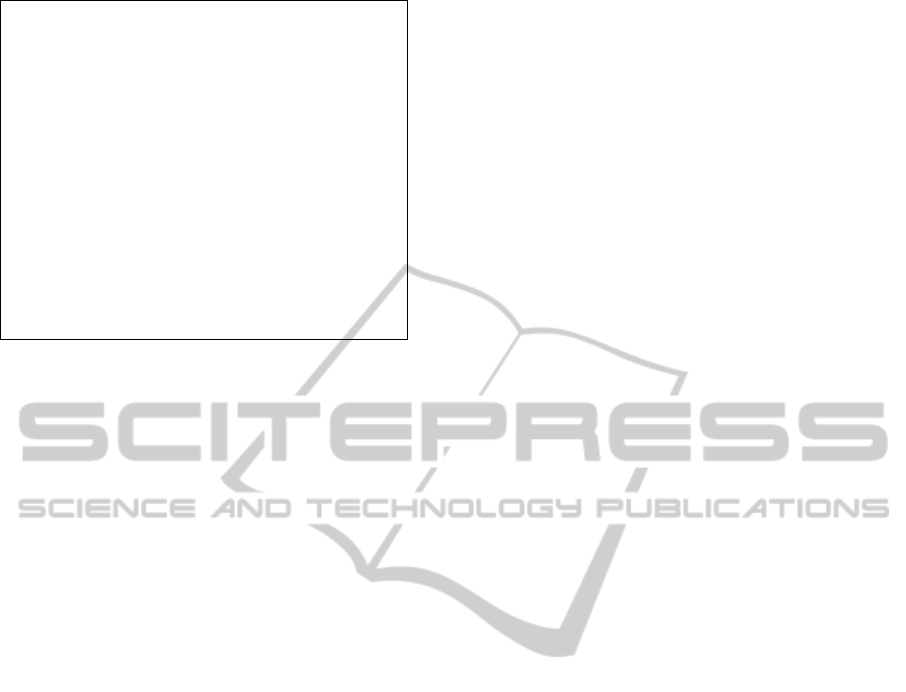
Running example 4
The whole surgery was successfully performed
by BROS under the automatic operating mode
and simulated using RobotStudio and
RobotWare. Only 4 fluoroscopic images were
needed, what makes 21 images less than in the
study case introduced in Section 3. BROS
insured all the intervention steps and the surgeon
had only to remotely check the smooth running
of the surgery and be ready to intervene in the
case where the robotized platform would not be
able to perform one of the surgery's steps or he
would judge that a human intervention is
necessary.
7 CONCLUSION AND
PERSPECTIVES
Our work consisted, through this paper, in
introducing BROS, this new robotic platform
dedicated to the treatment of supracondylar humerus
fracture, and its contributions. BROS is a flexible
system since it may run under different operating
modes to meet the surgeon requirements and the
environment constraints: it is reconfigurable.
Through the simulation of a real case of BROS-
assisted surgery, we proved the usefulness of this
robotic platform to avoid the complications that may
be generated because of the blind pinning and
prevent the danger posed by the recurrent exposition
to radiations. We can, now, certify that BROS is an
innovating project which will be of a great help to
pediatric orthopedic surgeons. The next step is to
proceed to the real implementation of BROS using
the ABB robotic arms.
ACKNOWLEDGEMENTS
This research work is carried out within a
MOBIDOC PhD thesis of the PASRI program, EU-
funded and administered by ANPR (Tunisia). The
BROS national project is a collaboration between
the Children Hospital of Béchir Hamza (Tunis),
eHTC and INSAT (LISI Laboratory) in Tunisia. We
thank the medical staff, Prof.Dr.med. Mahmoud
Smida (Head of Child and Adolescent Orthopedics
Service) and Dr.med. Zied Jlalia, for their fruitful
collaboration and continuous medical support. A
second paper is submitted in the conference for the
modeling and verification of BROS.
REFERENCES
Arbelaez, P., Maire, M., Fowlkes, C., and Malik, J.
(2011).Contour detection and hierarchical image
segmentation. Pattern Analysis and Machine
Intelligence, IEEE Transactions on, 33(5):898–916.
Barton, K. L., Kaminsky, C. K., Green, D. W., Shean, C.
J., Kautz, S. M., and Skaggs, D. L. (2001). Reliability
of a modified gartland classification of supracondylar
humerus fractures. Journal of Pediatric Orthopaedics,
21(1):27–30.
Cardwell, M. An irb 120 robots picks and packs tubes of
hair color into boxes for l’oreal canada.
www.abb.com.
Cleary, K. and Nguyen, C. (2001). State of the art in
surgical robotics: clinical applications and technology
challenges. Computer Aided Surgery, 6(6):312–328.
Clein, N. W. (1954). How safe is x-ray and fluoroscopy
for the patient andthe doctor? The Journal of
pediatrics, 45(3):310–315.
Mikaelsson, P. and Curtis, M. (2009). Portrait-robot d'un
petit prodige: ABB présente son nouveau robot IRB
120 et son armoire de commande IRC5 Compact.
Revue ABB, (4), 39-41.
Connolly, C. (2009). Technology and applications of abb
robotstudio. Industrial Robot: An International
Journal, 36(6):540–545.
Emmerson, B. Irb 120 inserting thermoplastic trays in to
boxes for bdmo. www.abb.com.
Flynn, J. C., Matthews, J. G., Benoit, R. L., et al. (1974).
Blind pinning of displaced supracondylar fractures of
the humerus in children. J Bone Joint Surg Am,
56(2):263–72.
Gosens, T. and Bongers, K. J. (2003). Neurovascular
complications and functional outcome in displaced
supracondylar fractures of the humerus in children.
Injury, 34(4):267–273.
Grauman, K. and Darrell, T. (2005). Efficient image
matching with distributions of local invariant features.
In Computer Vision and Pattern Recognition, 2005.
CVPR 2005. IEEE Computer Society Conference on,
volume 2, pages 627–634 vol. 2.
Haque, M. U., Shufflebarger, H. L., OBrien, M., and
Macagno, A. (2006). Radiation exposure during
pedicle screw placement in adolescent idiopathic
scoliosis: is fluoroscopy safe? Spine, 31(21):2516–
2520.
Judet, J. (1953). Traitement des fractures sus-condyliennes
transversales de l'humérus chez l'enfant. Rev Chir
Orthop, 39:199–212.
Kwoh, Y. S., Hou, J., Jonckheere, E. A., and Hayati, S.
(1988). A robot with improved absolute positioning
accuracy for ct guided stereotactic brain surgery.
Biomedical Engineering, IEEE Transactions on,
35(2):153–160.
Lagrange, J. and Rigault, P. (1962). Fractures
supracondyliennes. Rev Chir Orthop, 48:337–414.
Landin, L. A. (1983). Fracture patterns in children:
Analysis of 8,682 fractures with special reference to
incidence, etiology and secular changes in a swedish
HEALTHINF2015-InternationalConferenceonHealthInformatics
162