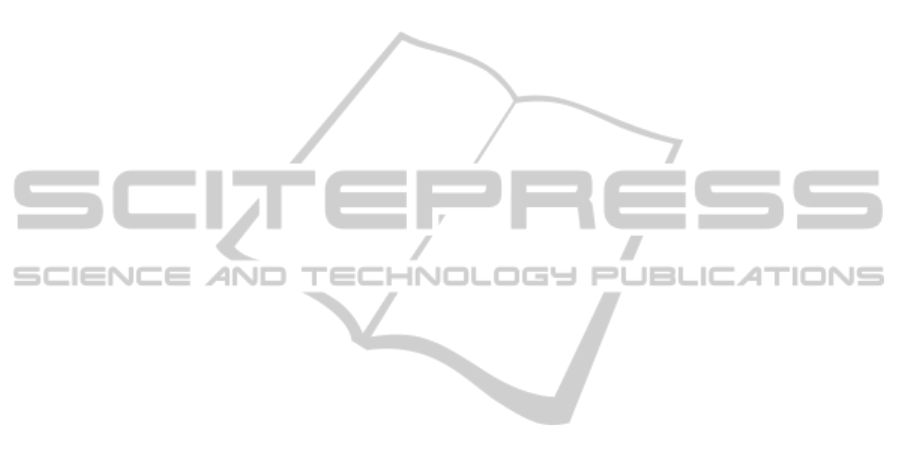
companies, with the aim of increasing their
competitiveness.
4 SUMMARY
The simulation experiments presented above showed
that there are many areas of opportunity at each of
the poultry stages. Strategic indicators were taken
from the poultry value chain to assess their impact
and to establish initial cause-effect relationships that
could improve the overall results of operations in the
flocks and poultry farms for the production of
chicken meat. The final objective is to meet the
needs of consumers, and to increase the
competitiveness of the poultry sector to conquer new
markets.
For the first strategic indicator, the production of
fertile eggs, it is observed based on the input
variables, that the number of birds that begin at the
stage of breeding, the fertility rates, egg hatching
and the percentage of defects are major factors that
influence a high yield. The evaluation of the density
of birds in the stands, allowed us to evaluate the bird
comfort in their living space which has a direct
relationship with the number of birds at the start of
the simulation, and the square meters available for
birds in production. The main objective is to find
the right balance between these two variables for the
optimization of the poultry chain. The third strategic
indicator is mortality, which is set according to the
assumptions of the system under study. The input
variables directly affecting this indicator are: the
number of birds at the start, the available area for
breeding flocks, egg production, and broiler chicken.
For broiler chicken an important factor of great
weight is the evolution of birds in the first week of
the cycle, which directly affects the performance of
broiler houses at the end of the production of
chicken meat. The conversion is a strategic indicator
directly related to the growing stage, which is
affected by the mortality that occurs early in the
cycle. This indicator is also closely related to the
welfare of birds in the flocks, which requires control
and care of various factors, such as the climate and
the health of birds. For the purposes of this research,
the number of variables and indicators are the most
representative of a poultry operation. However,
there is a wide spectrum of research to be addressed
in subsequent projects. Finally, for the cost of
production of chicken meat kilograms, the mortality
behavior in the first week of the broiler’s cycle is the
main factor that directly affects the direct and
indirect feed costs of poultry operations.
5 CONCLUSIONS
Simulation is a good tool to get started and provide a
basis for holistic solutions. The simulation model
developed focuses on the core part of the supply
chain to evaluate strategic poultry production
opportunities areas for taking decisions to improve
the system-wide integrated poultry from producers
to consumers. The poultry industry faces challenges
with the opening of global markets. The simulation
model provides an effective mathematical support to
improve the growth of Mexican poultry companies
and their production operations at all levels.
REFERENCES
Aviagen, (2001), Objetivos de Rendimientos de
Reproductoras Ross 308, USA: Aviagen Incorporated,
pp. 2-10.
Calderón, L (2008), Ph.D. Disssertation: Simulation model
of the value chain in the Mexican poultry industry.
Hernández Sampieri, Fernández Collado, y Baptista Lucio
(2003), Metodología de la Investigación, México:
Editorial McGraw-Hill.
RISTIC, M., (2004), Meat quality of organically produced
broilers, Rev. World Poultry, Vol. 20 No. 8 2004, pp.
30-31.
ROBBINS, S. (1994)., Administración: Teoría y Práctica,
México: Editorial Prentice Hall Hispanoamericana 4ta
Edición.
Sargent, R., (2004), Validation and Verification of
Simulation Models, 2004 Winter Simulation
Conference, pp. 17-26.
SOLARES, A. M. G., (2004), El ALCA y su
trascendencia para la avicultura: Visión
Latinoamericana, Rev. Avicultura Profesional, Vol.
22, No. 7/8 2004, pp. 28-29.
TAHA, H. A., (1992), Simulation with SIMNET II, 2da
Ed., SimTec Inc. Fayetteville, AR, USA.
TAHA, H. A., (2003), Operations Research an
Introduction, USA:7 Ed. Prentice Hall, pp. 645-673.
UNA, (2005), Monografía de la Industria Avícola
Mexicana 2005, http://www.una.org.mx, Unión
Nacional de Avicultores, 2005.
URRUTIA, S. (1999), El Broiler del año 2001, Revista
Avicultura Profesional, 15 Ed., pp. 23-28.
GeneralModelSimulationoftheMexicanPoultryValueChain
643