6, pp. 1082-1084.
Yang W. M., Chou S. K., Shu C., Li Z. W., Xue H., 2002
Development of microthermophotovoltaic system.
Applied physics letters, v.81, #27, pp. 5255-5257.
Fahrner W. R., Job R., Werner M., 2001 Sensors and
smart electronic in harch environment applications.
Microsystem Technologies 7(2001), Springer-Verlag,
pp. 138-144.
Kondon Y., Yokota S., 1997 Micro in-pipe mobile
machines by making use an electro-rheological fluid.
Proc. IROS-97, pp. 1672-1677.
ICINCO2015-12thInternationalConferenceonInformaticsinControl,AutomationandRobotics
258