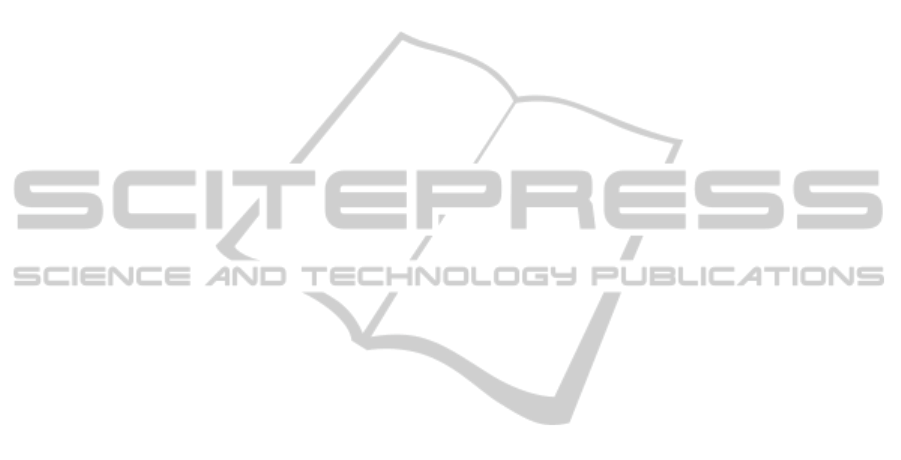
severe accident simulator, and all the software
interfaces including CSAMG.
3 COMPUTERIZED SEVERE
ACCIDENT MANAGEMENT
GUIDELINES
Severe accident management guideline is a paper-
based handbook for the NPP operators and
technicians to consult when the accident happened. It
requires the operators and technicians to be very
familiar with its content so as to locate the
information they need quickly. It would cost lots of
time and energy to learn the guidelines during the
training courses. And under the condition of severe
accident, due to the tension and pressure of operators,
they might be inefficient to look up through the
handbook. Compared to the paper based procedures,
Computerized Procedure System could improve the
performance of operators in the procedure application
(Lee et al., 2010). It also could reduce workload and
save time during the accidents (Yuji et al., 1996).
To develop the CSAMG, firstly, the AP1000
SAMG is investigated to learn the work mode of
operators and technicians during the accident; then
the requirements are analysed to provide the design
basis of CSAMG; next is the function design of
CSAMG. At the same time the prototype of CSAMG
is developed. At last is the test and validation. We are
in the stage of function design and prototype
development.
3.1 AP1000 SAMG
AP1000 SAMG consists of three major parts: (Zheng,
2012)
(1) Control Room Severe Accident Management
Guidelines (CR SAMG);
(2) Technical Support Centre Severe Accident
Management Guidelines (TSC SAMG);
(3) TSC Severe Challenge Response Guidelines
(TSC SCRG).
The CR SAMG is guided by the control room, while
the TSC SAMG and TSC SCRG are both guided by
the TSC. The CR SAMG consists of two separate
guidelines SACRG-1 and SACRG-2, which are
defined by the status of the Technical Support Centre
(TSC). SACRG-1 is the entry guideline from the
AP1000 EOP to the SAMG. SACRG-1 includes
many steps that are same as in the EOP. SACRG-2 is
intended to enhance the cooperation of the control
room and TSC. The primary responsibility of TSC is
evaluating the plant status and recommending
possible actions to mitigate the core damage. But if
the core damage occurs before TSC is functional, the
control room operators must response to the situation.
SACRG-1 is the guideline for this condition. When
the TSC becomes functional, the responsibility of
severe accident management would pass to the TSC.
The operators move to execute the SACRG-2.The
control room operators will remain in SACRG-2 until
the TSC decide to exit SAMG to other procedures.
The TSC SAMG and SCRG both can be divided
into two sections: diagnostics and relative
management strategies. These guidelines are used by
the TSC to evaluate the plant status and to
recommend the management strategies. The
diagnostics consist of two parts: a Diagnostic Flow
Chart (DFC) and a Severe Challenge Status Tree
(SCST).
The DFC specifies several key parameters to
monitor for diagnosis of plant status. The key
parameters are monitored in a continual periodic way
until all the parameters are in the safe region, so the
plant could be declared to be safe. If one of the
parameters is outside the range, the TSC should
evaluate the need to implement strategies to make the
parameter back into the safe range. The strategies are
specified in a set of seven corresponding procedures
called Severe Accident Guidelines (SAGs). It is
worthwhile to notice that the mitigation strategies can
have negative impacts. It is reasonable for the TSC to
decide not implement any actions.
The SCST is the other tool for diagnosis of
ongoing fission product releases and challenges to
fission product boundaries. In the SCST, some key
parameters are identified to be monitored too. The
main difference between the DFC and SCST is the
urgency of implementing the mitigation strategy. In
the DFC, the impacts of the strategy should be
evaluated by the TSC to determine whether to
implement the strategy or not. But in the SCST, due
to serious conditions, the strategy should be
implemented immediately without the evaluation of
the impact, because without the mitigation strategy,
the fission product is about to release.
The seven SAGs corresponding to the DFC
specify a systematic, logical evaluation of possible
mitigation strategies to a given parameter. The SAGs
helps the TSC staff identify the possibility of
implement, balance of positive and negative impacts,
symbol of the successful strategy, and long term
concern of the strategy.
The four SCGs corresponding to the SCST are
similar to the SAGs. The SCGs don’t need the
DevelopmentofComputerizedSevereAccidentManagementGuidelinesofAP1000NuclearPowerPlant
201