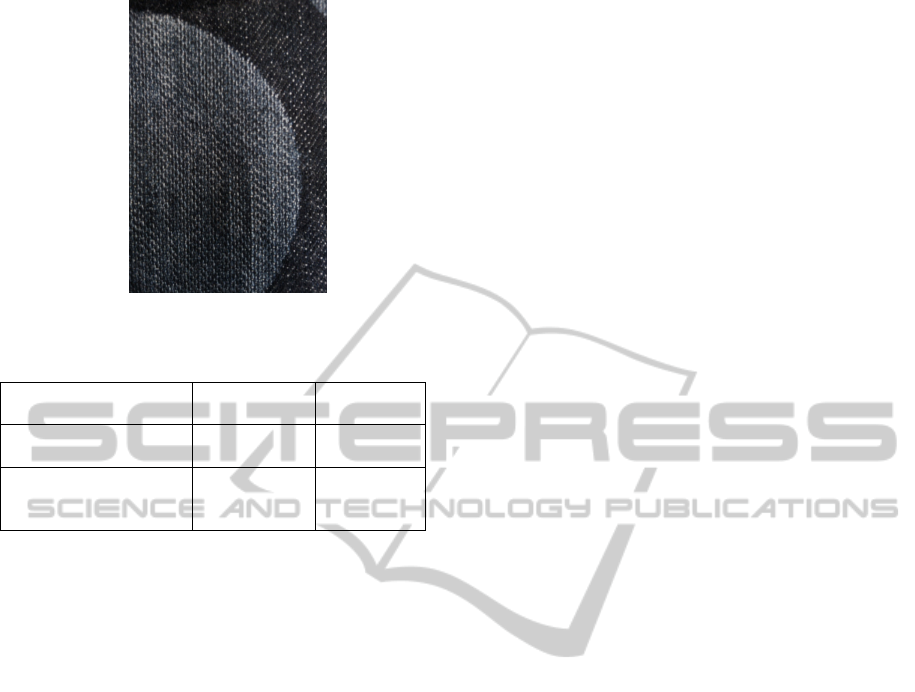
Figure 3: Line effect on 30 dpi laser engraving.
Table 1: Dimension of engraved circular pattern.
Sample Length (mm)
Width
(mm)
Circular pattern printed
in paper
200 200
Circular pattern laser-
engraved in denim
fabric
200 200
3.3 Dimensional Stability
Dimensional stability of fabric refers to the fabric
dimensional change after washing which can be
divided into two types, shrinkage and growth. The
causes of fabric shrinkage may be due to many
reasons, there are mainly two kind of shrinkage
happened on textile fabrics, relaxation shrinkage and
progressive shrinkage. Relaxation shrinkage is
happened on first time of washing, during
production of fabric, like weaving, fabric is under
tension by stretching by machines. This potential
energy is retained on the fabric due to friction
between yarns. During first washing of fabric,
because water and detergent can lubricate yarns, so
the tension released, and this cause the relaxation
shrinkage of fabric. Progressive shrinkage is the
continuous shrinkage of fabric during washing, it
can be caused by more than one reasons, like the
further relax of fabric tension, loss of elasticity of
fibre and felting effect on fabric. This kind of
shrinkage is not as much as relaxation shrinkage,
however, it keeps on happen in every washing.
Growth on fabric after washing, this problem can
also be caused by many factors, which mostly
affected by yarn. Over pre-shrinkage treatment to
fabric can cause relaxation growth of fabric. Low
twist yarn would tend to grow because of the poor
coherence of fibre cause easily lengthen when
pulling force is applied to the fabric.
Table 2 shows the dimensional change (in %) in
lengthwise and widthwise directions of laser-
engraved circular pattern in the denim fabric after
different washing cycles. In Table 2, the positive
number and negative number refer to fabric growth
and shrinkage in dimension respectively while “--“
means fabric damaged during washing and no data
can be measured.
3.3.1 Damage of Fabric during Washing
In the washing process, there are numbers of fabric
damaged after washing cycle. The possible reason
of the damaging of fabric was severe damage by
excess laser power. Most of the 100 dpi laser treated
fabrics could not withstand the washing cycle
because energy treated the fabric was too high
because the laser power of 100 dpi was at least 17.34
W/cm
2
. The strongest power of laser which could
withstand washing test was 80 dpi with pixel time
160μs which power intensity was 16.92 W/cm
2
.
3.3.2 Dimensional Change
In Table 2, the dimensional change of the circular
pattern was different in lengthwise and widthwise
directions. However, the widthwise direction has a
higher shrinkage. This may be due to the yarn in the
widthwise direction subjected to a higher tension
during the fabric production process. As a result,
during the washing process, a severe relaxation
shrinkage occurred. In general view for the samples
in Table 2, most of them was facing shrinkage in
their lengthwise and widthwise directions. The
relaxation shrinkage contributes most of the first
time shrinkage but the lengthwise direction did not
have much change in first washing cycle.
Denim fabric sample treated with high laser
power had less shrinkage because the fabric samples
were severely damaged by laser, so the fibre in the
yarn structure was damaged and no longer had high
coherence with each other, so when fabric was
washed, the yarn was started to relax and grow with
help of agitation and lubrication of water and
detergents. As there is a chance of dimensional
change of the laser- treated denim fabric, it would
have a risk of shape deformation in engraved pattern
in the denim fabric. So it is necessary to select the
laser processing parameters carefully to avoid the
shape deformation but with desired result.
DimensionalStabilityofCO2Laser-treatedDenimFabric
127