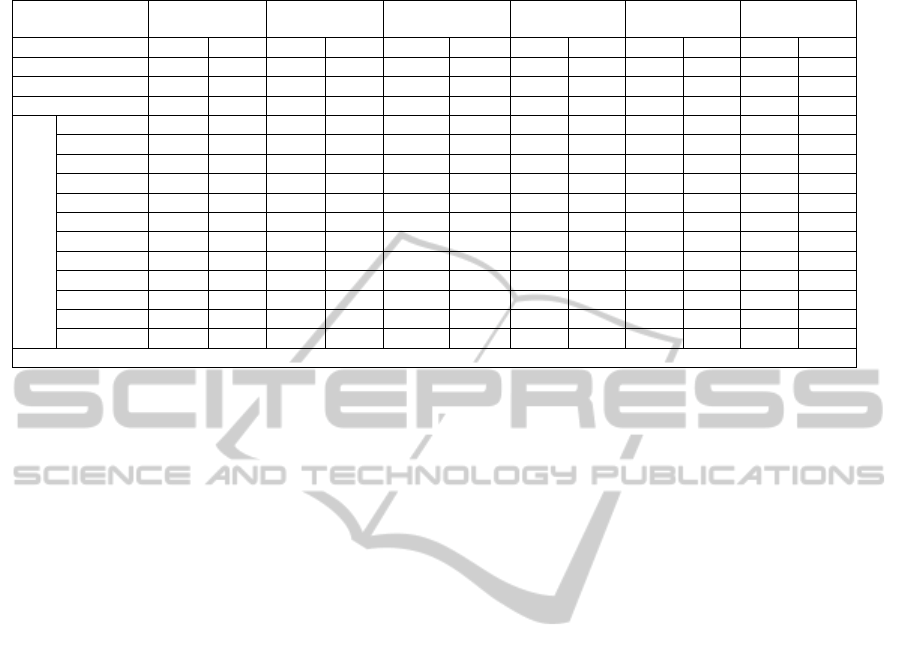
Table 3: Simulation Results.
Stream GPC CPC FG Tertiary Fuel Fuel Air
Condition 1 2 1 2 1 2 1 2 1 2 1 2
Temperature (K) 293 293 1663 1650 1373 1499 293 293 293 293 293 293
Pressure ( kPa) 120 120 120 120 120 120 120 120 120 120 120 120
Flow Rate (kg/s) 9.7 9.762 7.44 7.27 20.60 20.62 14.0 14.0 0.276 0.276 4.77 4.77
Components Flow Rates ( kg/s)
C 7.925 7.925 - - 0.24 - - - - - - -
C* 0.0 0.062 - - - - - - - - - -
CH
4
0.394 0.394 - - 0.242 - - - 0.276 0.276 - -
H
2
0.528 0.528 - - 0.314 0.4 - - - - - -
C
18
H
12
0.134 0.134 - - 0.072 - - - - - - -
H
2
O 0.51 0.51 - - 3.03 3.41 - - - - - -
N
2
- - - - 14.34 14.34 10.68 10.68 - - 3.66 3.66
CO
2
- - - - 1.84 2.24 - - - - - -
CO - - - - 0.43 0.077 - - - - - -
SO
2
- - - - 0.060 0.069 - - - - - -
S 0.211 0.211 0.169 - 0.0055 - - - - - - -
O
2
- - - - - 0.057 3.24 3.24 - - 11.53 11.53
1 Industrial data , 2 this study , C* carbon dust
flue gas where almost all volatile components and
carbon dust were oxidized adding more heat than
that of the industrial case. Moreover, the assumption
of adiabatic operation would add to the overall rise
in temperature.
5 CONCLUSIONS
This paper addressed the determination and
adjustment of the green petroleum coke calcination
in order to meet the allowable limits of the calcined
coke specifications. The methodology is to simulate
the processes that describe green petroleum coke
calcination. The simulation was based on using
physical and chemical reaction rate equations. The
results of the simulation were compared with actual
industrial rotary kiln data and there was a good
agreement. The methodology of rate-based
simulation described in this study may be used to
predict coke calcining kilns performance regardless
of the green coke composition. The sensitivity of the
kiln performance to changes in green coke
composition, fuel and tertiary air flow rates is left
for future work. Further validations using industrial
data are also necessary.
REFERENCES
ALBA, Private communication.
Bui, R. T., Perron, J., and Read, M., 1993. Model-based
optimization of the operation of the coke calcining
kiln, Carbon. 31; 7; 1139-1147.
Dernedde, E, Charette, A., Bourgeois, T., and Castonguay,
L., 1986. Kinetic Phenomena of the Volatiles in Ring
Furnaces. Light Met. Pcoc. Tech, Sess. AIME 105
th
Annual Meeting. 589.
Elkanzi, E. M., 2007, Simulation of the Coke Calcining
Processes in Rotary Kilns, Chemical Product and
Process Modeling, 2, 3, Article 20.
Howard, J. B., Williams, G. C., and Fine, D. H., 1973.
Kinetics of Carbon Monoxide Oxidation in Post flame
Gases. 14
th
International Symposium on Combustion.
975-985.
Ibrahim, H. A., and Ali, M. M., 2005. Effect of the
removal of sulphur and volatile matter on the true
density of petroleum coke. Periodica Polytechnica Ser
Chem. Eng. 49, 1, 19-24
Li, K. W., and Friday, J. R., 1974. Simulation of Coke
Calciners. Carbon. 12; 225-231.
Lu, C-W, and Wu, Y-J., 2004. Experimental and
theoretical investigations of rate coefficients of the
reaction S (
3
P) + O
2
in the temperature range 298-878
K). Journal of Chemical Physics. 121, 17, 8271-8278.
Lyons, J. W., Min, H. S., Parisot, P. F. and Paul, J. F.,
1962. Experimentation with a Wet-Process Rotary
Cement Kiln via the Analog Computer. Ind. Eng.
Chem. Process Des.Dev. 1; 1; 29-33.
Martins, A. Marcio., Oliveira, Leandro. S., and Franca,
Adriana. S., 1992. Modeling and Simulation of
Petroleum Coke Calcination in Rotary Kilns. Fuel.
80; 1611-1622.
Perron, J., Bui, R. T., and Nguyen, T. H., 1992.
Modelisation du four de calcination du coke de
petrole: 2- simulation du procede. Can. J. Chem.Eng.
70; 1120 - 1131.
Perron, J., and Bui, R. T., 1990. Rotary Cylinders: Solid
transport Prediction by Dimensional Rheological
Analysis. Can. J.Chem.Eng. 68; 61 - 68.
Srinivasan, R. J., Srirmulu, S., and Kulasekaran, S., 1988.
Mathematical modeling of fluidized bed combustion-
2: combustion of gases. Fuel. 77, 9/10, 1033-1043.
Rate-basedSimulationofCokeCalcinationinRotaryKilns
9