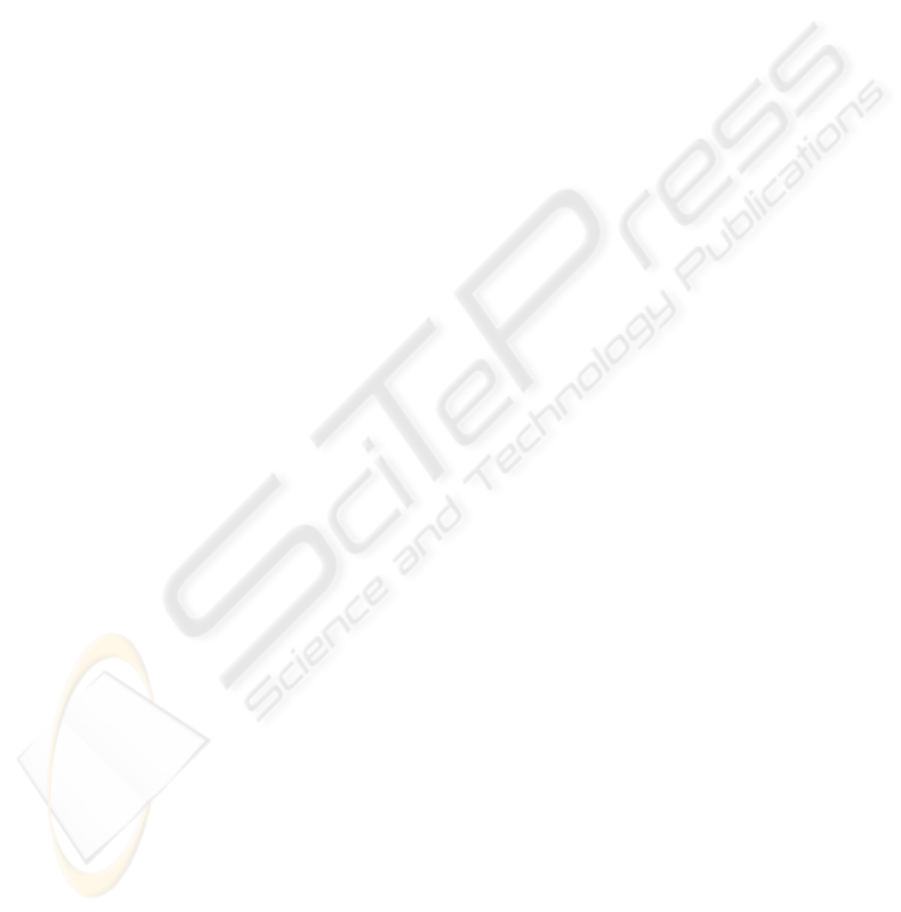
we attended to this work, a common and shared
welding design rule emerged from our instigation:
“A welded butt seam will be used when this welded
seam has to be checked. Such choice will make it
possible to validate the calculation hypothesis of
material continuity”.
An important corollary appeared immediately: “If
the specifications list or the calculation code do not
require checking the welded seam, then a less
expensive welded T-joint has to be chosen”.
This example shows that our presence as
observer (and knowledge management actor) gave
the experts the opportunity to share and define a
design rule at the interface of the three expertises.
An autonomous collaborative building of such a rule
requires a device (including areas, tools, methods…)
enabling experts to share their points of view. The
role of such a device is to help experts in
personalisation and codification strategies. We could
make the hypothesis of the relevance of the rule
justification as a means to support these strategies.
While the welding issue was the example we use
in this paper to put forward the necessity of a device
to allow codification and personalisation strategies,
we met other design situations (crane structure, hoist
system) where it could also be relevant.
5 CONCLUSIONS
In this paper, the analysis of a company producing
special machines has been conducted in order to
envisage how feasible knowledge management in
such context is. After discussing briefly the concepts
of information and knowledge and analysing the
present strategies relevant to implement a crucial
knowledge management approach, the context and
the investigations carried out have been described.
The observation analysis led us to some results
showing that a knowledge management approach is
relevant in the context of special machines.
First, in spite of the unique nature of each
project, the existence of numerous and multi-level
recurrences has been observed. This result is of great
importance to legitimise and to adjust the knowledge
management strategy.
Second, the recognized existence of experts and
the role they play are of major interest for defining
the knowledge management approach. This
participates in locating the crucial engineering
knowledge and gives some elements for defining the
required knowledge networks.
Third, we showed the necessity of a collaborative
device to allow codification and personalisation
strategies because it has been proved that different
experts in the same company should explicit
differently the same design rule.
To sum up, for knowledge management in a context
of special machine design, it is necessary to identify
expert people and crucial engineering knowledge, to
point out the recurrences and their level, and to give
means at disposal for confrontation between experts.
With this aim in view, works are in progress to
develop such an adapted collaborative device.
REFERENCES
Ahmed, S., Blessing, L., Wallace, K. M., 1999. The
relationships between data, information and
knowledge on a preliminary study of engineering
designers. In: ASME, Design Engoneering Technical
Conference. Las Vegas, 12-15 september 1999.
Beylier, C., Pourroy, F., and Villeneuve, F., 2008. A
collaboration-centred approach to manage engineering
knowledge: a case study of an engineering SME.
Journal of Engineering Design.
Briggs, H. C., 2006. Knowledge management in the
engineering design environment. In: AIAA,
Structures, Structural Dynamics,and Materials
Conference. Newport, USA, 1-4 may 2006.
Gardoni, M., Dudezert, A., 2005. Valuing Knowledge
Management Impact on Engineering Design
Activities. In: The Design Society, International
Conference on Engineering Design, Melbourne, 15-18
august 2005.
Grundstein, M., Rosenthal-Sabroux, C., 2008. GAMETH,
A Process Modeling Approach to Identify and Locate
Crucial Knowledge, In: Knowledge Generation,
Communication and Management. Orlando, USA,
june 29
th
- july 2
nd
, 2008.
Hansen M. T., Nohria N., Tierney T., 1999. What’s Your
Strategy for Managing Knowledge? Harvard Business
Review, 77(2), pp.106-116.
Matta, N., L’Hédi, Z., 2008. Applications of Knowledge
Engineering Approaches for Design. In A. Bernard, S.
Tichkiewitch, eds. Methods and Tools for Effective
Knowledge Life-Cycle-Management. Berlin: Springer.
pp.363-373.
Mentzas, G., Apostolou D., Young R., Abecker A. 2001.
Knowledge networking: a holistic solution for
leveraging corporate knowledge. Journal of
Knowledge Management, 5, pp.94-107.
Nonaka, I., Takeuchi, H., 1995. The Knowledge-Creating
Company. Oxford University Press. New-York.
Petroni, A., Colacino, P., 2008. Motivation strategies for
knowledge workers: evidences and challenges.
Journal of Thechnology Management & Innovation,
3(3), pp.21-29.
Wilson, T. D., 2002. The nonsense of knowledge
management. Information research, 8(1), paper n.144.
KMIS 2009 - International Conference on Knowledge Management and Information Sharing
128