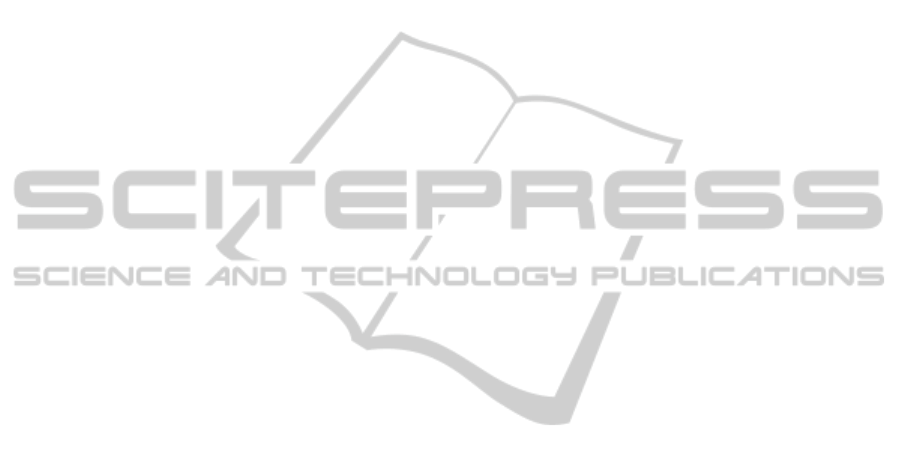
production processes and cycles in metal forming
industry was used. The system is user friendly and
adapts easily to new use cases. Performed
optimization allowed to design the thermal cycle,
which gives required volume fraction of phases in
the final product.
ACKNOWLEDGEMENTS
Financial assistance of the NCN, project no.
2011/03/B/ST8/06100, is acknowledged.
REFERENCES
Ambroziński, M., Polak, S., Gronostajski, Z., Kuziak, R.,
Chorzępa, W., Pietrzyk, M., 2015, Numeryczna
symulacja testu zderzeniowego z uwzględnieniem
umocnienia odkształceniowego w procesie
wytwarzania energochłonnego elementu samochodu
(Numerical simulation of the crash test accounting for
strain hardening introduced during the manufacturing
stage), Mechanik, 88, 92-96 (in Polish).
Górecki G., Kuziak R., Kwiaton N., Madej Ł., Pietrzyk
M., 2015, DP_builder - the computer system for the
design of the continuous annealing cycles for DP
steels, Computer Methods in Materials Science, 14, (in
press).
Gronostajski, Z., Niechajowicz, A., Polak, S., 2010.
Prospects for the use of new generation steel of the
AHSS type for collision energy absorbing
components, Archives of Metallurgy and Materials,
55, 221-230.
Hofmann, H., Mattissen, D., Schaumann, T.W., 2009.
Advanced cold rolled steels for automotive
applications, Steel Research International, 80, 22-28.
Kusiak, J., Rauch, Ł., Pietrzyk, M., 2015. Holistic
approach to optimal design of technology of materials
processing, Proc. XXXIV Verformungskundliches
Kolloquium, ed., Buchmayr, B., Zauchensee, 56-66.
Kuziak, R., Pietrzyk, M., 2011, Physical and numerical
simulation of the manufacturing chain for the DP steel
strips, Steel Research International, special edition
Conf. ICTP, Aachen, 756-761.
Madej Ł., Kuziak R., Mroczkowski M., Perzynski K.,
Libura W., Pietrzyk M., 2015, Development of the
multi scale model of cold rolling based on physical
and numerical investigation of ferritic-pearlitic steels,
Archives of Civil and Mechanical Engineering, 15,
doi.org/10.1016/j.acme.2015.02.010.
Matlock, D.K., Krauss, G., Speer, J.G., 2005. New
microalloyed steel applications for the automotive
sector, Materials Science Forum, 500-501, 87-96.
Pietrzyk, M., Kuziak, R., 2012. Modelling phase
transformations in steel, in: Microstructure evolution
in metal forming processes, eds, Lin, J., Balint, D.,
Pietrzyk, M., Woodhead Publishing, Oxford, 145-179.
Pietrzyk, M., Kuziak, R., Radwański, K., Szeliga, D.,
2014a. Physical and numerical simulation of the
continuous annealing of DP steel strips, Steel
Research International, 85, 99-111.
Pietrzyk M., Kusiak J., Kuziak R., Madej Ł., Szeliga D.,
Gołąb R., 2014b. Conventional and multiscale
modelling of microstructure evolution during laminar
cooling of DP steel strips, Metallurgical and Materials
Transactions B, 46B, 497-506.
Rauch, Ł., Kuziak, R., Pietrzyk, M., 2014a. From high
accuracy to high efficiency in simulations of
processing of Dual-Phase steels, Metallurgical and
Materials Transactions B, 45B, 497-506.
Rauch, Ł., Skiba, M., Kusiak, J., 2014b. Computer system
dedicated to optimization of production processes and
cycles in metal forming industry, Computer Methods
in Materials Science, 14, 3-12.
Sellars, C.M., 1979, Physical metallurgy of hot working.
In Hot working and forming processes, eds, Sellars
C.M., Davies G.J., The Metals Soc., London, 3-15.
Szeliga, D., Gawąd, J., Pietrzyk, M., Inverse analysis for
identification of rheological and friction models in
metal forming, Computer Methods in Applied
Mechanics and Engineering, 195, 2006, 6778-6798.
Szeliga, D., Sztangret, Ł., Kusiak, J., Pietrzyk, M., 2013.
Optimization as a support for design of hot rolling
technology of dual phase steel strips, Proc. 11th Conf.
NUMIFORM, AIP Publishing, Shenyang, 718-724.
SimulationsandOptimizationofManufacturingofAutomotiveParts
191