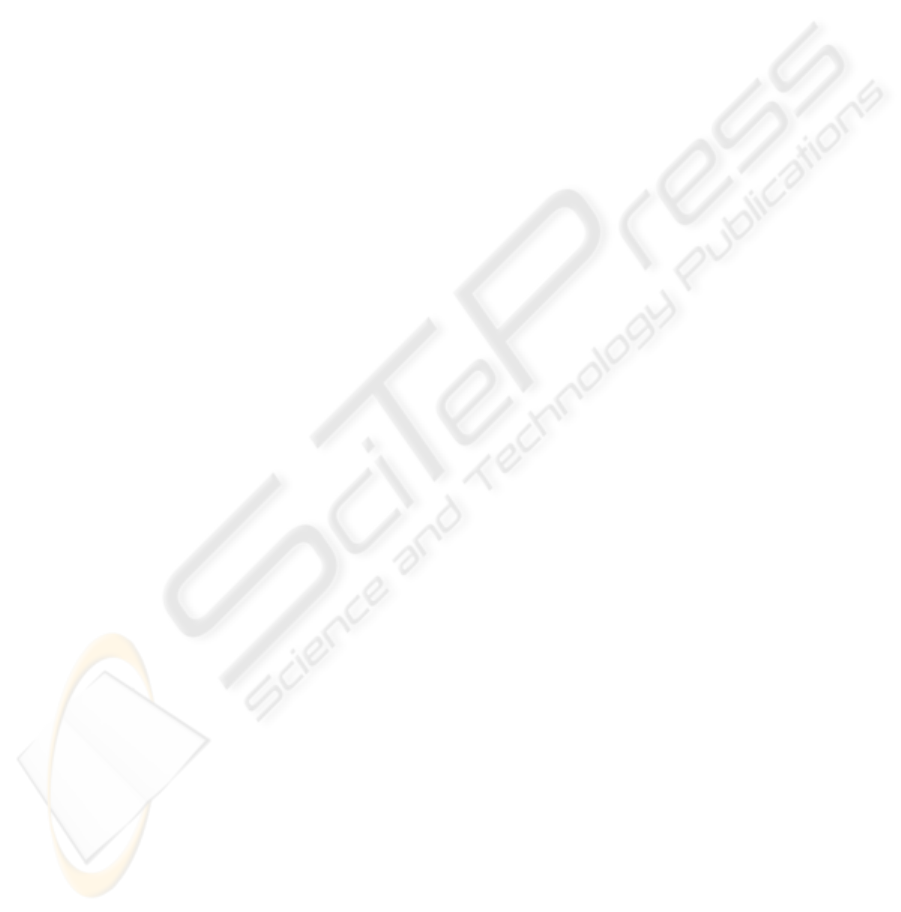
observer and with acceleration control loop,” in Conf.
Rec. ISIE’99, Slovenia, 1999, pp.1035-1040.
Gieras, J. F. and Piech, Z. J., 2001. Linear Synchronous
Motors: Transportation and Automation Systems. Boca
Raton, USA: CRC, 2001.
Hong, K. and Nam, K., 1998. ”A Load torque
compensation scheme under the speed measurement
delay,” IEEE Trans. Ind. Electron., vol. 4, no. 2, April
1998.
Hor, P. J., Zhu., Z. Q., Howe, D. and Rees-Jones, J.,
1998. “Minimization of cogging force in a linear
permanent magnet motor”, IEEE Trans. Magn., vol.
34, no. 5, pp. 3544-3547, Sept. 1998.
Hyun, D.-S., Jung, I.-S., Shim, J.-H. and Yoon, S.-B.,
1999. “Analysis of forces in a short primary type
permanent magnet linear synchronous motor,” IEEE
Trans. Energy Conversion, vol. 14, no. 4, pp. 1265-
1270, 1999.
Inoue, M. and Sato, K., 2000. “An approach to a suitable
stator length for minimizing the detent force of
permanent magnet linear synchronous motors,” IEEE
Trans. Magn., vol. 36, no. 4, pp. 1890-1893, July 2000.
Jung, S.-Y. and Jung, H.-K., 2002. ”Reduction of force
ripples in permanent magnet linear synchronous
motor,” Proceeding of International Conference on
Electrical Machines, Brugge, Belgium pp.452, Aug
2002.
Kim, B. K., Chung, W. K. and Oh, S. R., 2002.
“Disturbance Observer Based Approach to the Design
of Sliding Mode Controller for High Performance
Positioning Systems,” 15th IFAC World Congress on
Automatic Control, 2002.
Lee, S.-H. and Song, J.-B., 2001. “Acceleration estimator
for low-velocity and low-acceleration regions based on
encoder position data,” IEEE/ASME Trans.
Mechatron., vol. 6, no. 1, March 2001.
Morimoto, S., Sanada, M. and Takeda, Y., 1997. “Interior
Permanent Magnet Synchronous Motor for High
Performance Drives,” IEEE Trans. Ind. Applicat., vol.
33, Issue 4, July-Aug. 1997.
Olsson, H., Åström, K. J., de Wit, C. C., Gäfvert, M. and
Olsson, P. L., 1998. “Friction Models and Friction
Compensation,” European Journal of Control, 1998,
Vol.4, No.3.
Otten, G., de Vries, T.J.A., van Amorengen, J., Rankers,
A.M. and Gaal, E.W., 1997. “Linear motor motion
control using a learning feedforward controller,”
IEEE/ASME Trans. Mechatron., vol. 2, no. 3, pp. 179-
187, 1997.
Tan, K. K., Huang, S. N. and Lee, T. H., 2002. ”Robust
adaptive numerical compensation for friction and force
ripple in permanent-magnet linear motors,” IEEE
Trans. Magn., vol. 38, no. 1, January 2002.
Zhu, Z. Q., Xia, Z. P., Howe, D. and Mellor, P. H., 1997.
“Reduction of cogging force in slotless linear
permanent magnet motors”, Proc.IEEE Electr. Power
Appl., vol. 144, no. 4, pp. 277-282, July 1997.
ICINCO 2004 - ROBOTICS AND AUTOMATION
184