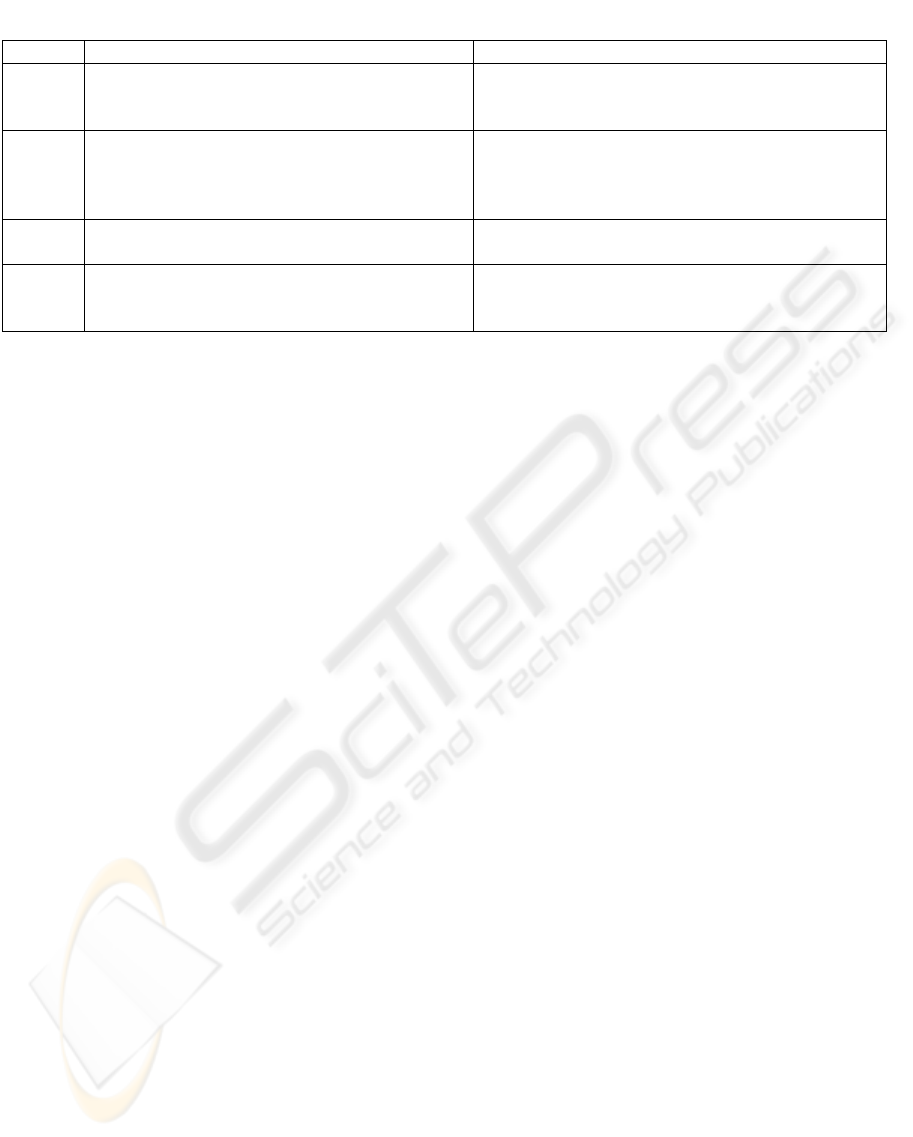
no customer records on inventory balance. Although
laboratory tests indicate that the remote monitoring
of small technical wholesale items is doable,
basically monitoring is best suited for the large and
medium sized items. For small items, the system
would require labels or other signals, which would
increase maintenance costs. As camera based
monitoring itself is not easily adopted to all item
sizes and types the camera monitoring would be at
its best as a part of an extensive remote monitoring
system as an expansion of systems capabilities.
