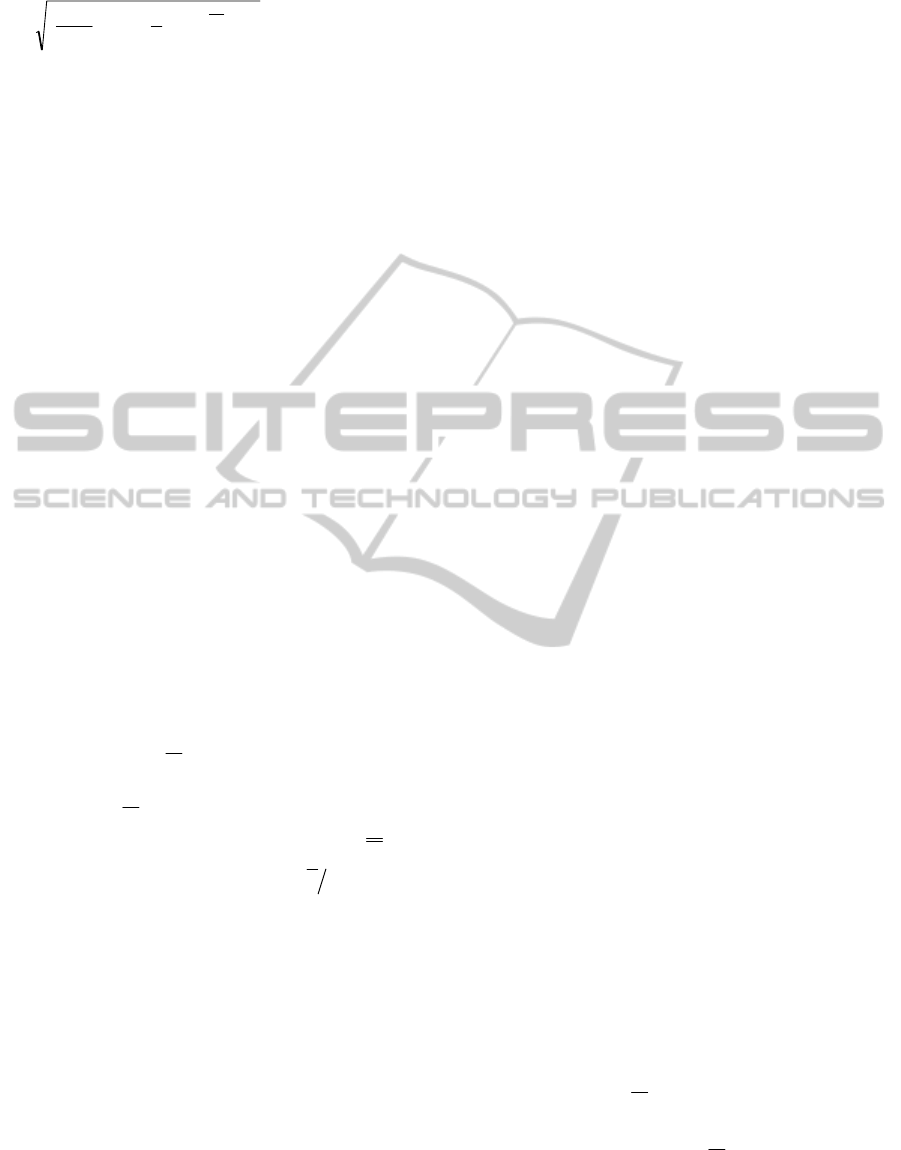
4 3
1
1
2
2
1
2
1
,,r,XX
r
S
r
r
S
r
rrr
(22)
A process is capable if simultaneously it verifies
both conditions
3
L
Q
and
3
U
Q
.
The implementation of the Q control charts
assumes that the quality characteristic X is
independent and Normally distributed.
5 CASE STUDIES
5.1 Example 1
In this section, the authors present an example of
application to a production system of components
(connection joints) of the wiring of electrical and
electronic systems of an automotive industry. Five
products (connection joints) were selected, and the
traction resistance is the quality characteristic to be
studied.
Initially (Phase 1 of the SPC) 50 samples (each
sample was constituted by 4 connection joints) were
obtained for the five products, and the whole
procedure was as follows:
Check whether the data from each component
(connection joint) were independent, i.e.,
ijij
x
where
2
0
,N~
, by using the
Estimated Autocorrelation Function (EACF)
and the Estimated Partial Autocorrelation
Function (EPACF).
Construction of
and S
control charts for
each product.
Analysis of
and S
control charts.
Estimation of the process parameters, u X
as
the estimator of the mean and
4
cS
as the
estimator of the process standard deviation.
Check the shape of the distributions of data for
the 5 products.
Analysis of the process capability of the five
processes, using the classic capacity indices
defined by equations (3), (4) and (5).
The implementation of Phase 1 of the SPC showed
that, for all the five processes:
1)
The data for the five quality characteristics are
independent (no significant autocorrelation).
2)
The processes were in-control, i.e., there were
only common causes of variation.
3)
The data of these five distributions were
approximately Normal; this study was made
based on the Kolmogorov-Smirnov test.
4)
The five processes had the capability to
produce according to specifications.
Table 4 shows the results obtained in the study of
the processes of the 5 components (connection
joints).
After the referred study in Phase 1, the authors
moved on to Phase 2 of the SPC. As there are
several products (5 types of connection joints), the
control charts
and
S
W are best fit for this
situation, since the distributions are approximately
Normal and process parameters have been estimated
in Phase 1. The authors built up the control charts
and
S
W , including all components (joints) in
chronological sequence. The statistics Z and W of
the sample i for the product j were determined from
the equations of Table 2. As the technical
specification concerning the traction resistance test
of all five components is unilateral (there is only the
LSL), the authors determined only the capability
index
L
Z for each product j, at time r, calculated
using equation (9). The control charts were built
using the Excel software. Figure 2 shows these
control charts constructed from 40 samples, taken in
chronological order, referring to the five
components. The analysis of these (monitoring)
control charts reveals that the five processes are
stable, i.e., the patterns are random for each
component, and their capability to meet technical
specifications remains at a satisfactory level.
5.2 Example 2
The second example relates to the production of two
food products, which are referenced by T1 and T2.
The weight of each pack is the quality characteristic
under study. The technical specification relating to
the weight of the product packages T1 is
g 10250
and the technical specification relating to the weight
of the product packages T2 is
g 15500
.
The number of packages of each product
produced is very low. In this case, data availability
was limited to only twelve samples of T1 and ten
samples of T2. Each sample was constituted by 8
packages.
As the amount of data was restricted, this second
study applied the
XQ
and
2
SQ
control charts;
once again, Excel software was used to determine
the values of the statistics
XQ
,
2
SQ
,
L
Q and
U
Q . The resulting control charts are shown in
Figure 3.
ProcessMonitoringinProductionSystemswithLargeDiversityofProducts
325