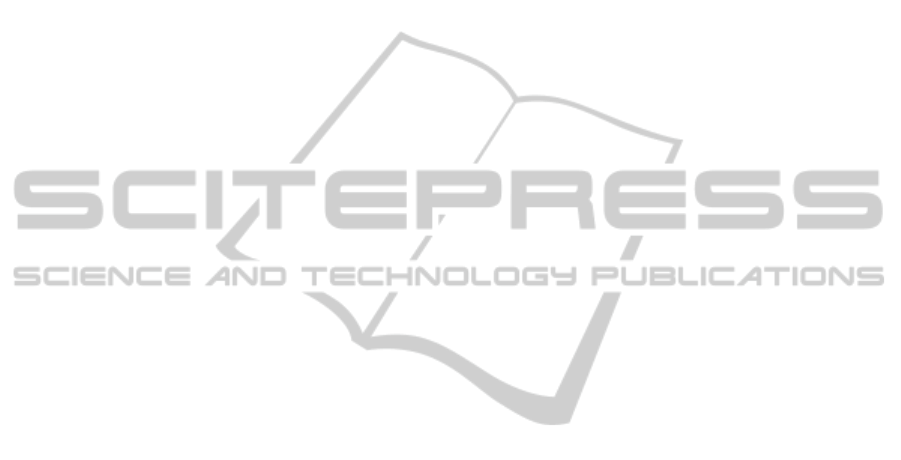
quality with minimum effort. Moreover, a short
product life cycle leads to frequent design changes.
This increases the challenge on the process designers
to setup fault free processes the first time right. The
macro simulation tool provides an opportunity to
analyse and optimize the machining processes.
In the macro simulation, the macroscopic
engagement is calculated on the discrete points of
the toolpath. Using these calculated macroscopic
engagement conditions, interpretations regarding the
real process conditions can be deduced. With an
extension of the macroscopic simulation, even
microscopic geometric process characteristics are
derived. Thus NC machining processes can be
characterized based on purely macroscopic and
microscopic geometrical parameters which are
derived using the macroscopic engagement
parameters. Further this process analysis is
independent of empirical process data.
Prediction of the critical sections on the toolpath,
where the process technology values can exceed the
allowable limits set during process design, is
possible. Through the proactive identification of the
critical process sections, their elimination at the
process design phase is possible before the
machining processes are executed, thereby reducing
potential expensive damages and machine
downtime. Moreover there is improvement in the
process reliability. Thus there is optimization in the
productivity of the NC machining processes.
ACKNOWLEDGEMENTS
The authors would like to thank the German
Research Foundation DFG for the support of the
depicted research within the Cluster of Excellence
"Integrative Production Technology for High-Wage
Countries".
REFERENCES
Altintas, Y., 2012, Manufacturing automation: Metal
cutting mechanics, machine tool vibrations, and CNC
design, 2nd edn., Cambridge University Press,
Cambridge, New York.
Bouzakis, K.-D., Michailidis, N., Gerardis, S.,
Katirtzoglou, G., Lili, E., Pappa, M., Brizuela, M.,
Garcia-Luis, A. & Cremer, R., 2008, ‘Correlation of
the impact resistance of variously doped CrAlN PVD
coatings with their cutting performance in milling
aerospace alloys’, Surface and Coatings Technology
203(5-7), 781–785.
Choi, B.K. & Jerard, R.B., 1998, Sculptured surface
machining: Theory and applications, Kluwer
Academic, Dordrecht, London.
Degner, W., Ham, N. C., Untersuchungen beim spanen
mit kleinen spanungsdicken, Fertigungstechnik und
Betrieb 13 (1973), 523 – 528.
Gey, C., 2002, Prozessauslegung für das Flankenfräsen
von Titan, VDI-Verl., Düsseldorf.
Hoischen, H., 2003, Technisches Zeichnen: Grundlagen,
Normen, Beispiele, darstellende Geometrie ; ein Lehr-
, Übungs- und Nachschlagebuch für Schule,
Umschulung, Studium und Praxis, 29th edn.,
Cornelsen Girardet, Berlin.
Klocke, F., 2011, Manufacturing Processes, Springer,
Berlin, Heidelberg, New York.
Kronenberg, M., 1969, Grundzüge der Zerspanungslehre:
Theorie und Praxis der Zerspanung für Bau und
Betrieb von Werkzeugmaschinen, 2nd edn., Springer,
Berlin [etc.].
Lazoglu, I. & Liang, S. Y., 2000, ‘Modeling of Ball-End
Milling Forces With Cutter Axis Inclination’, Journal
of Manufacturing Science and Engineering 122(1), 3.
Meinecke, M., 2009, Prozessauslegung zum fünfachsigen
zirkularen Schruppfräsen von Titanlegierungen,
Apprimus-Verl., Aachen.
Minoufekr, M., Glasmacher, L., Adams, O., ‘Macroscopic
Simulation of Multi-axis Machining Processes’, 10th
International Conference on Informatics in Control,
Automation and Robotics (ICINCO 2013), 505–516.
Ozturk, E., Tunc, L. T. & Budak, E., 2009, ‘Investigation
of lead and tilt angle effects in 5-axis ball-end milling
processes’, International Journal of Machine Tools
and Manufacture 49(14), 1053–1062.
Schug, P. et al, 2012, Durchgängige CAx-Prozessketten,
Forschung an der Werkzeugbau Akademie, Apprimus,
Aachen.
Zabel, A., 2010, Prozesssimulation in der Zerspanung,
Vulkan-Verlag, Dortmund.
ICINCO2014-11thInternationalConferenceonInformaticsinControl,AutomationandRobotics
670