Camera monitoring is at its best when items are
consumed sporadically in large volumes. Regular
on-site replenishment inspections meet the
customer's normal replenishment needs, and camera
monitoring assures that individual consumption
peaks do not cause shortages in the meantime. The
webcam system thus helps to increase the efficiency
of operative order-delivery processes through remote
monitoring and replenishment decisions.
7 FUTURE WORK
The correlation between camera monitoring and
replenishment efficiency should be studied from a
financial perspective. Does the arrangement of the
camera and shelves have an impact on the
replenishment efficiency (e.g. installing shelves side
by side and at centralised locations) or do efficient
camera monitoring and replenishment efficiency
contradict?
As this research study was part of the TEMO –
projects research topics (Häkkinen et al., 2007) and
as the result of the scale based system have been
really promising (Happonen and Salmela, 2007) a
new development research project is on preparation
for a integrated remote inventory monitoring system
which will allow many different monitoring methods
to be used side by side to deliver complete remote
inventory monitoring system.
REFERENCES
Bavister, S., 2002. Digitaalikuvaus ja kuvankäsittely,
WSOY.
Elvander, M.S., 2005. A theoretical mapping of the VMI
concept – A literature review. Report ISRN
LUTMDU/TMTD-4016--SE, Lund University. 40
pages.
Happonen, A.., Salmela. E., 2007. Automatic & unmanned
stock replenishment process using scales for
monitoring. In Webist’07, 3rd International
Conference on Web Information Systems and
Technologies. INSTICC Press.
Hedgecoe, J., 1992. The Photographer’s Handbook, Alfred
A. Knopf, New York, 3
rd
edition.
Holweg, M., Disney, S., Holmström, J., Småros, J., 2005.
Supply Chain Collaboration: Making Sense of the
Strategy Continuum, in European Management
Journal, Volume 23, Issue 2, Pages 170-181
Häkkinen, K., Hemilä, J., Uoti, M., Salmela, E.,
Happonen, A., Hämäläinen, H., Siniluhta, E.,
Nousiainen, J., Kärkkäinen, M., 2007. VMI
teollisuudessa – Teoriaa, teknologiaa ja sovelluksia,
VTT, Finland
Illumination Engineering Society of Finland. Publisment
no 9/1986. Valaistussuositukset/Sisävalaistus.
McClelland, D., Eismann, K., 2003. Real world digital
photography, Peachpit Press, Berkeley, 2
nd
edition.
Salmela, E., Happonen, A., 2007. Applicability of CPFR
on Inventory Replenishment Operation Model of Low-
value Items. Finnish Machinery Industry - Case
Study. In Proceedings of the 12th International
Symposium on Logistics (ISL 2007), Hungary
Vigtil, A., 2006. Exchange of advance demand
information in Vendor Managed Inventory. In
Proceedings of NOFOMA 2006.
Table 2: Image usability for inventory balance detection in different distances.
Range AXIS 207MW AXIS 2120
2 m Under 20 lux; some problems to “see” the amount
of items, because of shadows by boxes on top.
Other illumination levels are ok.
Under 20 lux; the image is not clear enough for
inventory monitoring. Higher illumination levels have
lower noise levels, but low resolution is a problem.
3 m
Under 20 lux; image inspection starts to be too
slow process. Other illumination levels are
problem free.
Under 100 lux; image not clear enough for inventory
monitoring. Higher illumination levels have lower
noise levels, but low resolution and distance from the
objects makes image inspection almost impossible.
4 m Under 20 lux; for industrial usability more light is
needed, 100 lux should be sufficient.
Low resolution and “high” distance limits AXIS 2120
in over 3 metres distances.
5 m Under 100 lux; problems because of shadows by
boxes on top. Maximum range for the resolution.
Produces usable images in over 100 lux levels.
As above.
IS WEBCAM PERFORMANCE SUFFICIENT FOR THE INVENTORY CONTROL OF INDUSTRIAL WHOLESALE
ITEMS WITH NO CUSTOMER INVENTORY BALANCE RECORDS? - Case: Technical Wholesale Items
511