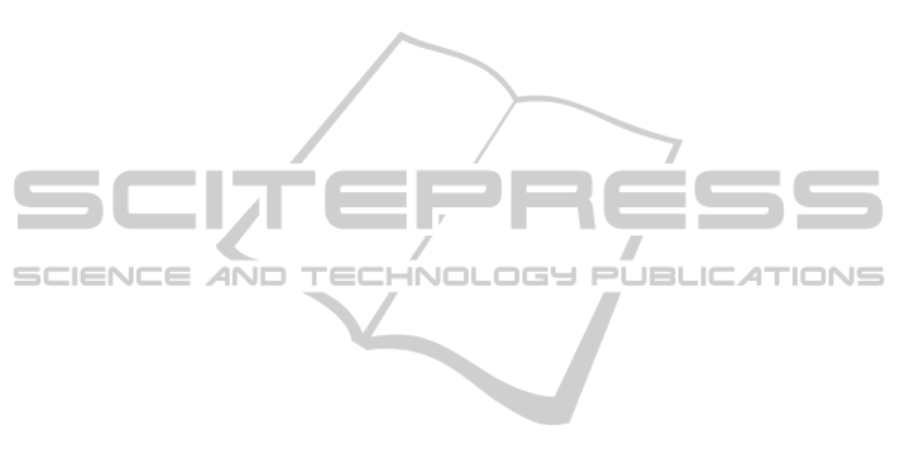
5 CONCLUSIONS
In this paper the impedance shaping control strategy
has been described and tested in a full rigid body as-
sembly real task with compliant support. The method
is capable to avoid force overshoots while allowing
to track a force reference using an estimate of the
environment dynamic parameters. The paper shows
the capability of the defined control strategy to satisfy
the desired requirements and compares the obtained
results to constant impedance controllers, that show
force overshoots and unstable behaviours.
Future work will extend the strategy to the rota-
tional DoFs and will investigate the optimal defini-
tion of the on-line tuning functions of the stiffness and
damping parameters and set-point gains. Moreover,
more challenging tasks will be considered (machin-
ing and surgical tasks).
ACKNOWLEDGEMENTS
This work has been partially supported by EC FP7
ACTIVE project (FP7-ICT-2009-6-270460). Opin-
ions or results expressed in this work are solely those
of the authors and do not necessarily represent those
of EC. The authors’d like to thank T. Dinon (CNR-
ITIA) for expertise, setup and experimental support.
REFERENCES
Colgate, E. and Hogan, N. (1989). An analysis of contact
instability in terms of passive physical equivalents. In
Robotics and Automation, 1989. Proceedings., 1989
IEEE International Conference on, pages 404–409.
Dubey, R. V., Chan, T. F., and Everett, S. E. (1997). Variable
damping impedance control of a bilateral telerobotic
system. Control Systems, IEEE, 17(1):37–45.
Ferraguti, F., Secchi, C., and Fantuzzi, C. (2013). A tank-
based approach to impedance control with variable
stiffness. In Proceedings of the 2013 International
Conference on Robotics and Automation (ICRA).
Fl
¨
ugge, W. (1975). Viscoelasticity. Springer New York.
Hogan, N. (1984). Impedance control: An approach to ma-
nipulation. In American Control Conference, 1984,
pages 304–313.
Ikeura, R. and Inooka, H. (1995). Variable impedance con-
trol of a robot for cooperation with a human. In
Robotics and Automation, 1995. Proceedings., 1995
IEEE International Conference on, volume 3, pages
3097–3102. IEEE.
Khatib, O. (1987). A unified approach for motion and force
control of robot manipulators: The operational space
formulation. Robotics and Automation, IEEE Journal
of, 3(1):43–53.
Lee, K. and Buss, M. (2000). Force tracking impedance
control with variable target stiffness. The Intern. Fed-
eration of Automatic Control, 16(1):6751–6756.
Mason, M. T. (1981). Compliance and force control for
computer controlled manipulators. Systems, Man and
Cybernetics, IEEE Transactions on, 11(6):418–432.
Park, J. H. and Cho, H. C. (1998). Impedance control
with varying stiffness for parallel-link manipulators.
In American Control Conference, 1998. Proceedings
of the 1998, volume 1, pages 478–482. IEEE.
Raibert, M. and Craig, J. (1981). Hybrid position/force con-
trol of manipulators. Journal of Dynamic Systems,
Measurement, and Control, 103(2):126–133.
Roveda, L., Vicentini, F., and Tosatti, L. M. (2013).
Deformation-tracking impedance control in interac-
tion with uncertain environments. In Intelligent
Robots and Systems (IROS), 2013 IEEE/RSJ Interna-
tional Conference, pages 1992–1997. IEEE.
Salisbury, J. K. (1980). Active stiffness control of a manipu-
lator in cartesian coordinates. In Decision and Control
including the Symposium on Adaptive Processes, 1980
19th IEEE Conference on, volume 19, pages 95–100.
Seraji, H. and Colbaugh, R. (1997). Force tracking in
impedance control. The International Journal of
Robotics Research, 16(1):97–117.
Villani, L., Canudas de Wit, C., and Brogliato, B. (1999).
An exponentially stable adaptive control for force and
position tracking of robot manipulators. Automatic
Control, IEEE Transactions on, 44(4):798–802.
Volpe, R. and Khosla, P. (1995). The equivalence of
second-order impedance control and proportional gain
explicit force control. The International journal of
robotics research, 14(6):574–589.
Yang, C., Ganesh, G., Haddadin, S., Parusel, S., Albu-
Schaeffer, A., and Burdet, E. (2011). Human-like
adaptation of force and impedance in stable and un-
stable interactions. Robotics, IEEE Transactions on,
27(5):918–930.
Yoshikawa, T. (1987). Dynamic hybrid position/force con-
trol of robot manipulators–description of hand con-
straints and calculation of joint driving force. Robotics
and Automation, IEEE Journal of, 3(5):386–392.
Yoshikawa, T. and Sudou, A. (1990). Dynamic hybrid po-
sition/force control of robot manipulators: On-line es-
timation of unknown constraint. In Hayward, V. and
Khatib, O., editors, Experimental Robotics I, volume
139 of Lecture Notes in Control and Information Sci-
ences, pages 116–134. Springer Berlin Heidelberg.
ICINCO2014-11thInternationalConferenceonInformaticsinControl,AutomationandRobotics
450