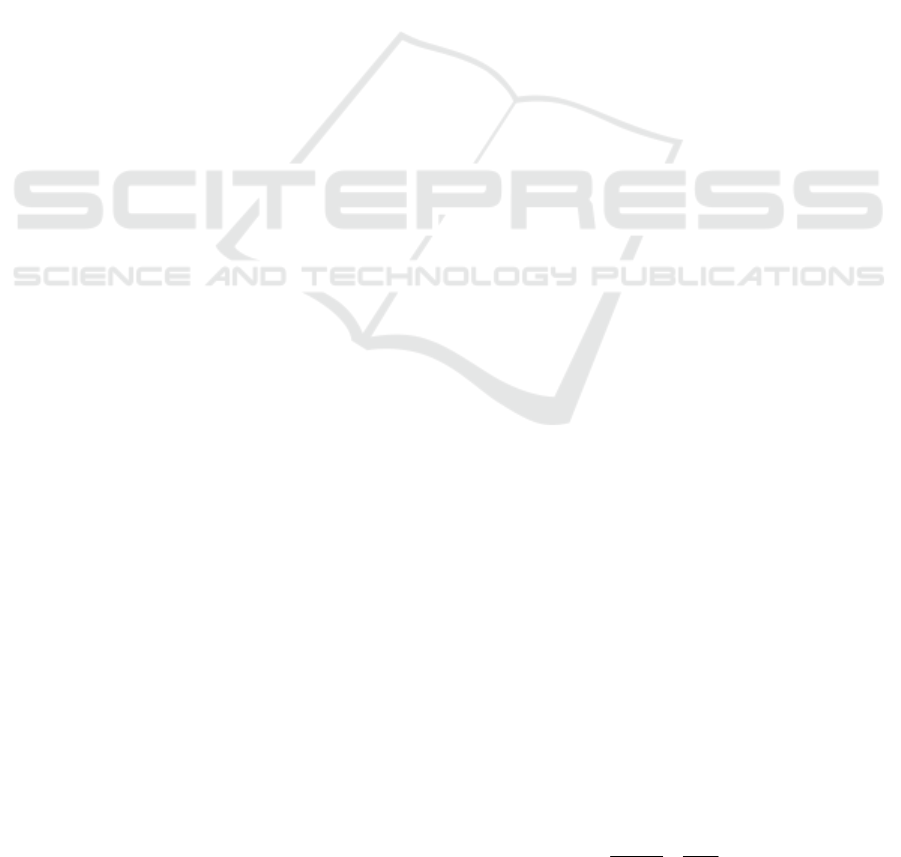
Robust Sliding Mode Control for a Roll-to-Roll Machine
Kuo-Ming Chang
1
and Yen-Yeu Lin
2
1
Department of Mechanical Engineering, National Kaohsiung University of Applied Sciences,
415 Chien-Kung Rd., Kaohsiung, Taiwan
2
Institute of Mechanical and Precision Engineering, National Kaohsiung University of Applied Sciences,
415 Chien-Kung Rd., Kaohsiung, Taiwan
Keywords: Roll-to-Roll Machine, Tension Control, Sliding Mode Control, Extended State Observer.
Abstract: This paper proposes a robust sliding mode controller, which is derived based on the extended state observer
and the sliding mode control techniques for a roll-to-roll machine to deal with the system uncertainty
problem of unknown system nonlinear functions, and external disturbances. It is worth noting that the
proposed sliding mode control scheme can be implemented without the condition that the system nonlinear
functions, and the upper bounds of external disturbances must be known in advance and it can achieve the
web transmitting speed and tension control goals satisfactorily, which are validated by numerical simulation
results.
1 INTRODUCTION
Roll-to-roll (R2R) processing is the process of
creating electronic devices on a roll of flexible
plastic or metal foil. R2R processing has the
advantages in fast and mass replication of
microstructures and it is a good fit for fabricating
devices based on flexible substrates. In recent years,
there has been much progress in the R2R processing
(Liang, 2003); (Makela et al., 2007); (Lo et al.,
2009).
To obtain a higher imprinting quality of the
microstructures in the R2R processing, the moving
web (PET substrate) should be under the conditions
that the web should be kept at a steady and fixed
speed and the web tension should be very small. A
moving web under insufficient tension cannot track
properly and may wrinkle the web, while excess
tension may result in web deformation or even a web
break. At the same time, unacceptable levels of
speed variation can cause detrimental variation in
tension. In view of the importance of both speed and
tension controls, a number of control schemes have
been proposed. Chang and Weng applied a
traditional sliding mode control method to control
the web speed and tension. Chen et al., (2004)
proposed a sliding mode control with an estimator
based on a recurrent neural network, which is used
to estimate system uncertainties. Dou and Wang
(2010) presented a robust H
∞
control strategy to
attenuate tension fluctuations when the system is
subject to disturbances and variations in speed or
other operating conditions. In this paper, a robust
sliding mode control is designed based on the
extended state observer and the sliding mode control
techniques for R2R machine to achieve the PET web
transmitting speed and tension control objectives in
the presence of unknown system uncertainties.
2 ROLL-TO-ROLL MACHINE
The configuration of the R2R equipment established
for conducting research into the tension and speed
controls of PET web is shown in Figure 1. Assume
that the web deformation in the thickness and width
directions are small compared to the length direction.
As a pull force is imposed on the web, the linear
density of web,
1
can be expressed by
1
1
L
(1)
where
L
and
are the length and linear density of
web, respectively before the web is elongated,
L
is the length deformation,
is the web strain in the
length direction.
405
Chang K. and Lin Y..
Robust Sliding Mode Control for a Roll-to-Roll Machine.
DOI: 10.5220/0004476304050409
In Proceedings of the 10th International Conference on Informatics in Control, Automation and Robotics (ICINCO-2013), pages 405-409
ISBN: 978-989-8565-70-9
Copyright
c
2013 SCITEPRESS (Science and Technology Publications, Lda.)