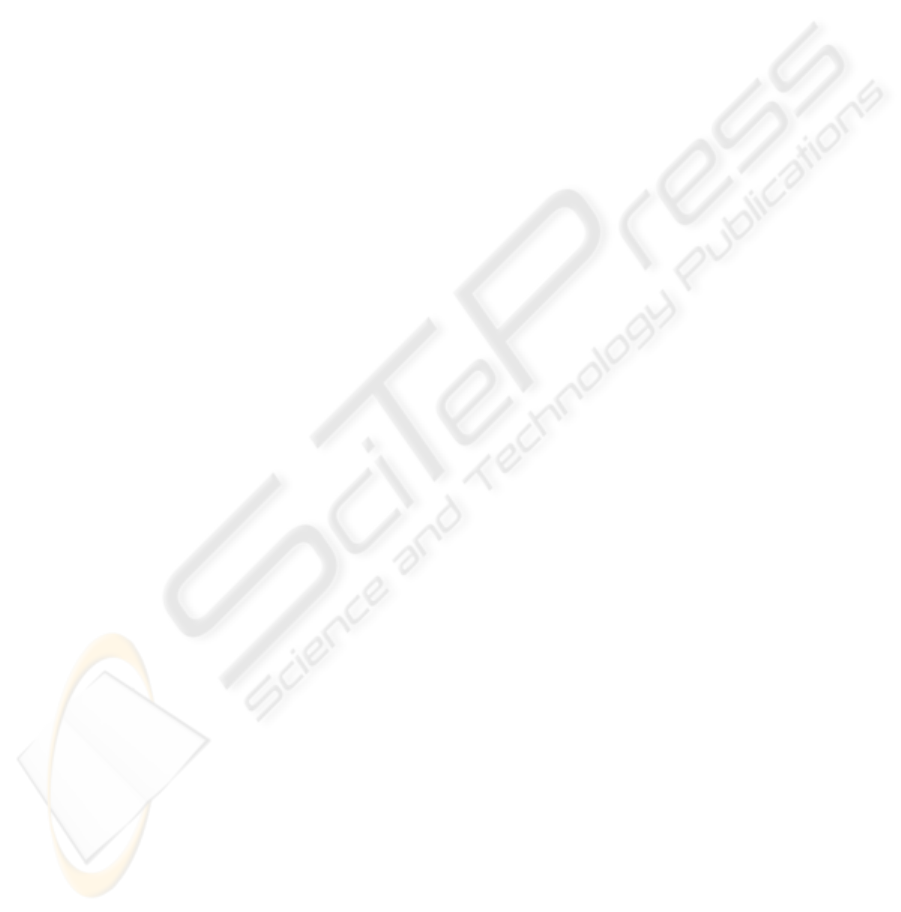
2 Background: Asset Tracking in the Rental Market
Plant rental companies operate in a highly-competitive market, providing a broad spec-
trum of items for their customers, ranging from mobile generators that can be the size
of a small car or a shipping container, to individual cables or boxes of tent pegs, leased
for periods of days or weeks. Although the logistical processes in such companies are
usually highly automated, with efficient call-centre based front offices, the nature of the
items being rented means they tend to be stored in large depots, or even fields. Further-
more, since many of the items are large and metallic, and some are stored inside walk-in
containers, there are challenges for any electromagnetic or line-of-sight communication
system deployed to support item handling.
Traditionally, paper-based processes are used to manage the dispatch and return
of rented items. Order sheets are printed from the order management system and car-
ried into the storage yards, where they are updated as required to reflect on-the-ground
knowledge and essential ad-hoc decisions about deployment made by experienced field
staff. This transition to paper introduces a significant dislocation in several respects.
Management lose visibility of activity and the disciplined automated processes can be
disrupted, leading to non-compliant behaviour by operations staff. Worse still, updates
from the paper sheets back into the automated logistics systems can take days, or in-
deed never be properly completed. Consequently, the tracking of rented assets becomes
somewhat hit-and-miss, and invariably errors occur that require manual rectification.
Spartan offers a tailorable computerised solution based on RFID tags affixed to the
rentable items, and hand-held wireless PDAs with integrated RFID scanners. Develop-
ing this system involved overcoming a number of significant problems, as described in
the next two sections. The advances described here are essential enabling steps for the
deployment of RFID technologies in other challenging environments. The Phalanx sys-
tem, which is at the core of Spartan’s software products, is now deployed at sites across
the UK, Europe and North America, with worldwide deployment planned for late 2007,
as a result of substantial contracts with major multi-national rental companies. In part-
nership with manufacturers of hand-held computers and the leading specialist software
houses producing order management systems for the rental market, Spartan are rev-
olutionising the business practises of an entire sector, exploiting RFID technology in
conjunction with their specialist sector know-how and software.
The integrated environment and platform addresses process control issues but offers
significant additional benefits. In particular, the reality of operations behaviour can be
captured for exploitation in the enterprise systems with minimal latency. Forms of in-
formation never normally seen in an ERP system, such as GPS and timing data, are also
made available and reports can be generated based on these new modalities. Further-
more, other technologies can be enabled by extension of the computer-based approach
into the operations domain. Modular design allows the system to be tailored to the
needs of the company, for example allowing a small amount of added telemetry, or a
simple warehouse management application to be integrated, in situations that do not
merit the cost of a full-function inventory management solution. This flexibility is the
key to maximising business value using an asset management system and is only possi-
ble because unified business processes are extended throughout the operational sphere
by the Phalanx software system.
76