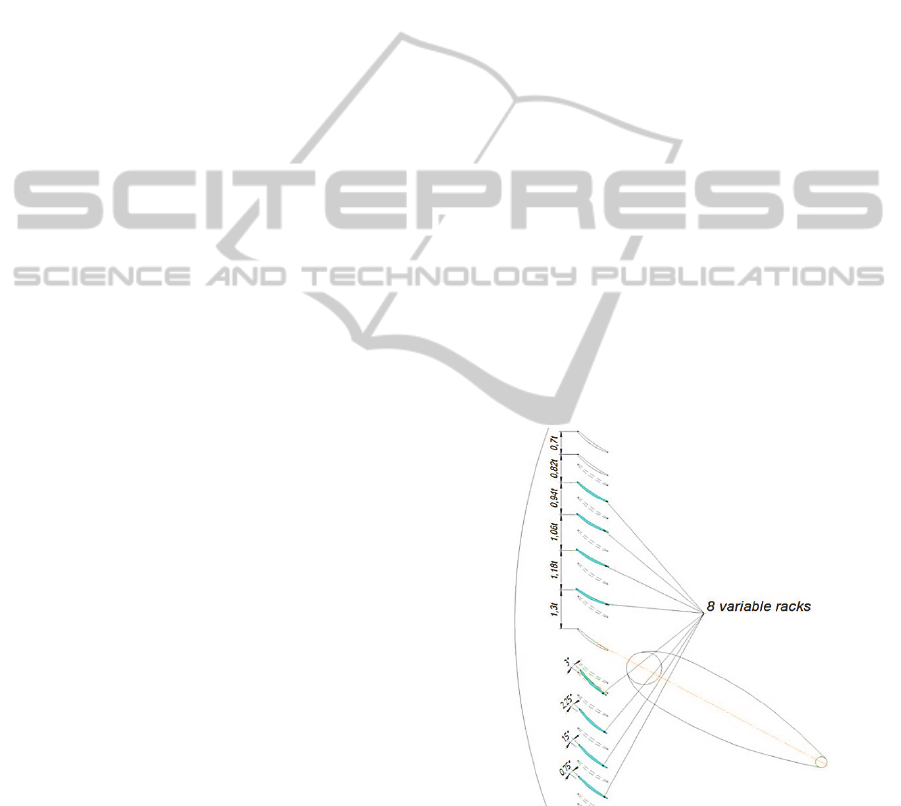
Seven racks of different cross-sections are
unevenly distributed in the flow passage of support
casing. These racks cause the circumferential
variation of the gas flow in gas-turbine engine flow
passage, which leads to increased dynamic stresses
in the fifth rotor wheel blades, as a consequence, to
its breakage (Figure 2).
As the number of support racks is 7, the blade
was detuned from the dangerous seventh harmonic
at the design stage. The natural frequency of the RW
blade vibrations is selected so that the resonance is
possible with the eighth harmonic and higher.
Seventh harmonic is beyond the engine operating
conditions. Experimental research revealed the
destruction of the rotor blade of compressor stage at
resonance with the 12
th
harmonic.
On the basis of the above-described method of
calculation of blade forced oscillations, the
maximum alternating stresses were defined in the
fifth stage rotor blade of IPC reference design
operating in the conditions of gas flow
circumferential distortion.
To reduce the circumferential distortion of the
flow, stagger angles and pitch of fifth stage guide
vanes were changed to non-uniform around the
circumference of the rotor wheel (Figure 3). At the
same time, CFD-calculation qualitatively coincides
with the experiment.
As a result, the optimal variant of the design was
chosen, in which the amplitude of the dangerous
12th harmonic was reduced by 2 times, while the
number of changeable guide vane (GV) blades was
equal to 14 (total blade number is 76).
4 EFFECT OF SUPPORT DESIGN
ON CIRCUMFERENTIAL
DISTORTION
4.1 Changing Angular Location of
Support Racks
Technologically, changing the stagger angle of the
guide vane blade is challenging, so it was decided to
change the configuration of the support rack.
Therefore, the experimental variant of support with
13 racks instead of standard support with seven
racks was considered at the next stage of the
research (Figure 4). The experimental tests were
conducted by JSC "Kuznetsov" (Samara, Russia) –
the enterprise of aviation and space propulsion
engineering. (JSC "Kuznetsov", 2014).
It was revealed that the mean amplitude of
dangerous 12th harmonic decreased by 2 times in
the computational studies (experimental data
confirm this). The coincidence of obtained results
with experimental data confirms the adequacy of
computational models and techniques. There was a
significant decrease in the amplitudes of all
dangerous harmonics.
The rack thickness, in which the engine systems
are located, and their angular disposition were
changed in the 13-racks experimental support.
Therefore, such support cannot be applied at
modernized engine. Consequently, one of the
conditions was to keep unchanged the racks 1, 3, 4,
and 7 of standard 7-racks the support (Figure 4)
when optimizing the angular arrangement of racks.
For this, the optimization technique of the
angular position of support racks was developed.
Angular position of racks was represented as a
periodic function. Function was provided in the form
of discrete data array containing the nominal
pressure before each rack, which was equal to one.
The array contained 180 values; each value
corresponded to the angle of the circumferential
location of the rack. Then the function value was 0 if
there was no the rack and the value was 1 if there
was rack is. Changing the angular arrangement of
free racks, decrease of dangerous harmonics
amplitude can be achieved.
Figure 3: The algorithm of introduction of different
stagger angle and pitch.
Reduction in the amplitude of the 12
th
harmonic
was performed using optimization methods
implemented in the software package IOSO
(Egorov, Kretinin, Leshchenko, Kuptzov, 2002.).
The goal of optimization was to decrease the
amplitudes of 10
th
and 12
th
harmonics.
AngularArrangementOptimizationoftheSupportRacksofGasTurbineEnginetoReducetheCircumferential
UnevennessofGasFlow
385