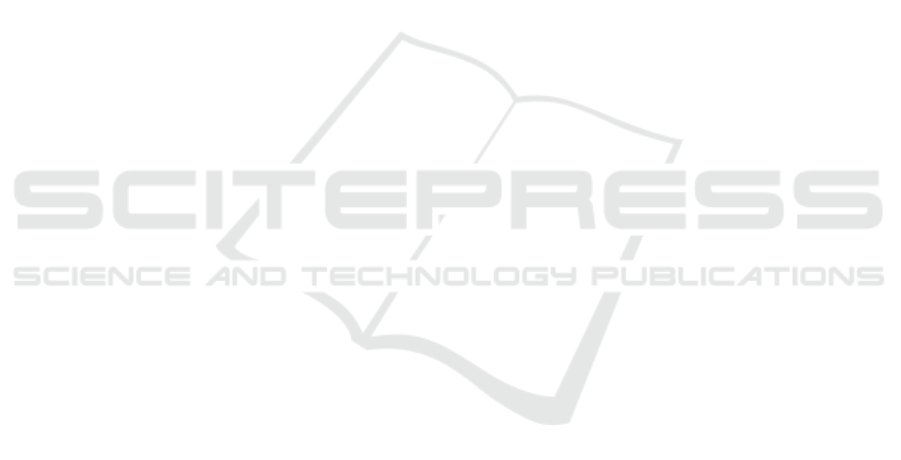
The Results of Gas Dynamic and Strength Improvement of
Turbocharger TK-32 Axial Turbine
Valery N. Matveev, Oleg V. Baturin, Grigorii M. Popov and Daria A. Kolmakova
Department of Theory of Engine for Flying Vehicles, Samara State Aerospace University (SSAU), 34,
Moskovskoye shosse,Samara, Russia
Keywords: Axial Turbine, Turbocharger, Gas Dynamic, Plastic Deformation, Efficiency, Blade, Strain-Stress State
Analysis.
Abstract: The results of strength and gas dynamic improvement of turbocharger TK-32 axial turbine are presented.
Turbocharger was manufactured by LLC “Penzadieselmash” (Penza, Russian) and is used as unit boost for
diesel locomotive. The goal of this work was to ensure turbine work capacity when rotor speed is increased
by 10% without efficiency reduction. The strain-stress state analysis indicated the region of high stresses on
rotor blade body at the level of 2/3 of root. These stresses exceed allowable values when rotor speed is
increased. The variant of peripheral rotor blade section tangential displacement, allowing to reduce the level
of stresses by 20%, was found. Gas dynamic calculation showed that variant of rotor blade modernization
results in an increase of efficiency by 0.4%. Also it was shown that the increase in turbine efficiency by 1%
can be reached if the number of rotor blades is reduced by 13%. This recommendation was implemented
and confirmed experimentally on a mass turbocharger TK-32.
1 INTRODUCTION
Turbocharger TK-32 (Figure 1) was developed at
LLC “Penzadieselmash” (Penza, Russian
Federation) for use on diesel generator 1А-9DG
manufactured by LLC “Kolomensky Zavod”.
During turbocharger’s operation there was a
necessity of engine forcing. As a result the
turbocharger operating condition was modified. In
particular, the rotor speed of the turbocharger
increased from 25500 to 28000 revolutions per
minute (rpm). In this regard LLC "Penzadieselmash"
applied for SSAU to assess the forcing effect on the
stress strain state of the turbine TK-32 and its gas-
dynamic efficiency, and make recommendations for
their improvement (Tikhonov, Matveev, 1982).
2 GAS DYNAMIC
CALCULATION OF TURBINE
BASIC DESIGN
Three-dimensional computational model of the flow
in the turbine stage, which includes zone of flow
around the nozzle guide vane (NGV), zone of flow
around the rotor wheel (RW) and free flow area at
the outlet of the turbine, was developed in Ansys
CFX program (ANSYS - Simulation Driven Product
Development, 2014). This model was used for
investigation of gas dynamic performances of the
existing turbocharger’s axial turbine. The flow
models of NGV and RW contain only one blade
passage for reducing required computer resources
and calculation time (Bonh, Heuer, Kusterer, 2005).
Therefore, the periodic boundary conditions were
implemented on lateral boundaries of the
computational domain (Figure 2).
Finite element mesh was created such as to
provide a value of y + no more than three. The total
number of elements was 250000 in the NGV mesh,
and 500000 elements in RW mesh. Tip clearance
was simulated when the RW mesh were created. The
value of tip clearance was taken as 1 mm in
accordance with the engineering drawing.
The following boundary conditions were set
during calculation:
mass flow rate (G = 5,34 kg/s), total
temperature (T* = 773 K) and flow direction
(perpendicular to the face) were set at the
computational domain’s inlet (NGV inlet);
595
Matveev V., Baturin O., Popov G. and Kolmakova D..
The Results of Gas Dynamic and Strength Improvement of Turbocharger TK-32 Axial Turbine.
DOI: 10.5220/0005042105950600
In Proceedings of the 4th International Conference on Simulation and Modeling Methodologies, Technologies and Applications (SIMULTECH-2014),
pages 595-600
ISBN: 978-989-758-038-3
Copyright
c
2014 SCITEPRESS (Science and Technology Publications, Lda.)