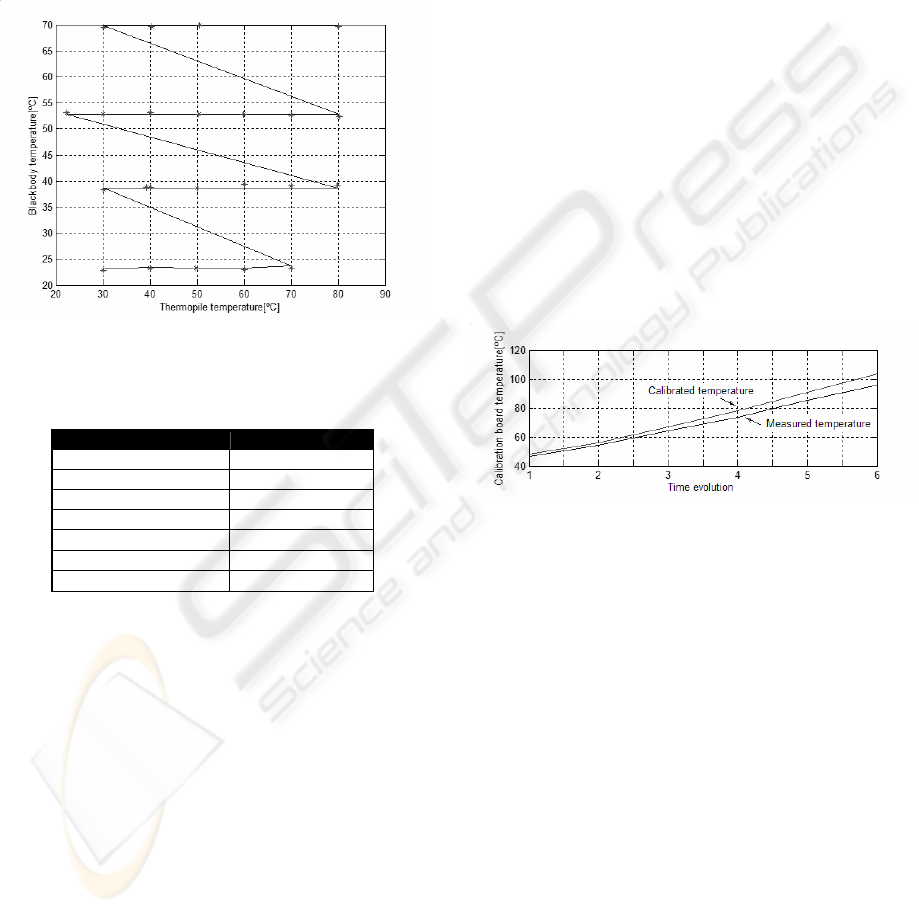
The first test tries to identify the value of those
unknown constants of the thermopile model, table 1.
In order to do it, different blackbody and thermopile
temperatures were consigned, figure 4, while the
flight calibration board was removed, which means
that
α
is equal to 0. Therefore, based on the energy
balance equation (2), where the energy terms are
known, a least-squares problem for the tested points
is established. Finally, the values of the constants,
which minimize the least-squares error, are obtained.
Figure 4: Real blackbody temperature (-) and estimated
blackbody temperature (*) after the identification process.
Table 1: Thermopile and model variables.
Variable Value
K
1
1
K
2
28.1695
K
3
128.4088W/K
Error
RMS
0.28K
α
0.34
Polynomial coefficients [1.0826 -4.0577]
β
0.415
The second test has been carried out with the
purpose of identifying the factor of the FOV
obstructed by the flight calibration board, this is α.
This value is an essential parameter, necessary for
the flight calibration process.
During the test, the thermopile and the
calibration board must be kept at ambient
temperature, to ensure that their temperatures are
homogeneous and stable. This requirement is
necessary due to the radiance of the flight calibration
has not previously calibrated, and in this way the
error introduced by this factor is avoided. The
blackbody temperature is set over the ambient
temperature. In order to avoid the thermopile
heating, due to the energy radiated by the blackbody,
an opaque surface was introduced in between. This
surface was removed during the measurement time
of bodies temperature and thermopile output. From
these data, the energy terms of equation (2) were
calculated, and we were able to solve for the values
of α, for each blackbody temperature. Finally, these
values of α were averaged in order to obtain a
unique value, table 1.
The third test pretends to know the real
temperature of the calibration board, which is
required to calculate its real radiometric emission.
The test consists of varying the flight calibration
board temperature over the temperature of the
thermopile, while the temperature of the thermopile
and the blackbody are kept constant.
In this case, for each calibration board
temperature, the blackbody and the thermopile
temperatures were collected, as well as the
thermopile’s output. Therefore, based on these data
and the energy valance equation (2), the radiometric
emissions of the flight calibration board are derived,
and from them the real temperatures, which were
compared with the measured temperatures to
determine the absolute calibration error, figure 5.
Also, a first order polynomial, interpolating this
error, has been obtained, table 1.
Figure 5: Temperature calibration error of the flight
calibration board.
The final test is dedicated to analyse the
behaviour of the in-flight calibration algorithm, after
depositing a certain among of dust over the
thermopile window, simulating Mars environment.
The test is divided in two different steps. In the
first one, the flight calibration algorithm is run for
different calibration board temperatures. The figure
6(Top) shows the obtained values of β, with and
without considering the previous calibration of the
calibration board. The data after calibration are more
stable, validating this calibration and reducing
algorithm error. As a result the average value of β is
shown, table 1.
The second step is dedicated to measure the
temperature of the blackbody from: the thermopile
output, the calibrated thermopile model, the
calculated value of the factor β due to dust
deposition. During the test, the temperature of the
blackbody was almost constant, while the
ICINCO 2007 - International Conference on Informatics in Control, Automation and Robotics
106