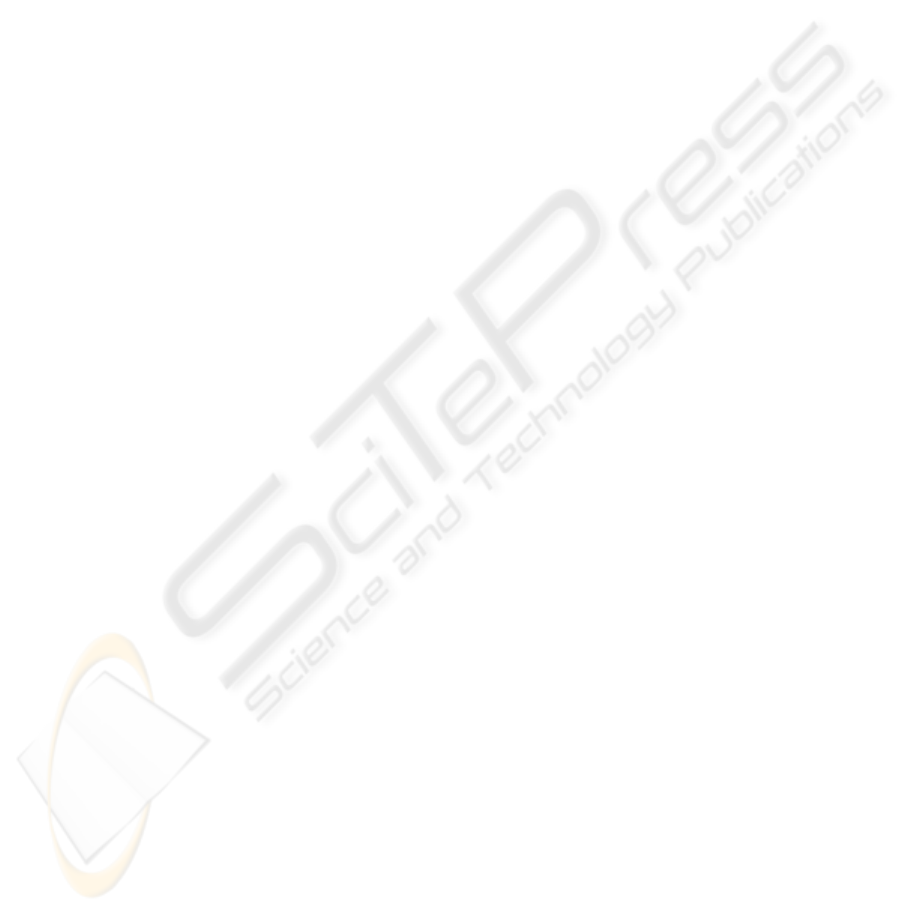
3. Consumption probability (PROB), i.e. the probability that a product is bought in a
store. PROB depends on various factors, the most important being the current
level of stock in the store and the remaining time before the end of the season.
These factors are not explicitly considered in the model, but they should be
considered to assess the proper PROB value.
4. Expected Markdown (%EM), i.e. the percentage of expected reduction of the price
of an article. The %EM should be higher when the product is expected to be sold
near the end of the season or in the end-of-season sale. The expected value of
%EM has been assessed through a real case and is 7.8%. This value already takes
into account the probability of selling a product with different discount prices and
the discount prices themselves.
5. Transport Cost (TC), i.e. the cost of transporting the goods from one destination to
another. The model considers only the extra-costs to transport the missing goods
to the store urgently. This cost is usually high, as the transport is performed with
an Express Courier. We refer to TC
ELT
in case of Lateral Trans-shipment from a
nearby store and TC
CWEC
in case of Central Warehouse Express Courier case. The
value of TC
ELT
is € 10; the value of TC
CWEC
is € 15 if the Central Warehouse is
located in the same country of the store and it is € 69 if the Central Warehouse is
not located in the same country of the store.
It is now possible to compute the payoff for each identified policy. As stated
before, the payoffs have been assessed by considering the differential costs and
benefits with respect to the situation in which the article is available in the store. If the
store manager decides to “do nothing” (DN), he tells the customer that the product is
not available in the store. Obviously, the payoff of this policy is always negative, as
the firm bears the stock-out cost without any additional income. The stock-out cost
can be simply expressed as a lost margin (%GM*PR), as shown in Formula 1.
P
DN
= – %GM*PR (1)
If the store manager decides to apply a Central Warehouse Express Courier
(CWEC) policy, he will allow the customer to book the product, that will be shipped
as soon as possible from the Central Warehouse through an Express Courier. Then,
the payoff of the CWEC policy considers only the transportation cost through an
Express Courier service from the central warehouse to the Receiver Store (TC
CWEC
),
since the article is indeed sold to the customer (cf. Formula 2).
P
CWEC
= – TC
CWEC
(2)
If RFId technology is in place, the store manager might also decide to apply the
Emergency Lateral Trans-shipment (ELT) policy. In this case the store manager will
allow the customer to book the product, which will be shipped as soon as possible
from a Supplier Store through an Express Courier. Then, the payoff of the ELT policy
is the transportation cost through an Express Courier service from a nearby store
TC
ELT
. Moreover, it is necessary to consider that the same article, if not shipped to the
Receiver Store, could be sold in the Supplier Store in the future with a probability
PROB. For this reason, the expected value of stock-out cost in the Supplier Store
should be considered (PROB*%GM*PR), reduced by the entity of the Expected
Markdown.
121