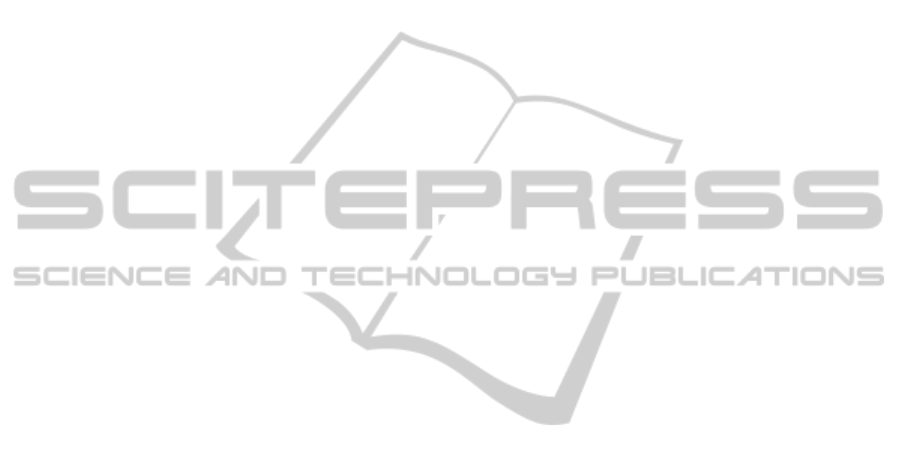
of a range of parameters. Section 3 describes the ex-
perimental data sets gathered for evaluation purposes,
while Section 4 presents the multiple linear regres-
sion ET estimation method. Section 5 presents the
results obtained through training and testing the esti-
mator. Finally, Section 6 concludes the paper.
2 RELATED WORK
Traditionally, vehicle HVAC systems control cabin
air temperature and humidity to a target set-point.
However, it has long been established that ther-
mal comfort is influenced by a variety of factors
in addition to air temperature, such as mean radi-
ant temperature, relative air velocity, relative hu-
midity, metabolic rate and clothing thermal resis-
tance (Fanger, 1973), (Gagge et al., 1967). More-
over, it is known that occupants feel comfortable over
a range of temperatures rather than at one specific
temperature (Fanger, 1973), (ANSI/ASHRAE, 2004),
(Singh et al., 2010). Estimating the level of passen-
ger comfort allows generating the exact amount of
energy needed, instead of wasting additional energy
by warming-up or cooling-down the whole cabin to
a certain set-point temperature. It can therefore be
concluded that the traditional approach is not opti-
mal with regards to ensuring comfort and energy ef-
ficiency. This indicates that in order to develop im-
proved HVAC control algorithms, there is a need to
1) sense more than just air temperature and 2) utilise
thermal comfort estimates for cabin occupants in the
control feedback loop.
ET is formally defined as the uniform tempera-
ture of the imaginary enclosure with air velocity equal
to zero in which a person will exchange the same
dry heat by radiation and convection as in the actual
non-uniform environment (SAE Journal, 2012). In-
tuitively, ET corresponds more closely to the human
sensation of environmental temperature than air tem-
perature alone. ET is an accurate predictor for ther-
mal comfort (Mayer and Schwab, 1999), (Curran et
al., 2010), (Mola et al., 2004), which integrates the ef-
fect of air temperature, mean radiant temperature and
relative air velocity. However, its direct measurement
can be intrusive, expensive and bulky. An alternative
to measuring ET is to estimate it from measurements
made at more convenient locations.
A variety of learning based models have been cre-
ated for the remote estimation of several parameters
in different environments. Mehnert et al. (2000), for
example, used a multiple linear regression to estimate
average skin temperature from parameters such as air
temperature, mean radiant temperature, air velocity,
metabolic rate, rectal temperature and partial vapour
pressure. Buller et al. (2010) developed an estima-
tor of human core body temperature using Kalman
filters, with only heart rate as input. Lee (2007) de-
veloped an artificial neural network for car cabin air
temperature prediction from 17 inputs, such as direct
sun intensity, air temperature outside the car, outside
air velocity and ventilation temperature.
Similar to the work presented in this paper, Mola
et al. (2001) developed an ET estimation model that
can be used to control the car cabin environment. A
series of trials in a controlled environment were per-
formed to identify the estimator, during which a ther-
mal manikin occupied the driver seat and measured
overall ET. The cabin air temperature, HVAC outlet
air temperature, external air temperature and mean ra-
diant temperature were also recorded. Of these mea-
sured parameters, mean radiant temperature, HVAC
outlet air temperature and air velocity were found to
allow the best estimate of ET. A linear mathemati-
cal expression was inferred for estimating ET. The
method was only assessed qualitatively and it was
concluded to successfully drive HVAC control. A
downside of this method is the fact that only one sen-
sor was used to measure the cabin temperature, while
different air temperature sensor locations within the
cabin can increase the estimator’s accuracy (Hintea et
al., 2011). Moreover, the data used for training and
testing the system came from controlled trials, leav-
ing open the question of how well it would perform in
realistic driving scenarios.
There are several gaps in the state of the art that
this paper tries to fill: 1) using a large number of sen-
sors for data gathering as this enables optimisation of
sensor location (Hintea et al., 2011) and leads to a
more efficient estimator, 2) validating the estimator
on data gathered in a variety of conditions, not only
in stable, controlled environments and 3) quantifying
the ET estimation error for multiple occupant body
parts, rather than overall.
3 EXPERIMENTAL DATA
GATHERING
The training and testing of the algorithm implemented
here was based on experimentally gathered car cabin
data within a variety of conditions. Throughout all
113 trials, ET was monitored at eight locations (cor-
responding to head, chest, left lower arm, right lower
arm, left upper arm, right upper arm, thigh and calf)
using the INNOVA Flatman thermal manikin, shown
in Figure 1 (right), positioned in the front passenger
seat of the test car. Cabin air and surface tempera-
ICINCO2013-10thInternationalConferenceonInformaticsinControl,AutomationandRobotics
508